By Samudrapom DamReviewed by Susha Cheriyedath, M.Sc.Updated on Oct 10 2024
Robotic control systems are at the core of modern robotics, enabling machines to perceive their environment, process information, and perform tasks. These systems incorporate logic analysis, data algorithms, and various processing methods to ensure precise and efficient movement. Control systems typically operate in three stages: perception, where data is collected from sensors; processing, where the information is analyzed; and reaction, where the necessary commands are sent to the actuators to execute the required actions.1
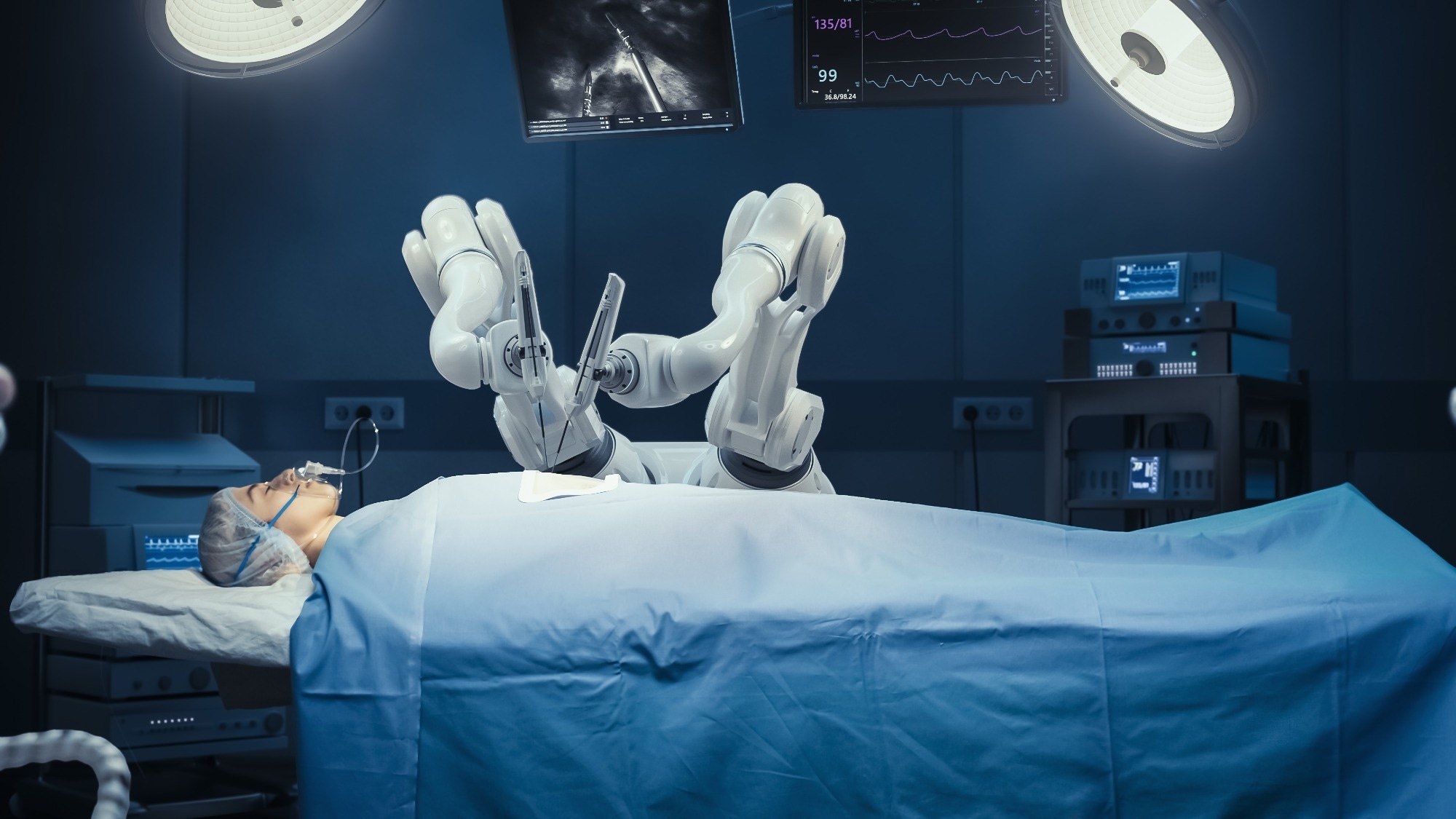
Image Credit: Gorodenkoff/Shutterstock.com
Key Control Methods in Robotics
Control systems in robotics use different methods to optimize performance based on the task's complexity and environmental conditions. Let’s explore the primary methods:
- Adaptive Control: This method continuously modifies the system's behavior based on prior actions and feedback, adapting to long-term changes in the environment. For instance, in manufacturing robots, adaptive control can help correct errors caused by gradual wear and tear of machinery. However, it is less effective in responding to sudden changes, such as unexpected obstacles.1
- Open-Loop Control: Open-loop control works without feedback, meaning the system operates based solely on preset parameters. This approach is common in simple applications, like automated conveyor belts or washing machines, where the tasks are repetitive and the environment is stable. However, without feedback, any variation in conditions can lead to inaccuracies.
