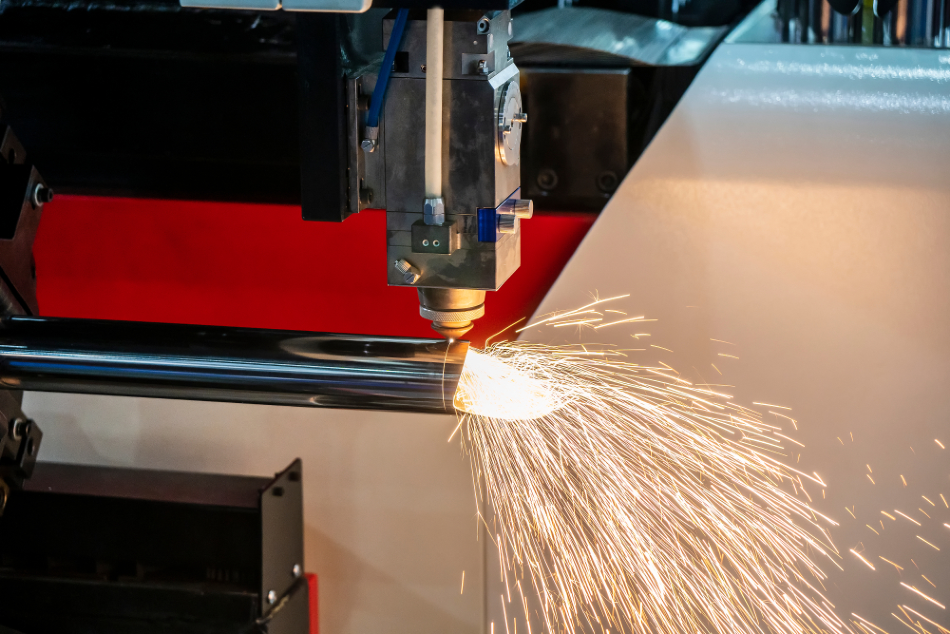
Image Credit: Pixel B/Shutterstock.com
The Benefits of Robotic Fiber Laser Welding Systems
Robotic fiber laser welding has become well established in numerous industries, notably within the automotive industry, manufacturing sector, and the oil, gas, and mining industries. Advancements in technology have made robotic laser welding even more beneficial to those who opt to incorporate it into their processes. Generally, it is known for cutting costs, increasing productivity, increasing production speed, reducing errors on first runs, and bringing more flexibility and productivity to the workspace.
Robotic fiber laser welding systems also allow engineers to work with a wider range of materials, such as those that have not previously been weldable with traditional welding techniques, such as metals that are prone to cracking, and exotic metals. This is enabling industries to work with a wider range of materials and create products that had not been achievable previously.
The number of advantages systems of robotic fiber welding lasers hold over traditional welding systems has helped the robotic systems become established in numerous applications, which we discuss below.
Applications
Remote laser welding
Remote laser welding is a rapidly growing application of robotic fiber laser welding because of its increased use by manufacturers of lithium battery modules for e-mobility. To make these batteries the welding of individual battery cells is essential. 2D and 3D scanners can be used to carry out remote laser welding, an example of this technique being used at a large scale is BMW’s use of the method to weld their i8 battery modules.
Automotive manufacturing has relied heavily on the use of laser welding for many decades, it is in fact where robotics first became established within manufacturing. The application has proven itself to be precise, and trustworthy, and will continue to play a vital role in automotive manufacturing into the future.
Robotic laser cladding
Like remote laser welding, robotic laser cladding is another robotic welding system that has become firmly established within the field of automotive manufacturing. This system has been successfully used in applications in the automotive industry, such as for preparing the valve sheet of an engine component. The system is like thermal spraying, as it uses powdered metal, which is added to the substrate of the metal to be welded, having the result of protecting or enhancing its properties. The method is beneficial in the automotive industry where large production runs are standard.
Robotic laser cladding is also being used to weld and repair the worn wheel spindles of large mining trucks, as well as to weld the components of land-based gas turbines, making the method essential to the mining and oil industries.
Spin scanning welding
Spin scanning welding is a friction welding method that is used to weld thermoplastics. It has numerous applications across a variety of industries. First, this method is firmly established in applications that create packaging. Bottles that dispense liquids, bottle tops, canisters, and lids all can be created with spin scanning welding. At the other end of the scale, the technique can be used to weld together components of large household appliances such as washers and vacuums. Also, spin scanning welding is being used to help create electronic products, being useful in creating hermetically sealed welds for plastic components within electronic products. Finally, the method is used in the automotive industry to weld circular components, such as the engine and other under the hood parts.
Potential future applications
In the future, it is predicted that robotic fiber laser welding methods will advance to facilitate the welding of dissimilar materials. The requirements of the automotive industry will likely drive this, with its growing need for lightweight designs and with new materials being used to replace conventional ones.
References and Further Reading
Disclaimer: The views expressed here are those of the author expressed in their private capacity and do not necessarily represent the views of AZoM.com Limited T/A AZoNetwork the owner and operator of this website. This disclaimer forms part of the Terms and conditions of use of this website.