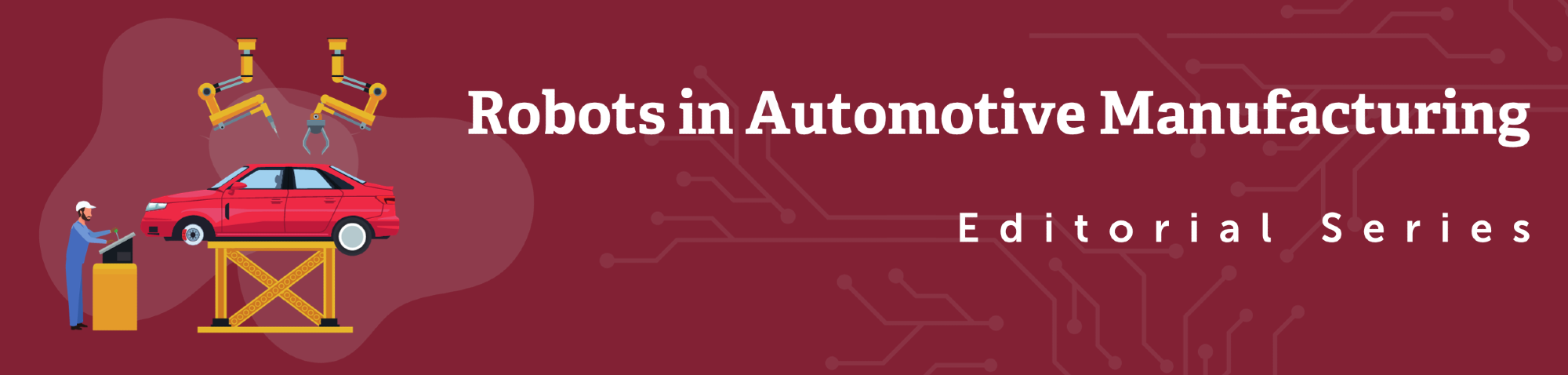
Over the past three decades, automotive welding robots have revolutionized the industry, making assembly lines faster, safer, and more cost-effective. Their integration into manufacturing, which began with General Motors' UNIMATE in 1967, gained momentum in the 1980s, setting a trend followed by other automotive companies.
Automotive robots have significantly improved safety by replacing humans in hazardous welding tasks and withstanding challenging conditions. In addition, they contribute to cost savings by boosting production capacity without requiring breaks or benefits.
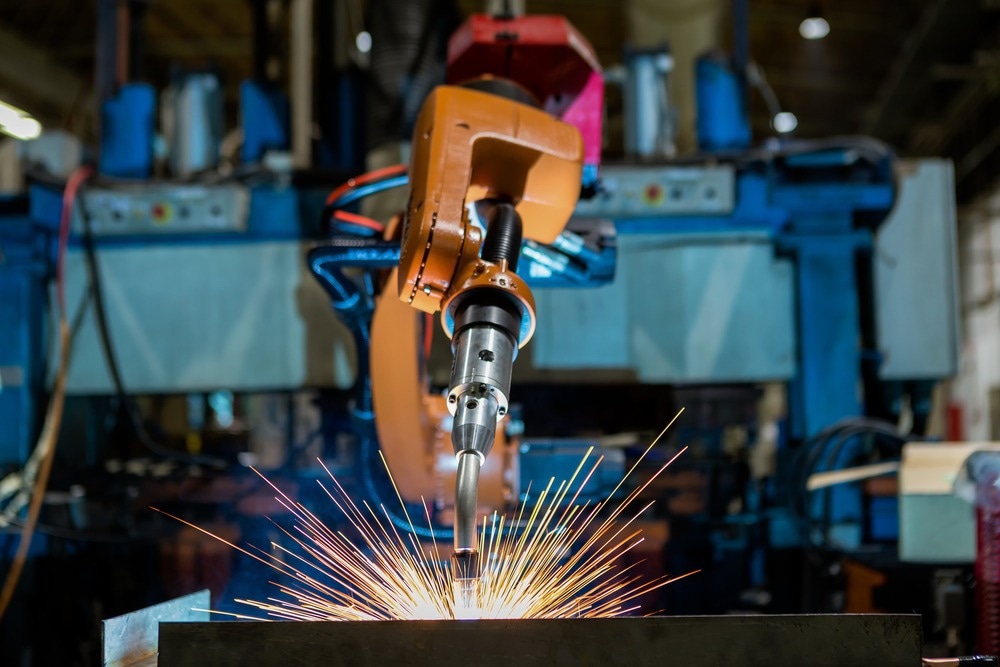
Image Credit: Factory_Easy/Shutterstock.com
In response to industry demands for lighter vehicles and more precise welding, robotic welders have emerged as key players in producing advanced, top-tier vehicles. As industry standards continue to tighten, robots consistently prove their ability to meet these demanding criteria efficiently and reliably.
