Sponsored by CavitarReviewed by Louis CastelSep 30 2022
Using welding cameras for real-time visual monitoring of welding processes is becoming a more prominent and common process monitoring method.
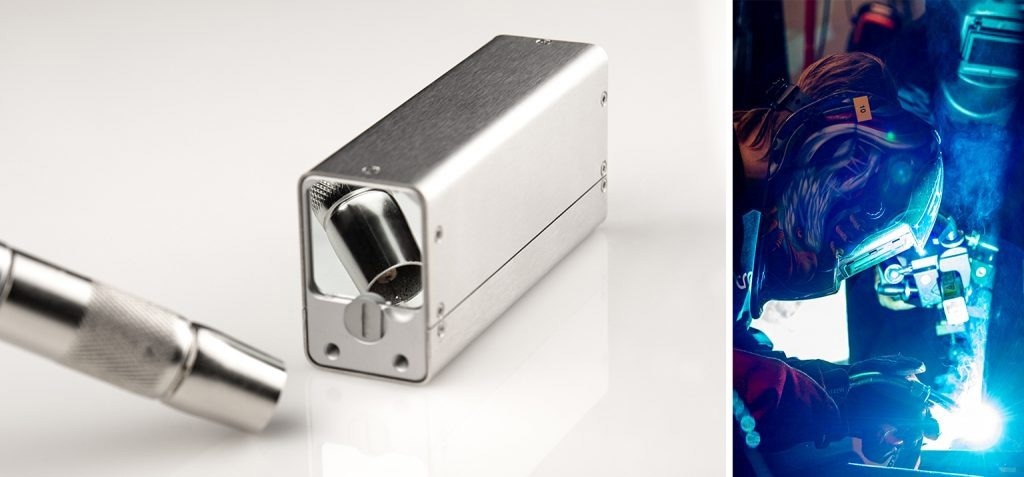
Image Credit: Cavitar
Usually, the welding process is evaluated via a series of post-weld inspections, e.g., visually by an experienced weld inspector, NDT test measurements, topography sensors, or even quality testing by destroying a selection of completed welds. However, possible welding defects will have already happened before they are fully detected and will result in time-consuming, costly, if not impossible, repairs.
Cavitar has designed a welding camera for capturing high-quality images of welding processes. The Cavitar Welding Camera is compact and powerful and has been constructed with the ability to endure harsh industrial environments.
It was designed and developed to address the needs in industry and in welders’ education in order to offer a comprehensive view of the welding process and, at the same time, enhance welder safety. This article lists various areas where Cavitar Welding Cameras can benefit operations.
Better Process Monitoring and Understanding Through Clear Images
Using a welding camera for monitoring and visual inspection during the welding allows any problems and defects to be identified early on. The camera is typically used to see if the welding torch is aligned with the gap correctly. The camera also allows the process operator to place the filler materials more accurately to the weld.
Additionally, users are able to observe the melt pool characteristics, which can signal defects like inclusions. Once a problem is detected, the process can be instantly realigned remotely. This means less scrap and greater yields because a flaw was detected early in the process, minimizing downtime or lost production time due to repairs.
Furthermore, by evaluating and recording the welds and welding parameters, the same high-quality process can be produced repeatedly, thus delivering high batch-to-batch consistency.
Clear View to T-Joint MIG Welding taken with Cavitar Welding Camera
Video 1. MIG welding of a T-joint. Video Credit: Cavitar
Using the welding camera to record the welding process facilitates non-destructive post-weld analysis, enabling quality checking. In case of customer claims, recordings can be supplied as proof that the welding has been of high quality.
Offering a clear view of processes also enables the close study of how various parameters, such as welding speed and angles, as well as materials like filler materials and protection gases, influence the welding process of various welded materials.
Typically, this is used by research and development to find best practices and improve the process. However, it can also help on-site process engineers to better understand their processes.
In automated welding applications, it is a significant advantage to be able to verify that the torch stays at the programmed path prior to welding. This allows adjustments of the program to be made before the actual weld and allows for quick startup of the real process, as well as limiting defects due to inaccuracies in the program.
Due to the capability to see through heat and the blinding welding process light, Cavitar Welding Cameras deliver the same image quality irrespective of whether the welding process is on or off, thus offering a deeper understanding of the process.
Improving Working Conditions for Welders
Welding cameras allow rapid and easy remote alignment of weld torch and gap. A task that is conventionally done manually through a welding helmet and often performed in difficult-to-access places close to the welding process and with exposure to heat and toxic fumes.
Welding cameras also improve work safety due to their capability to monitor the process. Compact welding cameras can be seamlessly incorporated into the welding process to supply a clear real-time view of the process while facilitating safe, remote monitoring and adjustment of the process.
The use of a welding camera significantly enhances ergonomics as the operator can manage and view the welding process without having to take up uncomfortable working positions. This makes for happier and healthier employees whilst offering welders the chance to have a longer working life.
Here you can read how SERIMAX uses Cavitar welding cameras in their complex orbital welding application.