- Closed-Loop Control: Closed-loop systems, also known as feedback control, are essential for tasks requiring high precision. By continuously comparing the robot’s output with the desired outcome, closed-loop control adjusts performance in real-time, correcting errors. For example, in autonomous vehicles, sensors monitor speed, direction, and external conditions, allowing the system to make immediate adjustments for safety and efficiency.
- Feed-Forward Control: Unlike closed-loop control, feed-forward systems anticipate changes and adjust the control action without waiting for feedback. This method is particularly useful in high-speed systems where delays in feedback could hinder performance, such as in high-speed assembly lines or laser-cutting machines.
- Feedback Control: Feedback control is vital for maintaining accuracy in complex robotic systems. By constantly measuring sensor data, the system can adjust actuator movements to correct errors in speed, position, and orientation. This control method ensures robots meet their performance targets, making it essential for precision tasks such as robotic surgery or drone navigation.
Components of Robotic Control Systems
For robots to function effectively, three critical components must work together: sensors, controllers, and actuators. These elements form the foundation of any robotic control system.
Sensors: Perceiving the Environment
Sensors are the eyes and ears of a robot, gathering data from the environment and translating it into actionable information. Various sensors are used for different tasks:
- Cameras help robots visually map their surroundings, crucial for tasks like object recognition and spatial awareness.
- Microphones enable sound detection, allowing robots to respond to auditory cues in their environment.
- Bumper sensors detect physical collisions, useful for mobile robots navigating tight spaces.
- Advanced sensors, such as LIDAR (Light Detection and Ranging) and supersonic sensors, create detailed 3D maps of the robot's environment. LIDAR uses laser beams, often in autonomous vehicles, while supersonic sensors use high-frequency sound waves to map spaces more cost-effectively.
Controllers: The Robot’s Brain
Controllers process sensor data and make decisions, guiding the robot's actions. In simpler robots, microcontrollers handle basic tasks such as motor control or navigation. For more advanced robots that need to process large volumes of data—like those using AI for image recognition—high-performance controllers are required. The controller acts as the robot's brain, managing everything from simple routines to complex decision-making processes.
Actuators: Bringing Movement to Life
Actuators convert energy into motion, enabling robots to perform physical actions like moving limbs or gripping objects. Whether driving wheels, manipulating robotic arms, or controlling servo motors, actuators are responsible for translating commands into physical movements. Actuators can be linked to computer systems through interfaces like USB or digital control systems, allowing for flexible and precise control.
Exploring the Different Types of Control Systems
Control systems can be classified based on their characteristics and applications. Below are the main types of control systems, each with its unique benefits and challenges.
- Open-Loop Control Systems: Best suited for predictable tasks, open-loop systems are used in devices where conditions are stable, such as in household appliances or basic robotic arms. These systems are efficient for repetitive tasks but lack the adaptability needed for more dynamic environments.
- Closed-Loop Control Systems (Feedback Control): Closed-loop systems excel in environments requiring constant adjustments. These systems are widely used in HVAC systems, autonomous vehicles, and robotic surgery, where precision and adaptability are essential for success.
- Linear Control Systems: Linear systems are characterized by a direct relationship between input and output. They are simple to model and commonly found in applications like electric motors or conveyor belts, where system dynamics are predictable and stable.
- Non-Linear Control Systems: These systems deal with complex behaviors where the relationship between input and output isn’t proportional. Non-linear control is often applied in more advanced systems, such as drones or robotic arms, where changing forces and unpredictable conditions demand flexibility.
- Time-Variant Control Systems: These systems are designed for dynamic environments where conditions evolve over time. Applications include satellite navigation and mobile robots navigating unfamiliar terrain, where the system must continuously adapt to changing variables.
- Time-Invariant Control Systems: In contrast, time-invariant systems operate in stable environments where conditions remain consistent, such as elevators or factory conveyor systems.
- Continuous-Time Control Systems: Continuous-time systems operate in real-time, providing uninterrupted control in systems like motor speed regulation or fluid dynamics. These are essential for tasks requiring constant monitoring and adjustment.
- Discrete-Time Control Systems: Discrete-time systems operate at specific intervals, often in digital systems like robotic controllers or automated manufacturing lines. These systems process signals at set times, making them ideal for tasks involving regular data sampling.
