Electric vehicles (EVs) have become increasingly popular for their environmental benefits and energy efficiency. At the heart of these vehicles lies the battery pack—a component that requires precise engineering and intricate assembly processes to deliver optimal performance. This is where robotics comes in, transforming the way EV batteries are manufactured by boosting speed, accuracy, and scalability.
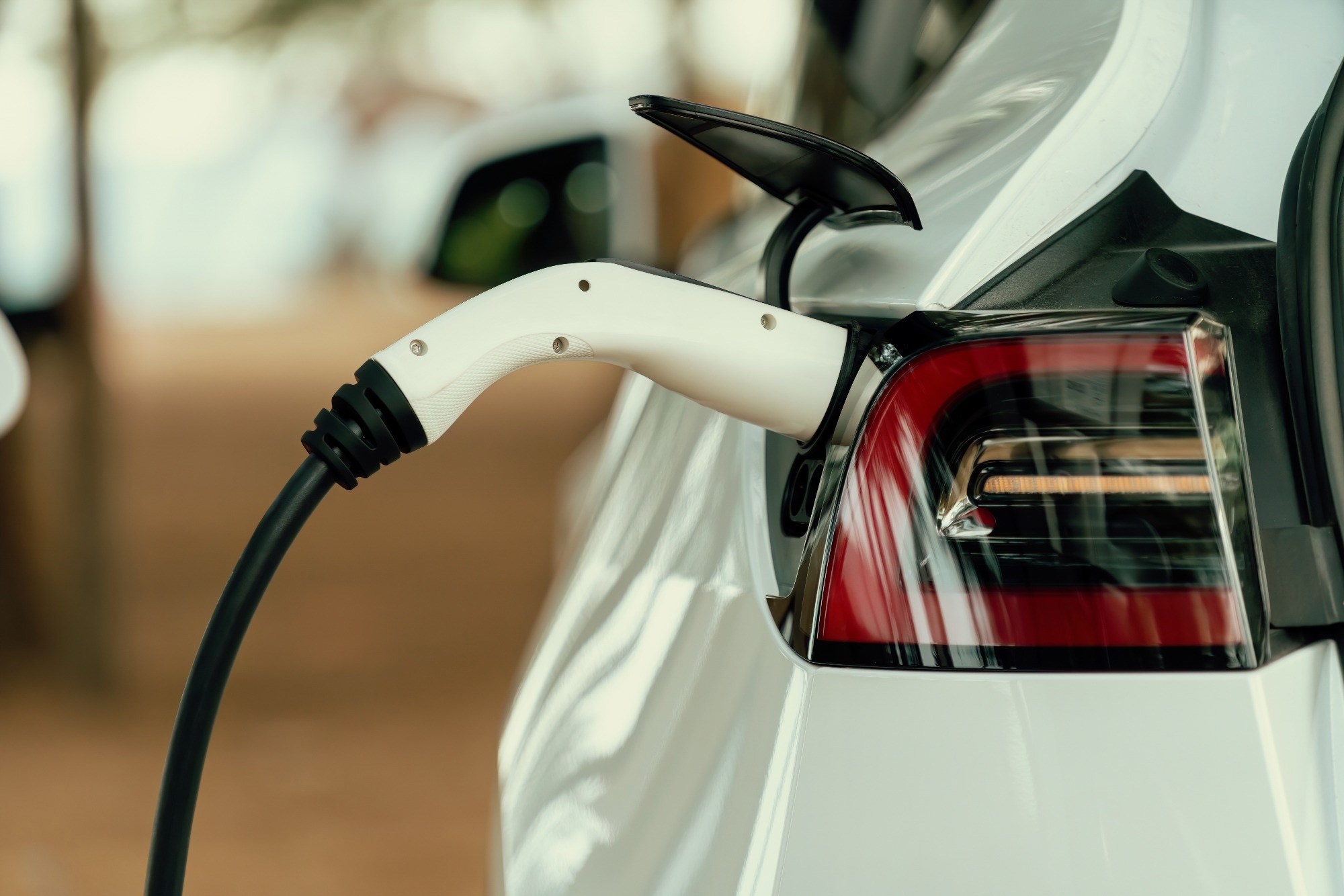
Image Credit: Owlie Productions/Shutterstock.com
By adopting advanced robotic solutions, manufacturers can overcome traditional assembly challenges, driving innovation while keeping costs in check.