Cavitar's Welding Camera Solution Used by Serimax
Video 2. Cavitar Welding Camera for orbital GMAW welding at Serimax. Video Credit: Cavitar
Teaching the Future Welders with the Help of Welding Cameras
Root and Face View of a MIG Welding with Cavitar Welding Camera
Video 3. Top and bottom view of the same GMAW welding process. Video Credit: Cavitar
The capability to see through the bright light of the welding process also offers benefits in welding education. Cavitar Welding Cameras deliver a clear view of the details of the process – to the melt pool, weld arc, weld seam, and torch tip. Therefore, the welding instructor can demonstrate the welding process's features to all students with ease and clarity.
Welding defects, such as inclusions, cracks and porosity are also visible, as are the conditions that bring them about. The students are able to watch the welding from a screen/monitor rather than being tightly packed around the instructor.
Demonstrations can also be recorded, which means that students can learn from the lessons in their own time by watching the recordings. By recording lessons, the instructors preserve a permanent record of material, preventing the need to constantly recreate lessons.
Also, the students can record practice welds which makes it possible for the students to monitor their own individual personal learning progress.
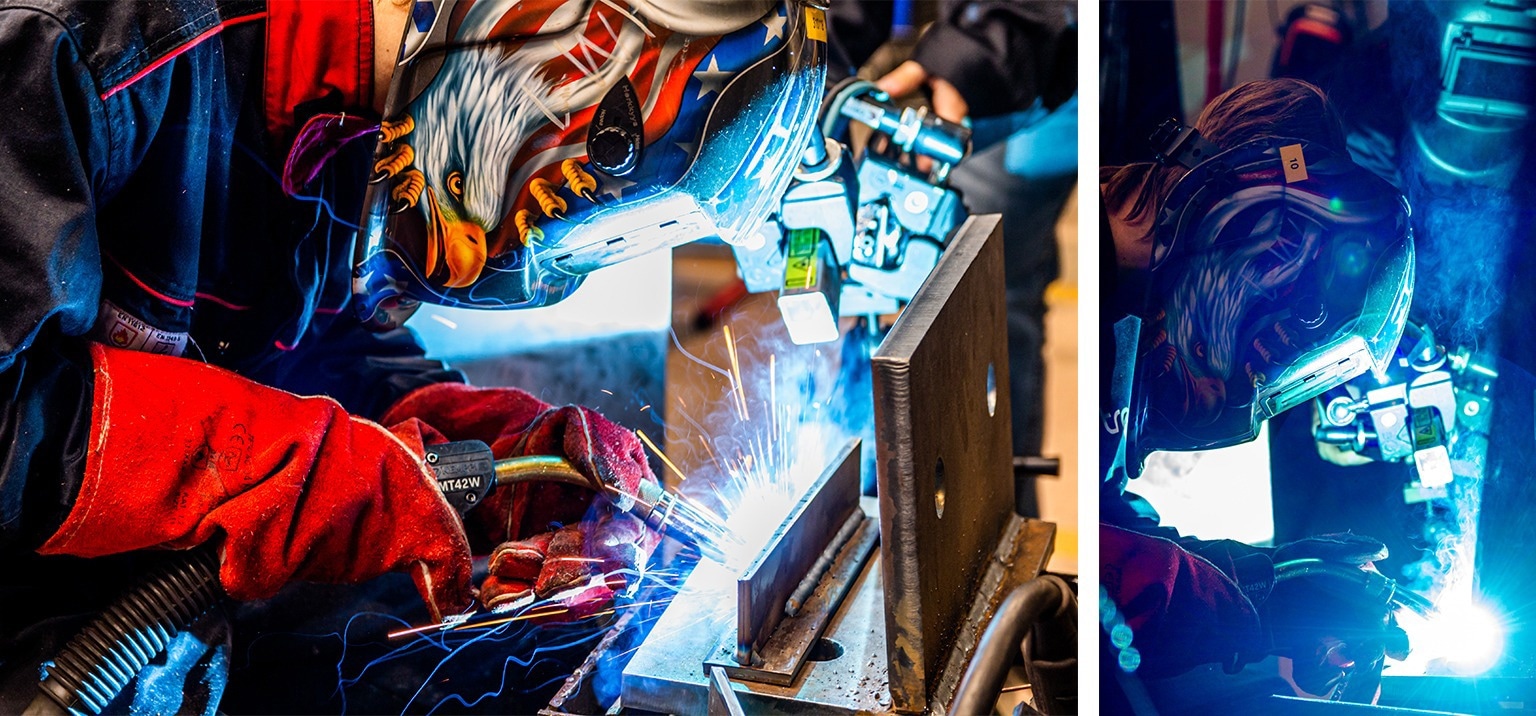
Image Credit: Cavitar
The example applications outlined above demonstrate that welding cameras are an exceptional and powerful tool for companies in the welding industry. With Cavitar Welding Camera solutions, manufacturers and educators are offered a high-resolution view and understanding of their key processes. Contact Cavitar to find out more www.cavitar.com/contact.
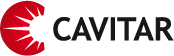
This information has been sourced, reviewed and adapted from materials provided by Cavitar.
For more information on this source, please visit Cavitar.