Mining is no walk in the park. It’s tough, unpredictable, and downright dangerous. But as operations get more complex, technology is stepping in to make things easier—and safer. From mapping and surveying to excavation and transportation, robots are changing the game in mining, boosting efficiency while keeping workers out of harm’s way.
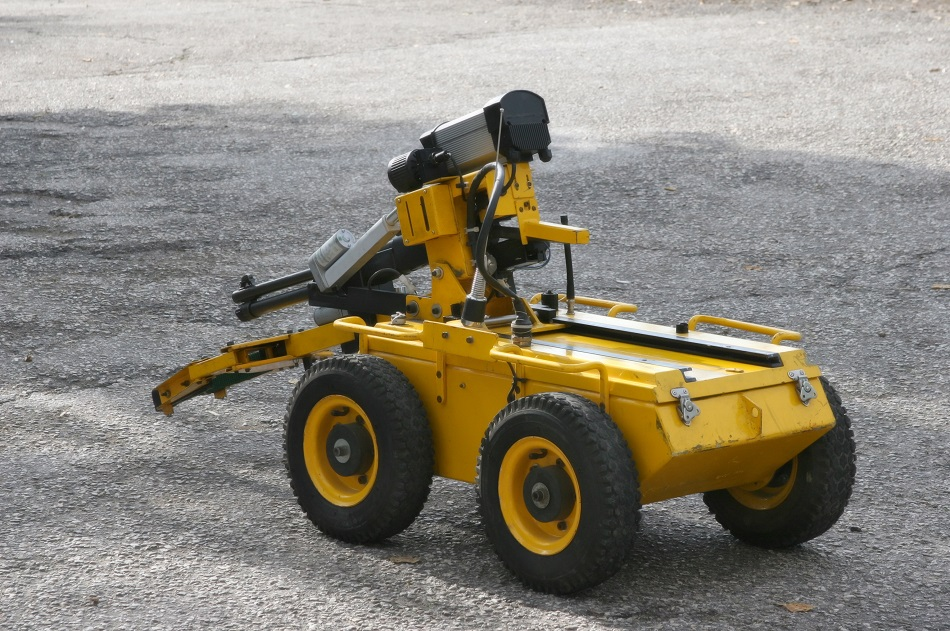
Image Credit: Stavchansky Yakov/Shutterstock.com
Download your PDF copy now!
In this guide, we'll take a closer look at how robots are transforming both surface and underground mining. From self-driving haul trucks to intelligent coal-mining bots, we’ll explore the latest advancements, real-world applications, and what the future holds for automation in mining.
Why Robots Are a Big Deal in Mining
Robots aren’t just a fancy addition to mining—they’re essential, especially in underground operations where safety risks are high. Deep in the mines, certain areas are nearly impossible for humans to monitor and maintain regularly. Recent fatality statistics highlight the dangers miners face, particularly in hard-to-reach locations where inspections can be challenging.1,3
Blasting is another huge risk. Expanding tunnels using explosives can cause cave-ins, structural failures, and dangerous gas leaks. Traditionally, workers inspect the site after each blast to ensure it's safe to continue. But why put people in harm’s way when robots can do the job just as well—if not better?
Beyond safety, robots also help cut costs. They automate routine inspections and reduce downtime, making operations more efficient. Plus, robotic vehicles can explore mines and gather valuable data, aiding in search-and-rescue efforts when necessary.
Robots Taking Over Surface Mining
Opencast mining relies on massive earthmoving machinery and a large workforce, but with that comes increased risks and the need for higher efficiency. That’s where robots come in. By automating machinery, mining operations can improve safety, reduce human exposure to hazardous conditions, and boost overall productivity. Robotic systems are quickly becoming a game-changer in the industry, helping mines run smoother and more efficiently than ever.2-4
In surface mining, haul trucks play a crucial role in moving materials from excavation sites to processing or stacking areas. But with the rise of autonomous mining vehicles, the game is changing. These self-driving haul trucks come equipped with advanced sensors, situational awareness, and precision control systems, allowing them to navigate challenging environments without human intervention. This results in fewer accidents, greater efficiency, and a major boost in productivity. In fact, in Western Australia, autonomous hauling technology has increased output by 20 %—a clear sign that automation is reshaping the future of mining..2-5
However, it is not just haul trucks leading the charge; one of the most exciting advancements is a 3500-tonne, 75-meter-tall semi-automated dragline that has been tested in a Queensland coal pit. This enormous machine can lift an astonishing 120 tonnes of rock in a single scoop and has been automated to reduce operator involvement by 80 %. With an integrated control system managing its 100-meter boom and swinging load, it operates with incredible precision, easing the burden on human operators and improving efficiency.2
And let’s not forget semi-autonomous mine navigation systems. Equipped with visual sensors, these systems help guide mining robots in open-pit and underground settings. They’re especially useful for disaster response, assisting in rescue operations when communication is limited.
