As part of an Editorial short series, AZoRobotics takes a look at how the renewable energy sector is harnessing the power of robotic technologies. Here, we take a look at robots in hydropower stations.
Hydropower – An Introduction
Hydropower is the oldest renewable energy source that has been crucial in providing sustainable electricity for decades. As the world seeks to transition towards cleaner and greener energy solutions, hydropower remains at the forefront of the energy transition process.
Innovative technologies, such as drones, robots, and autonomous systems, are being integrated into the industry to carry out inspections efficiently and safely to maintain and improve the performance of hydropower plants.
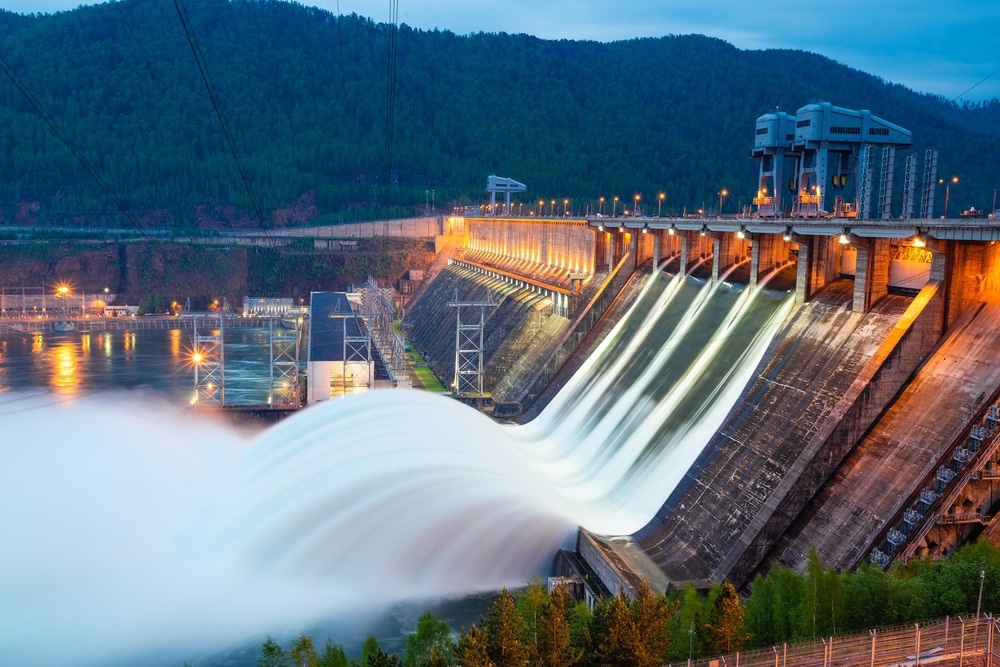
Image Credit: Evgeny_V/Shutterstock.com
Robots in Hydropower Sector
The advent of robotics and digitalization has revolutionized the way inspections are conducted in the hydropower sector. Traditionally, water pipe inspections were limited to external assessments, especially for pipes with smaller diameters. One of the key advantages of using robots and autonomous systems in hydropower inspections is their ability to access confined spaces and dangerous areas that pose risks to human inspectors.
Commercially Used Robots in Hydropower Sector
With continuous innovation and the integration of advanced technology, drones and robots can now carry out inspections in areas where human access is limited or impossible, enhancing the overall safety of inspection processes while ensuring the integrity and optimal functioning of the hydropower plants.
Enel Green Power (EGP)
Enel Green Power (EGP), a leading renewable energy company, has been at the forefront of implementing robotic systems for internal pipe inspections with the capability to provide valuable information about the condition of pipes from within, enabling more precise assessments.
EGP, through open innovation and collaboration with start-ups and research centers, has been actively involved in developing and implementing diverse robotic solutions. For instance, EGP's innovative team created a small, versatile robot with thermal, HD, and thickness sensors equipped with a 3D modeling system and a 4K camera. This palm-sized robot can efficiently conduct inspections of confined spaces and provide preliminary analyses of pipes. Such solutions have become a reality by utilizing the company's internal knowledge and expertise in robotics.
Similarly, EGP's collaborative partnerships with start-ups have led to the development of a gas-detection robot equipped with an "electronic nose" that conducts inspections in hazardous environments and can enter areas where human presence would be risky due to the presence of potentially harmful gases. This improves safety standards and ensures efficient inspections of critical components within the hydropower plants.
China's State Power Investment Corporation (SPIC)
A Chinese company, SPIC, a global hydropower operator, has revolutionized hydropower inspections through AI and robotics by developing the Hydropower Smart Remote O&M System, integrating 29 patented innovations and proprietary software. This system employs robots and drones equipped with advanced tools like image and sound recognition, infrared thermometers, and more to conduct daily patrols and gather data at their Wuqiangxi hydropower plant.
AI processes the data, providing real-time health assessments and generating maintenance suggestions based on equipment condition, optimizing operations. The system's standardized processes enhance efficiency and accuracy, allowing for comprehensive inspections. Deployed in multiple plants, this innovation has reduced maintenance costs by 10%, increased power production time by 0.5%, and improved power generation by 0.3%, marking a significant advancement in hydropower technology.
Falcon Underwater Vehicle
Falcon is another Chinese underwater robotic vehicle for hydropower dam safety and maintenance which plays a crucial role by conducting inspections in challenging conditions, including zero visibility and strong currents. These robots navigate complex structures, tight bends, and lengthy tunnels, providing detailed imaging and data collection for defect detection, corrosion assessment, and debris removal.
