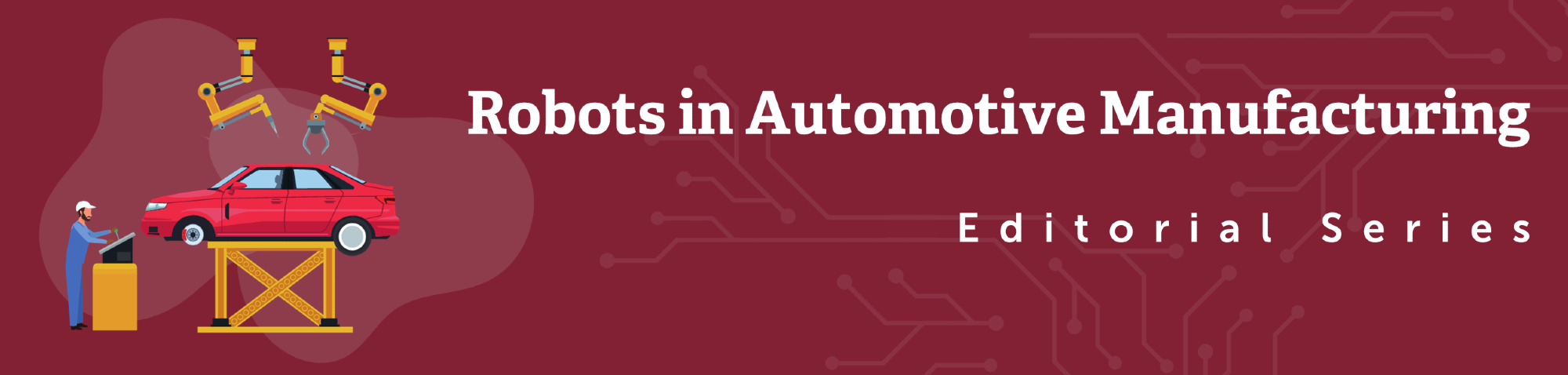
The automotive industry has been an early adopter of industrial robotics and automation. On the factory floor, robotic arms excel at highly repetitive tasks like welding and painting. But beyond the assembly line, there is a massive behind-the-scenes logistics operation to move materials efficiently around large manufacturing facilities. Automotive manufacturers are increasingly embracing robotic and autonomous technologies to optimize their internal supply chain.
Automating material handling offers numerous benefits for automotive manufacturers. Robots can work continuously without breaks, improving productivity and throughput. They also perform consistent, accurate work while eliminating ergonomic strain on human workers. As the industry faces labor shortages and cost pressures, robots and artificial intelligence provide new automation capabilities for internal logistics.
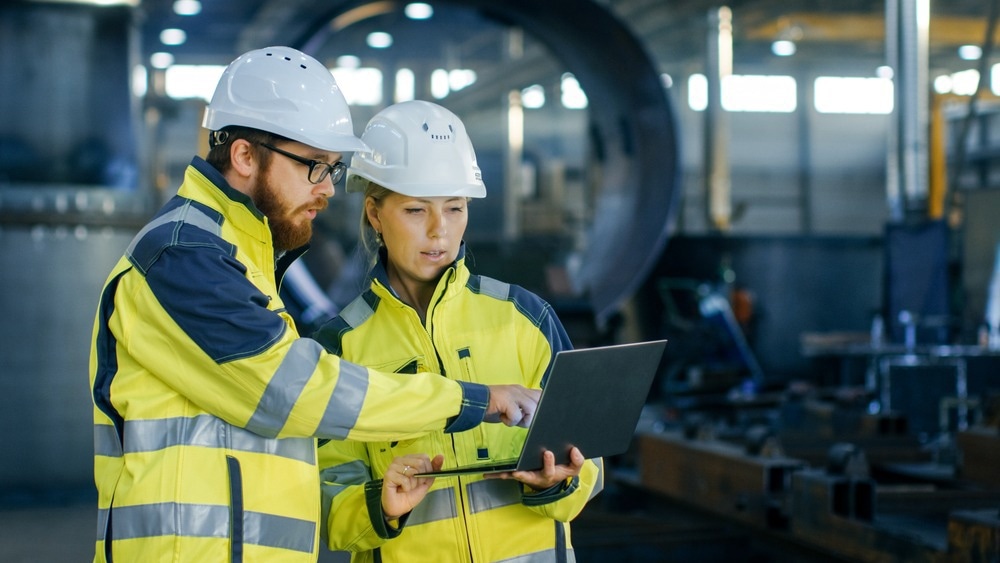
Image Credit: Gorodenkoff/Shutterstock.com
Autonomous Mobile Robots Streamline Intralogistics
One of the most promising technologies transforming automotive internal logistics is autonomous mobile robots (AMRs). These self-driving robots use sensors, cameras, and pre-programmed facility maps to autonomously navigate predefined routes around the plant.