Types of Robotic Welding Systems
Two main robotic welding systems are used in automotive manufacturing: semiautomatic and fully automatic.
Semiautomatic welding suits limited production, with manual part loading and operator oversight. In contrast, fully automatic welding is ideal for critical or repetitive tasks involving custom machines, automated processes, and optional quality checks with occasional operator presence.
These robotic systems primarily rely on three welding methods: Arc, Spot, and Laser.
Arc welding uses an electric arc for precise and versatile welding; spot welding (electric resistance welding) is ideal for thin metal sheets in body assembly, whereas laser welding offers deep welds in delicate components or tight spaces.
BMW's Robotic Revolution in Automotive Manufacturing
During the early years at BMW, manufacturing was hindered by manual welding, as each vehicle necessitated nearly 6000 spot welds, resulting in a meticulously slow process that was subject to numerous quality checks.
However, by the late 1990s, BMW had integrated robots into much of the welding process, particularly in producing Z3 models. This transition was considered a game-changer, and BMW has not looked back since.
The role of robots in the BMW body shop has continued to expand over the years. Initially comprising only 2 percent of the workforce in 1994, BMW's plant has transformed into a 98 percent automated facility, with robots now pivotal in handling intricate and repetitive welding tasks.
The incorporation of robots at BMW has boosted efficiency, reduced welder fatigue, and upgraded the body shop into a highly technical environment.
Flexible Welding Solutions by Valmet Automotive and Mapvision
Valmet Automotive and Mapvision have introduced a flexible welding cell demonstration, representing a significant advancement in automotive manufacturing toward a self-adjusting production process.
This pilot closed-loop welding cell, initiated as part of Valmet Automotive's Intelligent Manufacturing program, addresses the challenges posed by the evolving automotive industry, which demands greater flexibility and capacity optimization.
The key component of this welding cell is the Mapvision Smart Eye Cell, a versatile solution incorporating multi-camera technology, advanced inspection software, and adaptable hardware.
This integrated system allows robots to precisely measure component location and orientation before welding and to conduct quality checks at every production stage without using traditional jigs.
Robotic Investment Transforms Sertec's Automotive Manufacturing
Sertec's £500,000 investment in a robotic welding cell in 2017 represented a significant step forward for the company in automotive manufacturing. This advanced technology increased their production capacity, with the ability to manufacture around 80,000 rear seat assemblies annually for Toyota's Auris, and it also brought a higher degree of flexibility to their operations.
The robotic cell was designed to handle different seat structures required by Toyota, ensuring adaptability to changing production needs. Importantly, the robots in the cell delivered precise and high-quality welds, particularly vital for safety-critical components.
With integrated safety features and a monitoring system, the cell guarantees the integrity of welds on these crucial parts. This investment improved overall productivity and efficiency, enabled Sertec to meet customer demands effectively, and maintained high-quality standards in their automotive manufacturing processes.
Toyota's Welding Robots: Boosting Quality and Efficiency
In Toyota Motor Manufacturing UK's Weld Shop at Burnaston, Godzilla the Robot, among over 400 articulated machines, efficiently handles underbodies, lifting them from the factory's automated weld lines and placing them precisely for further production. They enable the precise customization of welds for each car, serving specific purposes such as component attachment, strength, rigidity, and anchorage for hinges and panels.
These robots achieve precision welds within a tenth of a millimeter and handle more than 90% of vehicle welding, underscoring their vital role in boosting productivity and quality in modern automotive manufacturing.
Kawasaki's Welding Robot: A Study in Reliability and Adaptability
In March 1997, Kawasaki Motors Manufacturing Corporation (KMM) deployed a Kawasaki J series robot to weld the Kawasaki Vulcan 800 motorcycle frame sides.
Remarkably, this dependable robot operated in KMM's facility for 22 years, adapting to welding various parts for different products. The robot provided consistent, high-quality welds with adaptive welding functionality, maintaining exceptional quality day in and day out.
After discontinuing Vulcan 800 motorcycle production, KMN reprogrammed the robot to weld steering shafts for the increasingly popular ATVs, demonstrating its flexibility and versatility.
Over its lifetime, the robot logged 38,390 hours, equivalent to two decades of eight-hour shifts, with just 57 maintenance entries. According to Chief Engineer Scott Gordon of KMM, the KMM achieved a rapid return on investment (ROI) within two years of its purchase, making it a cost-effective and reliable asset.
