Jul 17 2012
Climbing is a crucial survival trait among animals to aid feeding behaviour and survival. Research into robotics is trying to advance this basic principle of climbing behaviour into the robot world by engineering a system that can move up vertically complex man-made structures, structural frames and natural structures including trees to help carry out tasks that could become too dangerous for humans if the target is too high.
Motivation
Development of tree-climbing robots has been inspired by the process of natural selection and observing how arboreal animals have evolved and adapted diverse skills to deal with the pressures of a world becoming more complex to survive in. Tree-climbing methods have been designed to help create algorithms that can be implemented into a robotic system to control movement of a robot up a vertical wall. One advantage to engineering a climbing robot is that it removes the need for manipulation of this system by the user. There are a number of factors to consider when designing a climbing robot, such as:
- Studying the different methodologies for climbing behaviour in robots and animals.
- The development of manoeuvre mechanisms for tree-climbing robots.
- The integration of sensors in the robotic foot to aid climbing behaviour.
- Development of adaptability behaviour such as tree-surface fastening mechanisms to allow for climbing robots to maintain grip when in contact with surfaces of varying shape and texture.
- The design and development of novel tree-climbing robots built with varying task performance and learning behaviour.
The locomotive functional mechanism to wall-climbing robots is based on legged, sliding and tracked wheeled manoeuvres. For the scope of this article, focus will be given to the design and development of legged wall-climbing robots.
Legged Wall-climbing Mechanism
Meet RiSE, a robot developed by Boston Dynamics, designed to climb vertical walls (see video below).
Boston Dynamics RiSE V2 and V3
Boston Dynamics have designed RiSE with micro-claws that uses foot contact sensors to sense and adapt to different textures to a surface. This climbing robot can manipulate its structure when in contact with different curvatures to a vertical surface. RiSE has also been designed with a tail like structure to help the robot maintain a state of balance when climbing vertical surfaces with varying curvatures. This is a clear example of how Boston Dynamics have studied how a flexible appendage helps the climbing behaviour of vertebrates and invertebrates, which stresses the fundamental purpose to studying methodology of climbing behaviour in a natural system before evolving this need into artificial systems designed to imitate life-like behaviour.
The robot is approximately 0.25 meters long and weighs 2 kg and can travel at a speed of 0.3 m/s. Weight and length of a climbing robot will impact the speed at which a machine can climb a vertical surface and this needs to be taken into account when designing such artificial systems. RiSE also has six legs controlled by electrical motors, a control system to manipulate the position of each leg and an array of sensors to gather data on joint position and leg strain.
One particular mechanical design for joint movement involves the use of a hydraulic jack to power each leg to a climbing robot. There are also rotational and prismatic joints designed into the robotic leg to control the speed of movement and manoeuvre and with the application of a transducer, the position of each leg can be measured. Figure 1, illustrates a functional pathway to controlling the movement of a joint.
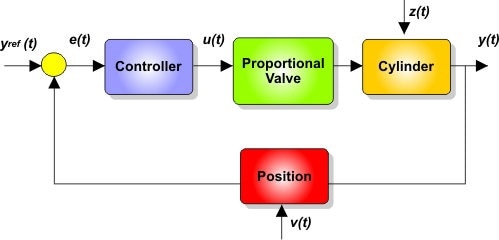
Figure 1. Controlling joint movement in the development of a climbing robot. Source: Armada, M., Gonzalez de Santos, P. Climbing and Walking Robots: Proceedings of the 7th International Conference. (2005). Germany, Berlin: Springer Science.
This position feedback system involves a proportional valve that helps the electrical flow of fluid from a controller to an actuator, which for the leg structure is called a cylinder. The hydraulic cylinder manipulates force in two directions to continue the manoeuvre of the automated system or to shut down the control. The cylinder controlling hydraulic force is connected to a hydraulic pump to generate this power supply. The control system in this feedback loop works as a central processing unit to drive forward a pulse width modulation signal to control the movement of the cylinder. To simulate each leg movement, the central processing unit must measure the timing and positioning of the leg before triggering a joint movement.
On a more basic level, when looking at the main mechanical parts to a climbing robot, a vacuum pressure generator is crucial to a climbing motion and is made of a motor and impeller, along with an embedded control unit. There is a DC-motor that controls the belt to a wheel which transfers motion to the impeller. This driving system is important to controlling the rotational speed of the impeller to allow for higher vacuum pressure to be generated.
The vacuum system is also important for allowing the robot to keep a firm grip of the wall. A sealing device will help separate the inner chamber to the robot from the surrounding environment and secure a grip to the wall. The sealing structure encapsulates the body of the robot, the springs to enhance movement of legs, and a tube. It is the textile on the surface of the tube that allows for a friction coefficient force pressing two bodies together.
RiSE V3 sees six legs reduced to four, resulting in a dramatically different leg mechanism and a unique gaited behaviour. This latest version can climb rapidly – up to 22 cm/s – a vertical structure such as a telephone pole. Future work will study how the robot can move horizontally and how it climbs a wide variety of surfaces.
Although significant progress has been made towards developing wall-climbing robot there are not many working examples of large-scale climbing robots applied in industry; there are still many challenges to overcome before they are seen in real-world settings. Future research may need to focus on the design and application of much larger climbing robots that can be applied to tasks that involve carrying heavy objects up and down a vertical surface. Such surfaces are incredibly diverse in terms of the type of buildings and environments these robots are expected to work in: one of the main challenges remaining is to develop a general-purpose robot capable of navigating any type of wall.
Sources and Further Reading
- Lam, T.L., Xu, Y. (2012). Tree Climbing Robot: Design, Kinematics and Motion Planning. Germany, Berlin: Springer Science and Business Media.
- Armada, M., Gonzalez de Santos, P. Climbing and Walking Robots: Proceedings of the 7th International Conference. (2005). Germany, Berlin: Springer Science.
- Erdmann, M. (2005). Algorithmic Foundations of Robotics, VI, Volume 6. Germany, Berlin: Springer Science.
- Tokhi, M.O., Virk, G.S., Hossain, M.A. (2006). Climbing and Walking Robots. Netherlands: Springer Science.
- Marques, L., De Almeida, A. (2008). Advances in Mobile Robotics. London: World Scientific Publishing Co, Ltd.
- Boston Dynamics. RiSE: The Amazing Climbing Robot.
This article was updated on 18th September, 2018.