AMRs do not rely on fixed infrastructure like wires, magnets, or lasers to control their movement and can be quickly configured for new routes by updating their maps, allowing automotive manufacturers to adapt rapidly to changing facility layouts and production needs.
Leading manufacturers like Ford, BMW and Faurecia have piloted AMRs for streamlining intralogistics flows. These mobile robots handle material delivery between production areas, warehouses, and line-side assembly 24/7 without human supervision. This takes over tedious material transport tasks from workers, who can be upskilled to more value-adding roles.
Ford Spain has deployed 3 MiR100 robots from Mobile Industrial Robots (MiR) to optimize material delivery to different robotic stations in their body and stamping plant. These versatile AMRs efficiently manage various spare parts and materials via an automated shelving system, resulting in a daily saving of 40 manual hours previously spent on non-value-added activities for Ford.
"The incorporation of the 3 MiR robots has allowed us to turn a routine distribution of spare items into a highly qualified job. We have been able to demonstrate that these robots are capable of learning their way by themselves and also interact perfectly well with our employees and forklift trucks or any other moving element with total safety," Helios Alvarez, Manager of the Body & Stamping plant at Ford.
Faurecia's German plant uses MiR500 and MiR200 robots for fully automated transport of components between their welding, paint and assembly shops. These AMRs integrate with Faurecia's enterprise resource planning (ERP) system to receive transport orders automatically. This automated material handling has increased process efficiency, while the easy reconfigurability of routes enables agile adaptations.
At Visteon's electronics plant in Slovakia, MiR200 robots transport PCBs to production lines, dispose of waste, and move finished components. With the flexible AMRs, Visteon can easily modify requirements and redeploy the robots to new tasks. They achieved ROI in less than a year while gaining the ability to optimize material flows dynamically.
Warehouse Robots Optimize Storage and Picking
Massive warehouse and logistics footprints support automotive manufacturing. Within these four walls, autonomous mobile robots optimize material flows to better utilize space, accelerate order fulfillment, and augment human capabilities.
One common warehouse application is autonomous forklifts for pallet movement and storage. These automated lift trucks can work safely alongside people to keep inventory organized and rapidly accessible. Unlike human-operated forklifts, they don't get tired or distracted, which improves consistency.
DENSO, a global Tier 1 automotive parts supplier, faced labor shortages and safety issues with forklift drivers traveling long distances inside their 800,000 sq ft Tennessee plant. By implementing five automated Toyota forklifts coordinated by Bastian Solutions software, DENSO reduced material transport defects by 48% within months. These reliable, efficient AGVs also allowed DENSO to reallocate 33% of material handling labor to higher-value jobs.
"At this point, we've been operating MiR robots since September 2020, we've run over a half million successful missions, and they have not called in sick one single day," said Travis Olinger, Logistics and Automation Engineer at DENSO.
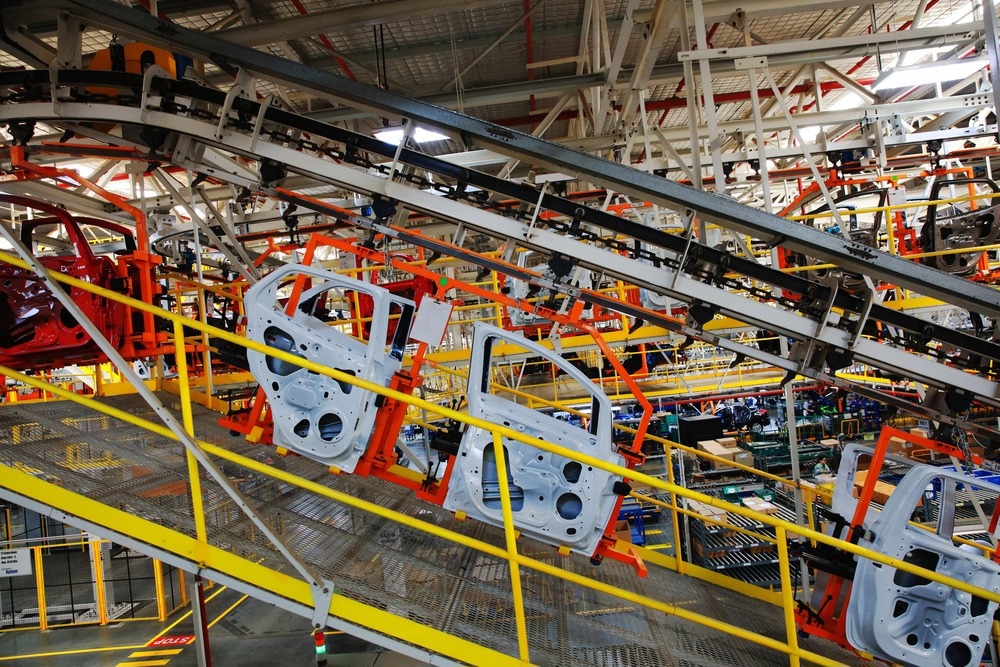
Image Credit: narai chal/Shutterstock.com
Simulation and AI-Enhanced Automotive Logistics Robots
Automotive manufacturers are also harnessing simulation, 3D visualization and artificial intelligence to improve the planning and optimization of internal logistics robots.