This guide will explore the fundamentals of robotics in EV battery production, breaking down the key processes, technologies, and benefits. Along the way, we’ll answer critical questions such as:
- How robotics improves precision and safety in EV battery assembly
- The key benefits and challenges of integrating robotics into production lines
- The future of robotics in sustainable EV manufacturing
Let's begin!
The Role of Robotics in Transforming EV Battery Production
Assembling EV batteries is no small feat—it’s a process that demands precision, consistency, and efficiency at every step. Robotics is revolutionizing this space, bringing speed, quality, and safety to tasks that were once manual and time-consuming. From handling delicate cells to ensuring seamless welding, robots are transforming battery manufacturing into a more reliable and scalable process.
Let’s take a closer look at how robotic technologies are shaping key stages of EV battery assembly.
Cell Handling and Sorting
Automated robotic systems equipped with advanced vision technology can efficiently handle and sort individual battery cells with high precision. These systems employ sophisticated algorithms to categorize cells based on characteristics such as capacity, voltage, and internal resistance. By using robotics, manufacturers can ensure consistent quality and increase production rates, which is crucial for industries such as electric vehicles and consumer electronics.1,2
The integration of artificial intelligence (AI) and machine learning (ML) enables continuous improvement in sorting accuracy. This advanced technology allows for:
- Real-time adaptation to variations in cell characteristics
- Optimization of sorting algorithms based on historical data
- Predictive maintenance of sorting equipment
Laser Welding and Bonding
Precision is critical when joining battery cells into modules, and robotic laser welding delivers exactly that. These systems ensure:
- Minimal heat distortion
- Consistently strong welds
- Superior joint quality
Advanced robotics with adaptive control systems can even tweak welding parameters on the fly to account for differences in materials, ensuring uniform results across high production volumes.1,2
Dispensing Thermal Interface Material
Thermal interface materials (TIM) play a crucial role in dissipating heat between cells and cooling plates. Robots ensure that TIM is applied evenly and precisely, maintaining consistent thickness for optimal heat conduction. This level of precision prevents hotspots, improves thermal management, and ultimately extends the lifespan of the battery.1,2
Battery Module Assembly
Assembling battery modules requires a combination of care and accuracy, and robots deliver on both fronts. Multi-axis robotic arms equipped with torque-controlled tools apply just the right amount of pressure, protecting fragile cells and connectors. Integrated sensors offer real-time feedback, enabling precise adjustments for even greater consistency.1,2
Automated Inspection and Testing
Quality assurance is non-negotiable in battery manufacturing, and robots excel at ensuring high standards. Vision-guided robotic systems can detect tiny defects—like cracks, misaligned cells, or weak welds—with incredible accuracy. Automated testing processes then verify electrical and thermal performance, reducing the likelihood of failures down the road.
Battery Pack Final Assembly
The last stage of battery production involves assembling modules into packs, connecting cooling systems, and conducting final tests. Collaborative robots, or cobots, work alongside human operators to make this process safer and more efficient by:
- Handling heavy components to minimize ergonomic risks
- Ensuring precise placement of modules and connections
- Speeding up production without sacrificing quality
Given that some battery packs can weigh over 1000 kg, heavy-duty pallet conveyor systems often play a supporting role, ensuring stability and precision during this critical phase.
By integrating robotics into EV battery assembly, manufacturers are not just keeping pace with demand—they’re setting new benchmarks for quality and efficiency.
How Robotics is Transforming EV Battery Production
The use of robotics in EV battery manufacturing has introduced practical solutions for improving efficiency, safety, and scalability. Let’s explore how robotics supports key areas in the production process:1-3
- High-Throughput Cell Assembly Lines: Robotic systems enable manufacturers to establish high-speed assembly lines capable of producing thousands of battery cells per hour. With unmatched precision, these systems ensure uniformity across cells—a critical factor for maintaining the high performance and reliability EV batteries demand.
- Customizable Battery Packs: EV models often require tailored battery solutions, and robotics is making customization faster and more efficient. Programmable robotic systems can quickly adapt to new designs and configurations, minimizing changeover time while enhancing flexibility. This adaptability allows manufacturers to cater to diverse EV models without compromising efficiency.