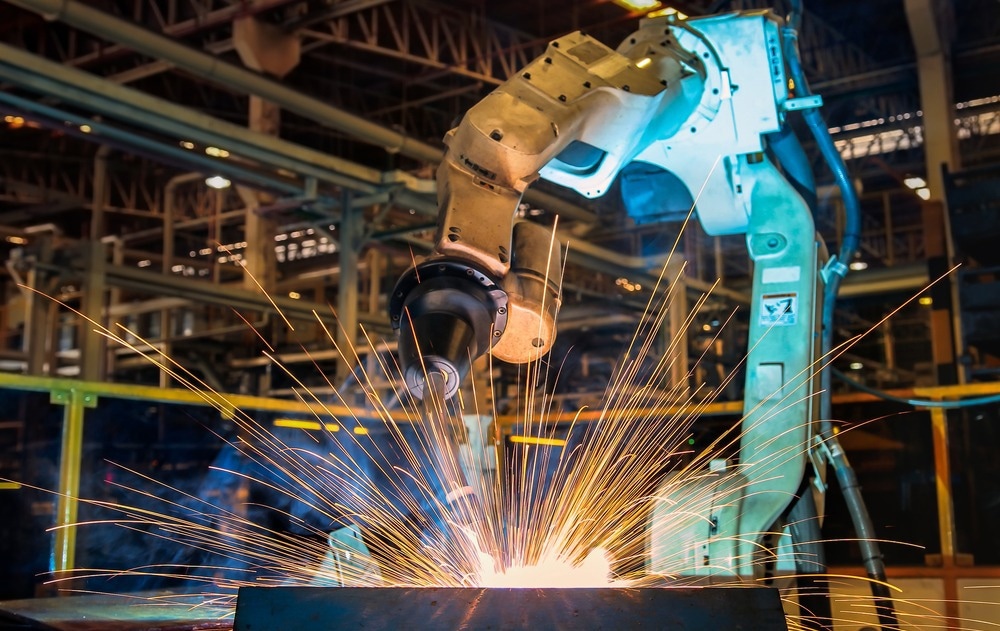
Image Credit: Factory_Easy/Shutterstock.com
GEDIA's Transition to Robotic Welding Improves Quality and Output
Automotive supplier GEDIA has implemented 57 FANUC robots for welding components as part of a plant redesign program. The goal was to achieve 100% repeatability in quantity and quality, improve working conditions, and create new jobs.
The decision to introduce robots was driven by GEDIA's positive prior experience with robotics and the need for stable product quality and advanced technologies.
These robots handle various processes, with 60% used for spot welding and the remaining 40% for pin welding, MAG/MIG welding, and workpiece movement. The introduction of robots has led to full automation of manufacturing processes, ensuring consistent quality and quantity. It has also provided greater flexibility to meet changing customer demands and produce different parts on a single machine.
The introduction of welding robots has led to the creation of approximately 200 new jobs while yielding cost savings in logistics, space rental, waste reduction, and enhanced safety measures.
Challenges and Future of Robotic Welding in The Automotive Industry
Robotic welding offers automotive manufacturers significant speed and precision advantages but presents initial cost challenges. Smaller companies may struggle with budget constraints, ongoing robot operation, and maintenance training expenses. In addition, the large physical footprint of robotic welding cells requires significant plant floor space, which could be constrained in smaller facilities.
However, as costs decrease and AI enhances flexibility, the adoption of robotic welding is expected to increase, especially in the production of electric vehicles. Smarter robots will adapt to new tasks without reprogramming, compact designs will access tight spaces, and innovations like hybrid welding systems and closed-loop control will improve efficiency and quality.
References and Further Reading
Robotrfq. (2012). Welding Robots Improve Automotive Parts. [Online]. Available at: https://www.robots.com/articles/welding-robots-improve-automotive-parts
Hardesty, A. (2017). Robots part of workforce evolution at BMW. [Online]. Available at: https://www.independentmail.com/story/news/local/2017/06/23/robotics-part/394124001/
Mikael Mäki. (2022). Valmet automotive and Mapvision introduce a flexible welding robot cell pilot. [Online]. Available at: https://www.valmet-automotive.com/media/valmet-automotive-and-mapvision-introduce-a-flexible-welding-robot-cell-pilot/
Williamson, J. (2017). Car supplier invests in new £500,000 robot welding cell. [Online]. Available at: https://www.themanufacturer.com/articles/car-supplier-invests-in-new-500000-robot-welding-cell/
Biddle, A. (2017). TMUK's 25 Objects – 18: Godzilla the Robot. [Online]. Available at: https://mag.toyota.co.uk/toyota-manufacturing-25-objects-godzilla-robot/
Kawasaki Robotics. (2023). Case Study "Reliable Robot Welds for More Than 20 Years". [Online]. Available at: https://kawasakirobotics.com/asia-oceania/case-studies/reliable-robot-welds-for-more-than-20-years/
FANUC. (2023). Automotive supplier GEDIA uses 57 FANUC robots for welding components. [Online]. Available at: https://www.fanuc.eu/il/en/customer-cases/welding-automotive-components
Disclaimer: The views expressed here are those of the author expressed in their private capacity and do not necessarily represent the views of AZoM.com Limited T/A AZoNetwork the owner and operator of this website. This disclaimer forms part of the Terms and conditions of use of this website.