BMW is developing a fleet of intelligent, in-house robots to enable faster navigation and object recognition as they transport materials within factories. Powered by NVIDIA's ISAAC robotics software platform, these robots employ advanced deep neural networks (DNNs) to rapidly identify forklifts, people and other obstacles and adjust routes in real-time to avoid collisions, making warehouse and plant navigation safer and more efficient.
The BMW Group has also employed AI and 3D scanning to create digital twins of their facilities. Individual objects like machines and containers can be digitally removed from the 3D scanned model and optimized virtually during planning and simulation. The optimized virtual plans can then be fed to the robots to carry out material transportation and handling tasks automatically.
Autonomous Logistics Critical for Automotive Industry Competitiveness
Automotive manufacturers operate on razor-thin margins and need extremely efficient operations to remain cost-competitive. Automating internal logistics with AI and robotics has become a strategic imperative to minimize non-value activities, improve productivity, adapt to changing market demands, and enable the upskilling of human workers.
As Robert Blackburn, a project leader at DENSO, emphasized, "Technology and innovation are very much a part of what we need to focus on going forward. Basically, if you're not going to focus on that, then you're doing your company or your plant a disservice by not coming out with the best ways to improve on existing manufacturing environments."
Therefore, AMRs, warehouse robots, self-driving forklifts, AI planning tools, and other Industry 4.0 solutions will be critical for automotive companies to optimize logistics and remain competitive now and into the future.
References and Further Reading
Automation.com. (2023). Case Study: Tier 1 Automotive Supplier Accelerates AMR Deployment from Warehouse to Line-Side Production. [Online]. Available at: https://www.automation.com/en-us/articles/february-2023/case-study-denso-amr-deployment-warehouse?fbclid=IwAR1Wa9GDqSnv3c1Y8jq-Ny21dRR8-HRmiEZeFymyQNf4uQSkasv8z8wGRxA (Accessed on 20 September 2023)
Biba, J. (2023). A Guide to Autonomous Mobile Robots. [Online]. Available at: https://builtin.com/robotics/autonomous-mobile-robots?fbclid=IwAR1jrMEx6ZO4e-LVKzXxy9rhwQyGGoDIBgJla7NDIaFkpQxHaihtjsR9oTU
Eitel, L. (2019). Mobile Industrial Robots in collaboration with Faurecia to optimize internal logistics. [Online]. Available at: https://www.designworldonline.com/mobile-industrial-robots-in-collaboration-with-faurecia-to-optimize-internal-logistics/?fbclid=IwAR2EdVLdXL-UlsiRI8VtPJ-ZmYQDYVu9o6nZryrlMmsgPpCX6FCDXu3xCh8 (Accessed on 20 September 2023)
Heer, C. (2023). One Million Robots Work in Car Industry Worldwide – New Record. [Online]. IFR Press Room. Available at: https://ifr.org/ifr-press-releases/news/one-million-robots-work-in-car-industry-worldwide-new-record
Huber, H. (2020). BMW Group is making logistics robots faster and smarter. [Online]. Available at: https://www.press.bmwgroup.com/global/article/detail/T0308393EN/bmw-group-is-making-logistics-robots-faster-and-smarter?language=en
Markov, K., & Vitliemov, P. (2020, June). Logistics 4.0 and supply chain 4.0 in the automotive industry. In IOP conference series: Materials Science and Engineering (Vol. 878, No. 1, p. 012047). IOP Publishing. doi.org/10.1088/1757-899X/878/1/012047
MiR. (2023). Intralogistics Automation in the Automotive Industry. MiR E-book. Available at: https://www.mobile-industrial-robots.com/media/1818118/mir-ebook_intralogistics-automation-in-the-automotive-industry.pdf?fbclid=IwAR1QH_APPvdr6RgByQGPgb2Rjl376QNPckQV3U0jgewOhdOcm6mtsFrS-so
MiR. (2023). MiR robots help FORD Spain optimize intra-logistics in its Car Body & Stamping plant. [Online]. Available at: https://www.mobile-industrial-robots.com/fr/case-studies/mir100-ford-spain/
Disclaimer: The views expressed here are those of the author expressed in their private capacity and do not necessarily represent the views of AZoM.com Limited T/A AZoNetwork the owner and operator of this website. This disclaimer forms part of the Terms and conditions of use of this website.