- Scalable Manufacturing Operations: Scaling production to meet the growing demand for EVs has never been easier. Robotic systems allow manufacturers to expand operations by integrating additional automated cells without disrupting existing workflows. This seamless scalability ensures production can grow in line with market needs.
- Improved Safety in Hazardous Environments: The assembly of EV batteries involves working with hazardous materials and high-voltage components. Robotics significantly enhances worker safety by automating tasks in these environments, reducing the need for human intervention and minimizing risks.
- Enhanced Traceability: By integrating IoT sensors, robotic systems provide real-time data on every step of the assembly process. This continuous monitoring enhances traceability, allowing manufacturers to optimize processes, improve quality control, and ensure compliance with regulatory standards.
Long-Term Benefits of Robotics in EV Manufacturing
The advantages robotics brings to EV battery production go beyond immediate efficiency improvements:2,3
- Consistency and Reliability: Uniform production reduces defects and ensures higher-quality batteries.
- Increased Throughput: Automated systems operate continuously, meeting production targets with fewer delays.
- Cost Efficiency: While robotics requires upfront investment, long-term savings are achieved through reduced labor costs, minimized waste, and optimized workflows.
- Reduced Errors: The precision of robotic systems lowers error rates, cutting down on rework and material waste.
Challenges of Robotics Integration in EV Plants
Robotics brings remarkable advantages to EV battery production, but adopting these advanced systems isn’t without its challenges. Manufacturers face several hurdles that require careful planning and strategic solutions to fully unlock the potential of robotics.
One major challenge is the significant upfront cost. Advanced robotic systems come with a hefty price tag, which includes the equipment itself, facility upgrades, and workforce training. For smaller manufacturers, this financial barrier can be daunting, making it harder to justify the investment—even with the promise of long-term benefits. The good news is that as robotics technology continues to evolve and become more affordable, these costs are expected to decrease, opening the door for wider adoption across the industry.1
Another obstacle is the complexity of integrating robotics into existing production lines. It’s not as simple as plugging in new machines; it often requires substantial engineering expertise and meticulous planning. Compatibility with legacy equipment can be a sticking point, and manufacturers may need to redesign workflows, update software, and even reconfigure factory layouts. This process can temporarily disrupt operations, so it’s crucial to have a well-managed transition plan to minimize downtime and ensure a smooth rollout.
Maintaining robotic systems is another critical consideration. These machines require regular upkeep to perform at their best, and any unexpected malfunctions can throw off production schedules. A strong maintenance strategy is key to avoiding prolonged disruptions. Many companies are turning to predictive maintenance, which uses AI and sensors to identify potential issues before they escalate. Having spare parts on hand and a team of skilled technicians ready to respond quickly can make all the difference in keeping operations running smoothly.
Finally, the shift to robotics demands a skilled workforce. Employees need training in areas like programming, operation, and maintenance to work effectively with these advanced systems. Bridging this skills gap is no small feat. Manufacturers can address this by offering in-house training, collaborating with educational institutions, or hiring automation specialists. Beyond technical skills, it’s also important to focus on change management. Employees must adapt to new ways of working alongside robotics, which requires a culture that embraces continuous learning and technological innovation.
While these challenges are significant, they are not insurmountable. With thoughtful planning and a commitment to upskilling teams, manufacturers can successfully navigate the path to robotics integration, reaping the rewards of increased efficiency and productivity in EV battery production.
The Lifespan of EV Batteries: From Production to Recycling
The journey of an EV battery doesn’t end once it leaves the production line. As the demand for EVs grows, so does the need for sustainable solutions to manage the lifecycle of these batteries. Robotics plays a critical role in not only assembling high-performance batteries but also supporting efficient recycling processes that recover valuable materials and reduce environmental impact.
Supporting Sustainability Through Robotics
Robotic systems are enhancing battery recycling by introducing precision and efficiency into what has traditionally been a labor-intensive and hazardous process. Equipped with advanced vision-guided technology, these systems can accurately identify, sort, and recover high-value materials such as lithium, cobalt, and nickel. This level of precision minimizes material waste, optimizes reuse, and significantly reduces the industry’s reliance on environmentally taxing raw material extraction. The result is a meaningful contribution to the circular economy, particularly within the EV sector, where sustainability is increasingly a priority.