- Feedforward Control Systems: Feedforward control anticipates disturbances before they occur, adjusting system parameters proactively. This method is commonly used in high-speed industrial processes, where quick response times are critical.
- Digital Control Systems: Digital control systems are increasingly prevalent in modern robotics, from 3D printers to CNC machines, where precise and fast computation is necessary.
In practice, many robotics applications combine multiple control strategies to optimize performance, depending on the specific requirements of the system. For instance, a robot may use closed-loop feedback control for precise movements but employ feedforward control for rapid adjustments in specific scenarios.
Impact of Artificial Intelligence
The integration of Artificial Intelligence (AI) has brought revolutionary changes to robotic control systems. AI enables robots to become more adaptive, intelligent, and capable of handling increasingly complex tasks. With AI, robots can now perform advanced functions such as obstacle avoidance, precision navigation, and autonomous decision-making in dynamic environments.
For example, a recent study presented at the 2023 2nd International Conference on Artificial Intelligence and Autonomous Robot Systems (AIARS) showcased a bionic robot capable of transporting goods using AI-driven navigation and obstacle avoidance algorithms. The simulation demonstrated that the AI algorithm allowed the robot to optimize its path, smooth its trajectory, and improve convergence speed—all crucial elements for efficient autonomous operation.
This growing trend in AI-driven robotics has also influenced major players in the robotic control system market, such as Hanbay Inc., Omron Automation, Tolomatic Inc., and Taricco Corporation. These companies are developing cutting-edge solutions, including electric valve actuators, sensors, and motion controllers, to support AI-enhanced robotics. Their innovations help optimize control systems, allowing robots to perform more efficiently and reliably in complex industrial and commercial settings.
Conclusion: The Future of Robotics and Control Systems
Control systems are the core of robotics, empowering machines to perceive their surroundings, process information, and perform tasks with accuracy and precision. These systems range from simple open-loop configurations to sophisticated AI-driven solutions, ensuring robots can operate both efficiently and adaptively. As technology continues to evolve, we can expect further groundbreaking innovations in automation, driven by advancements in control systems and the pioneering efforts of industry leaders.
What to Expect from the Robotics Industry by 2030
References and Further Reading
- Brogårdh, T. (2009). Robot Control Overview: An Industrial Perspective. Modeling, Identification and Control: A Norwegian Research Bulletin, 30(3), 167–180. https://doi.org/10.4173/mic.2009.3.7
- Mustafa, M. M., Hamarash, I. (2019). Microcontroller-based motion control for DC motor driven robot link. 2019 International Aegean Conference on Electrical Machines and Power Electronics (ACEMP) & 2019 International Conference on Optimization of Electrical and Electronic Equipment (OPTIM), 547-552). DOI: 10.1109/ACEMP-OPTIM44294.2019.9007122, https://ieeexplore.ieee.org/abstract/document/9007122
- Wang, J., Chortos, A. (2022). Control Strategies for Soft Robot Systems. Advanced Intelligent Systems, 4(5), 2100165. DOI: 10.1002/aisy.202100165, https://onlinelibrary.wiley.com/doi/full/10.1002/aisy.202100165
- Erbay, O., Doğan, A., Devecioğlu, E. (2024). Line Follower Robot with PID Control. https://www.researchgate.net/publication/377666058_Line_Follower_Robot_with_PID_Control
- Thwin, L. M. M., Chan, Y. (2020). Application of LQR control for two-wheel self-balancing robot. Journal of Myanmar Academy of Arts and Science, 28(2), 263-272. https://www.researchgate.net/publication/348277702_APPLICATION_OF_LQR_CONTROL_FOR_TWO-WHEEL_SELF-BALANCING_ROBOT
- Gottlieb, J., Anderson, D.L. Parts of a Robot [Online] Available at https://mind.ilstu.edu/curriculum/medical_robotics/parts_of_robots.html (Accessed on 07 October 2024)
- Central Control: Robot Brains [Online] Available at https://www.cs.rochester.edu/users/faculty/nelson/courses/csc_robocon/robot_manual/central_control.html (Accessed on 07 October 2024)
- Robot Acutators [Online] Available at https://www.cs.rochester.edu/u/nelson/courses/csc_robocon/robot_manual/actuators.html (Accessed on 07 October 2024)
- Lin, Z., Xu, F. (2023,). Simulation of robot automatic control model based on artificial intelligence algorithm. 2023 2nd International Conference on Artificial Intelligence and Autonomous Robot Systems (AIARS), 535-539). DOI: 10.1109/AIARS59518.2023.00113, https://ieeexplore.ieee.org/abstract/document/10285212
Disclaimer: The views expressed here are those of the author expressed in their private capacity and do not necessarily represent the views of AZoM.com Limited T/A AZoNetwork the owner and operator of this website. This disclaimer forms part of the Terms and conditions of use of this website.