Robots Underground: Taking Over the Most Dangerous Jobs
Underground mining presents some of the toughest challenges in the industry—harsh conditions, high costs, and serious safety risks. That’s why autonomous and remote-controlled machines are quickly becoming essential for operations below the surface.2-4
Miners often use remote-controlled equipment to operate machinery from a safe distance, especially in unstable draw sites that could collapse. This technology drastically reduces workers' exposure to hazardous conditions, making mining safer than ever.5
Then there are robotic carts—tiny but mighty machines loaded with lasers and sensors. These robots can map underground tunnels, navigate narrow spaces, and even detect objects. One such cart uses four two-dimensional (2D) laser range finders to gather data about the mine’s ground, cross-section, and ceiling structures.2
Similarly, the Groundhog robot built from the chassis of two all-terrain vehicles features two 2D laser range finders for forward 2D and three-dimensional (3D) mapping of the ceiling. Weighing 1600 pounds, Groundhog was used to successfully map an abandoned coal mine near Burgettstown, Pennsylvania, creating an accurate map of 100 feet, despite the mine being flooded since the 1920s.2
Meanwhile, in South Korea, the Korea Coal Corporation has partnered with three Korean engineering institutions to develop intelligent coal-mining robots. These robots will not only drill in mines but also load and unload coal onto conveyors for transportation. Operators will control the robots remotely using a 3D scanner attached to the back, enhancing efficiency in mining operations.2
Other robots can even come equipped with gyroscope navigation, material detection systems, and gas sensors to keep operations running smoothly. Automated inspections not only minimize risk but also save time by eliminating the need for shift changes.2
Large, international companies are also getting in on the action, with the likes of ABB, a Swiss-Swedish multinational, developing robots designed to inspect mining equipment and infrastructure, such as pipes and tunnels, for damage and wear. These robots reduce human involvement, lower risks to inspectors, and enhance overall safety standards in mining operations.1,2
ABB Robot Charger for remote blasting at the rock face in underground mining
The Next Big Thing: Swarm Robotics in Mining
Mining operations often require multiple machines working together, and that’s where swarm robotics comes in. This emerging technology focuses on small, coordinated robots collaborating to complete tasks efficiently and precisely. A recent study in Applied Sciences tested four different swarm robot models—baseline, ant, firefly, and honeybee—to see how they performed in essential mining operations like ore detection, transportation, and extraction.6
The results were promising. Swarm robots significantly boosted productivity and accuracy, especially in complex mining environments. In Australia’s Pilbara iron ore mine, these models demonstrated their capabilities, each excelling in different ways:
- The ant model was highly effective at role allocation, ensuring tasks were distributed efficiently.
- The honeybee model combined hybrid control with enhanced localization, improving navigation in the mine.
- The firefly model stood out for its advanced communication capabilities, allowing seamless coordination among robots.
Despite its precision, the honeybee model faced challenges with reliability in high-error conditions and encountered computational slowdowns in large-scale operations. Even so, this study highlights the potential of swarm robotics to make mining operations smarter, more adaptive, and far more efficient.
What’s Next for Mining Robotics?
Robotic technology is already an integral part of modern mining. From autonomous haul trucks in open-pit mines to robotic drillers operating deep underground, these machines are changing the game when it comes to how minerals are extracted.
Automation isn’t just about efficiency; it’s also reducing the risks associated with hazardous environments, making mining safer for workers while increasing overall productivity. The adoption of robotics has already proven its value in reducing workplace hazards and optimizing productivity, but widespread implementation isn’t without its challenges.
The biggest hurdle is cost. Advanced robotic systems require significant upfront investment, and mining companies must weigh these expenses against long-term gains in efficiency and safety. Additionally, integrating robotics into mining operations requires skilled personnel who can manage, maintain, and optimize these technologies.
Despite these challenges, the trajectory is clear: mining robots are here to stay. As automation continues to advance, we can expect even smarter, more adaptable machines that will further reduce operational risks, minimize environmental impact, and push the boundaries of what’s possible in modern mining.
Download your PDF copy now!
Want to Learn More?
If this topic has caught your interest, why not check out some of the below articles that cover like-minded topics?
References and Further Reading
- Horner, H. (2023). Robotics in Mining: Benefits, Challenges, and the Role of Engineers [Online] Available at https://www.eit.edu.au/robotics-in-mining-benefits-challenges-engineers/ (Accessed on 12 March 2025)
- Basha, P.C., Patel, V.K. (2022) Applications of Robotics in Mining Industry. Thematics Journal of Applied Sciences. https://thematicsjournals.org/index.php/tjas/article/view/20323
- Nordström, S. et al. (2024). Safety Inspections and Gas Monitoring in Hazardous Mining Areas Shortly After Blasting Using Autonomous UAVs. Journal of Field Robotics. DOI: 10.1002/rob.22500, https://onlinelibrary.wiley.com/doi/full/10.1002/rob.22500
- Ali, D., Iqbal, S., & Ahmad, N. (2024). A Review on The Role of Robotics in Improving Mine Safety and Efficiency. Exceed Journal of Biological and Computer Sciences, 1(1). https://www.exceedpublications.com/index.php/ejbcs/article/view/3
- John, A., Krishna, A., Ali, M., Suku, A., Kumar, A. S. (2021) Application Of Robotics In Mining- A Review. International Journal of Creative Research Thoughts. https://ijcrt.org/papers/IJCRT2108016.pdf
- Tan, J., Melkoumian, N., Harvey, D., Akmeliawati, R. (2024). Evaluating Swarm Robotics for Mining Environments: Insights into Model Performance and Application. Applied Sciences, 14(19), 8876. DOI: 10.3390/app14198876, https://www.mdpi.com/2076-3417/14/19/8876
Disclaimer: The views expressed here are those of the author expressed in their private capacity and do not necessarily represent the views of AZoM.com Limited T/A AZoNetwork the owner and operator of this website. This disclaimer forms part of the Terms and conditions of use of this website.