Robotic systems are becoming more collaborative and more dynamic. Whether in industrial, healthcare, or domestic settings, they increasingly work alongside humans and move around freely in shared spaces. Functional safety standards help manufacturers design robots and other mechanical systems with built-in, automatic “fail safe” measures.
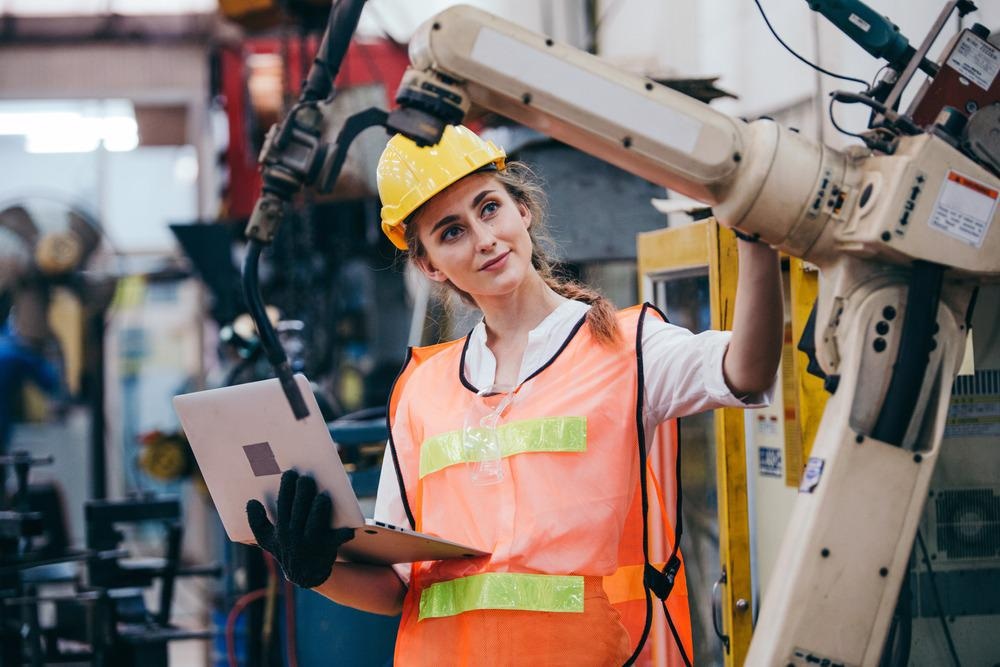
Image Credit: winnievinzence/Shutterstock.com
What is Functional Safety?
Functional safety refers to “fail safe” safety elements of a system or machine that automatically protect the system, its operator, or its surrounding environment from harm.
Fail safes or safety functions need to be designed into any potentially hazardous system, be that a robot, an electric grid, or a single piece of machinery. Functional safety needs to account for any potential issues that could be caused by human error, systematic errors, hardware failure, operational stress, the surrounding environment, and any other factors.
Functional safety systems include all of the safety functions necessary to remove unacceptable levels of risk of equipment damage, personal injury, damage to individuals’ health, property damage, and environmental damage.
No safety process will work unless it is designed with attention paid to the whole system and environment that it is a part of. This means that the scope of functional safety projects is necessarily end to end: it takes all aspects of a system into account.
For example, software is used extensively in many systems to automatically command and control processes, including safety functions. The general operative performance of the software is therefore critical to the overall functional safety of the system.
Functional Safety Standards Regulate a Global Industry
The basic concepts of functional safety – that machinery and systems should pose no threat to themselves, people, property, and their surrounding environment – are built into the safety functions that are implemented into large machine systems.
These concepts are based on sets of agreed upon standards. The International Organization for Standardization (ISO) defines functional safety as “an absence of unreasonable risk caused by malfunctioning electrical and/or electronic (E/E) systems” in ISO 26262.
Manufacturers and users of components, subsystems, and systems that make claims about their functional safety need to have those claims certified by a functional safety standard that is widely recognized.
Functional safety standards certify products to certain Safety Integrity Levels (SILs), or in some niche applications, to certain Performance Levels (PLs). Manufacturers receive the certificate with an assessment report that explains the scope and limits of their product’s functional safety performance.
Due to the end to end nature of the scope of functional safety processes, functional safety standards for electrical, electronic, and programmable systems (like robots) are required to extend to parts of the system that are not electrical, electronic, or programmable. These components include actuators, valves, motor controls, monitors, and even the software that enables automation.
Functional Safety for Robotics
Robot developers are increasingly designing robots to work more closely alongside humans. As a result, functional safety is increasingly important in robot system design.
The broad trend in robotics and industrial automation over the last century has been from coexistence. Here, robots are kept safely away from humans with minimal freedom of movement; to cooperation, where robots and humans share a workspace but carry out separate, potentially nonsynchronous tasks; and on to collaboration, where robots and humans work together in the same space and at the same time.
As a result of this trend, robots increasingly come into close proximity with humans, and so applying functional safety standards is paramount for newly designed robotic systems.
Functional Safety Standards for Robots
Several international and national governing bodies set functional safety standards, with input from professionals, industry and government representatives, and consumer groups.
Professionals working in the safety standards sector tend to adopt a hazard-based safety engineering methodology. This enables a systematic approach to safety that leads practitioners to identify all hazards and put mitigating measures in place to reduce the amount of energy that the machine can transfer to humans.
The international functional safety standards are set by the International Electrotechnical Commission (IEC), as well as the ISO. Many countries also have their own governing bodies setting functional safety standards.
The well known national governing bodies include the American National Standards Institute (ANSI) in the United States, the BSI (British Standards Institution) Group in the United Kingdom, and the CSA (formerly Canadian Standards Association) Group in Canada.
Robot developers work according to three main safety standards:
The ISO 26262 automotive electronic system safety standard mentioned above applies to all electrical, electronic, and programmable systems, including robots. The IEC 61508 standard is also for electrical systems and products. It certifies products according to certain SILs and PILs depending on their functional safety performance.
The ISO 13849 machinery control systems safety standard is for functional safety systems, safety related parts, and software that drives it. As well as robotics, it applies to various electrical, mechanical, hydraulic, and other technologies.
References and Further Reading
Antony, J. (2020). Hazard-Based Safety Engineering. [Online] UL. Available at: https://www.ul.com/news/hazard-based-safety-engineering
Functional Safety (FuSa) for Robotics Overview. [Online] Intel. Available at: https://www.intel.com/content/www/us/en/robotics/robotics-functional-safety-fusa.html
Disclaimer: The views expressed here are those of the author expressed in their private capacity and do not necessarily represent the views of AZoM.com Limited T/A AZoNetwork the owner and operator of this website. This disclaimer forms part of the Terms and conditions of use of this website.