The Falcons have been utilized globally, from inspecting inlet pipes during generator operations in Thailand's dams to assessing dam wall integrity and sediment depth in the French Alps. These robotics advancements ensure precise inspection, frequent assessments, and improved diver safety, ultimately contributing to enhanced hydropower infrastructure management.
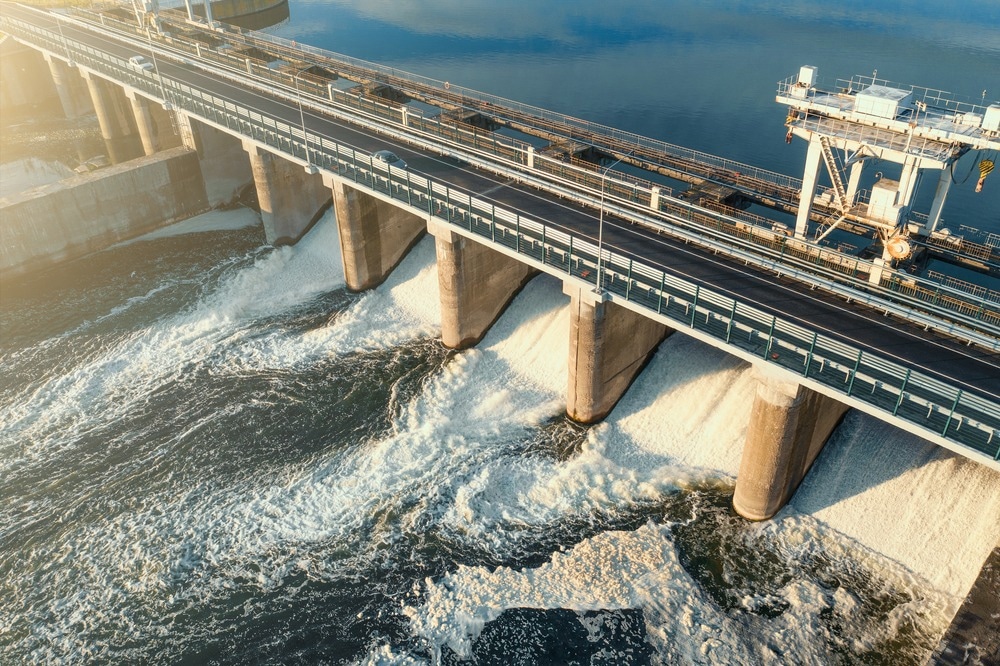
Image Credit: DedMityay/Shutterstock.com
Recent Research
5G Inspection Robot
In a 2022 study, researchers have introduced a novel approach to enhance the identification and resolution of remote faults in hydropower stations by proposing a design method for a remote fault management and control system using a 5G inspection robot.
The system optimizes hardware configuration and enhances software functions to achieve the goal of efficient hydropower station fault management. By integrating 5G technology, intelligent helmets, work cards, and video acquisition equipment, the system captures real-time on-site data and transmits it to a centralized processing system. As a result, timely warnings and information dissemination can be given to operators, thus improving operational efficiency and safety.
The study demonstrates that the proposed system effectively identifies and addresses faults, contributing to the hydropower station's reliable and intelligent operation. Further exploration involves utilizing GPS positioning to overcome challenges in robot localization within complex environments.
The Future of Robots in Hydropower
The prospects of robots in the hydropower sector are promising and transformative. Robots equipped with advanced sensing, monitoring, and maintenance capabilities can revolutionize the industry by performing tasks such as inspecting dams and turbines for cracks or wear, reducing human exposure to hazardous environments. These robots enable real-time data collection, leading to optimized operations and predictive maintenance.
Autonomous underwater robots can efficiently clean intake screens and monitor underwater infrastructure. Additionally, swarm robotics could be employed for complex tasks like sediment removal and environmental monitoring. As the sector adopts these innovations, robots will enhance efficiency, safety, and sustainability, ultimately contributing to the growth and resilience of hydropower as a renewable energy source.
References and Further Reading
Analysing why robotics is so critical to dam safety and maintenance. (2019). Retrieved from https://www.nsenergybusiness.com/features/robotics-dam-safety-maintenance/
ENEL (2023) EGP Innothon challenge: Robots for renewables. Retrieved from https://openinnovability.enel.com/challenges/call/2023/2/robotics-solutions-renewable-plants
ENEL Green Power (2022) The use of robotics in the hydropower sector Retrieved from https://www.enelgreenpower.com/media/news/2022/03/robotics-hydropower-sector
International Water Power & Dam Construction (2019) Analysing why robotics is so critical to dam safety and maintenance https://www.nsenergybusiness.com/features/robotics-dam-safety-maintenance/
Iqbal, J., Al-Zahrani, A., Alharbi, S. A., & Hashmi, A. (2019). Robotics inspired renewable energy developments: prospective opportunities and challenges. IEEE Access. https://ieeexplore.ieee.org/stamp/stamp.jsp?arnumber=8918343
Lin, K., Zhang, X., Fang, W., Wang, R., Wang, W., Hu, M., & Nian, W. (2022). Remote fault management and control system of hydropower station based on 5G inspection robot. In International Conference on Computer, Artificial Intelligence, and Control Engineering (CAICE 2022). SPIE. https://www.spiedigitallibrary.org/conference-proceedings-of-spie/12288/122882F/Remote-fault-management-and-control-system-of-hydropower-station-based/10.1117/12.2641056.pdf
SPIC (2020) Chinese operators are using AI to inspect their power plants. https://www.hydropower.org/case-study/ai-power-plant
Disclaimer: The views expressed here are those of the author expressed in their private capacity and do not necessarily represent the views of AZoM.com Limited T/A AZoNetwork the owner and operator of this website. This disclaimer forms part of the Terms and conditions of use of this website.