AI-powered robotics further enhances these capabilities by enabling dynamic adaptation to the growing diversity of battery designs. As new chemistries and configurations emerge, these systems continuously refine their processes to improve recovery rates and maximize efficiency. For manufacturers, this not only ensures compliance with increasingly stringent recycling regulations but also helps reduce operational costs and mitigate environmental risks. By automating complex disassembly tasks, robotics also addresses safety concerns, limiting workers' exposure to hazardous materials and improving overall workplace conditions.
Looking at the bigger picture, integrating robotic recycling into the broader EV battery lifecycle is about more than compliance or cost savings—it’s about driving long-term sustainability. By closing the loop on resource use, manufacturers can reduce environmental impact, support responsible innovation, and strengthen their competitive edge. Robotics isn’t just a tool; it’s becoming a cornerstone of forward-thinking strategies in EV manufacturing, aligning economic goals with environmental responsibility.3,4
Future Prospects and Conclusion
The future of robotics in EV battery assembly is incredibly exciting. Technologies like autonomous assembly lines, self-healing robots, and decentralized manufacturing hubs are no longer just ideas—they’re becoming closer to reality every day. As robotics hardware and materials science continues to evolve, we’re looking at systems that are smarter, faster, and more adaptable than ever before.
What makes robotics even more powerful is its ability to work hand-in-hand with digital tools. Take IoT-enabled robots, for example—they can provide live updates on production processes, helping manufacturers spot issues early and fine-tune operations on the go. When this data is combined with advanced analytics and cloud computing, it opens the door to even greater efficiency and smarter decision-making.3
Digital twins could even take it a step further, allowing manufacturers to test and optimize production scenarios in a virtual space before making real-world changes. This means fewer disruptions, faster adjustments, and more flexibility to meet changing market demands—all while keeping production running smoothly.3
At its core, robotics is reshaping how EV batteries are made. From carefully handling delicate cells to assembling complete battery packs, these systems are raising the bar for quality, speed, and reliability. Of course, there are still hurdles to overcome, like high initial costs and the need for specialized training, but innovation is moving us closer to solutions every day.
As EVs become more popular, robotics will play an essential role in meeting demand while supporting sustainable manufacturing. It’s an exciting time for the industry, and robotics is at the heart of making it all possible.
Want to Learn More About the Role of Robotics in EV Battery Production?
Robotics is doing incredible things in EV battery production—making everything faster, safer, and more efficient. But it’s not just about speed and precision; it’s also helping us tackle big challenges like sustainability and scaling up to meet growing demand.
If this has sparked your curiosity, here are a few topics you might find interesting:
References and Further Reading
- Ashourpour, M. (2023). Automation of Operations in Assembly of Battery Modules in Electric Vehicles. IFAC-PapersOnLine, 58(19), 754-759. DOI:10.1016/j.ifacol.2024.09.212. https://www.sciencedirect.com/science/article/pii/S2405896324016355
- Sharma, A. et al. (2019). Enabling the Electric Future of Mobility: Robotic Automation for Electric Vehicle Battery Assembly. IEEE Access, 7, 170961–170991. DOI:10.1109/access.2019.2953712. https://ieeexplore.ieee.org/document/8902005
- Kim, S. et al. (2022). Projecting Recent Advancements in Battery Technology to Next-Generation Electric Vehicles. Energy Technology, 10(8), 2200303. DOI:10.1002/ente.202200303. https://onlinelibrary.wiley.com/doi/abs/10.1002/ente.202200303
- Dy, K.J. et al. (2022). A Survey of Digital Supply Chain Twins’ Implementations. IFIP Advances in Information and Communication Technology, vol 663. Springer, Cham. DOI:10.1007/978-3-031-16407-1_59. https://link.springer.com/chapter/10.1007/978-3-031-16407-1_59
Disclaimer: The views expressed here are those of the author expressed in their private capacity and do not necessarily represent the views of AZoM.com Limited T/A AZoNetwork the owner and operator of this website. This disclaimer forms part of the Terms and conditions of use of this website.