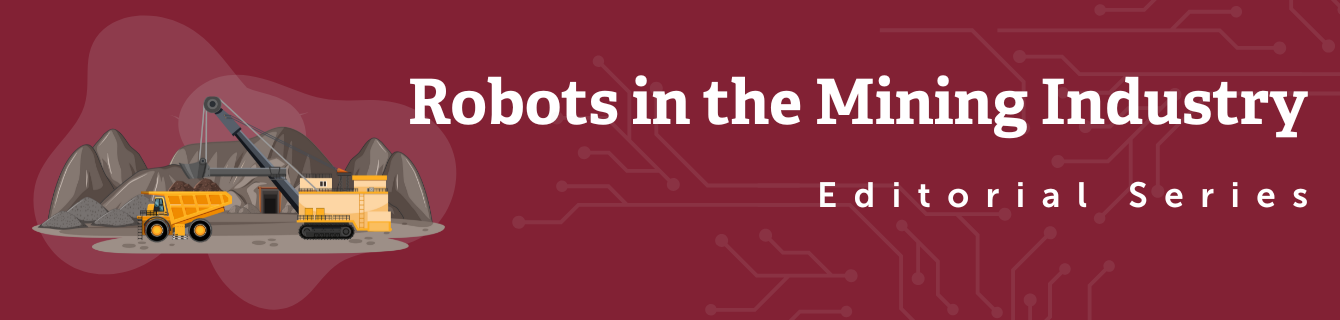
Robots continue to play a central role in mining, offering several benefits over traditional labor-focused operations. This article will briefly explore the use of robots and autonomous technologies in drilling and blasting.
Building the Mine of the Future
Mining is a vital economic activity with a history that stretches back eons. Vast amounts of key resources such as iron ore, copper ore, precious metals, and coal are extracted globally every year to satisfy commercial demand.
The story of mining has been one of technological innovation and progress. From the simplest open-pit mines to the deep underground operations of today, new technologies have improved safety, resource extraction, productivity, and economic output.
The environments in deep underground mines can present unique challenges to mine planners and workers, with complex ore and rock characteristics, dangerous conditions, and the remoteness of mine faces requiring careful planning to avoid catastrophic events.
By 2027, according to some analysts, the global market for autonomous mining equipment will be worth 4.2 billion USD, up from 3.1 billion USD in 2022. Several areas, such as vehicles, plant equipment, software, and communication, drive this growth.
The mine of the future will be a more highly connected, automated environment, with reduced labor needs due to the increased use of Industry 4.0 technologies such as AI, smart sensors, Industrial Internet of Things (IIoT) connected devices, and advanced robotics.
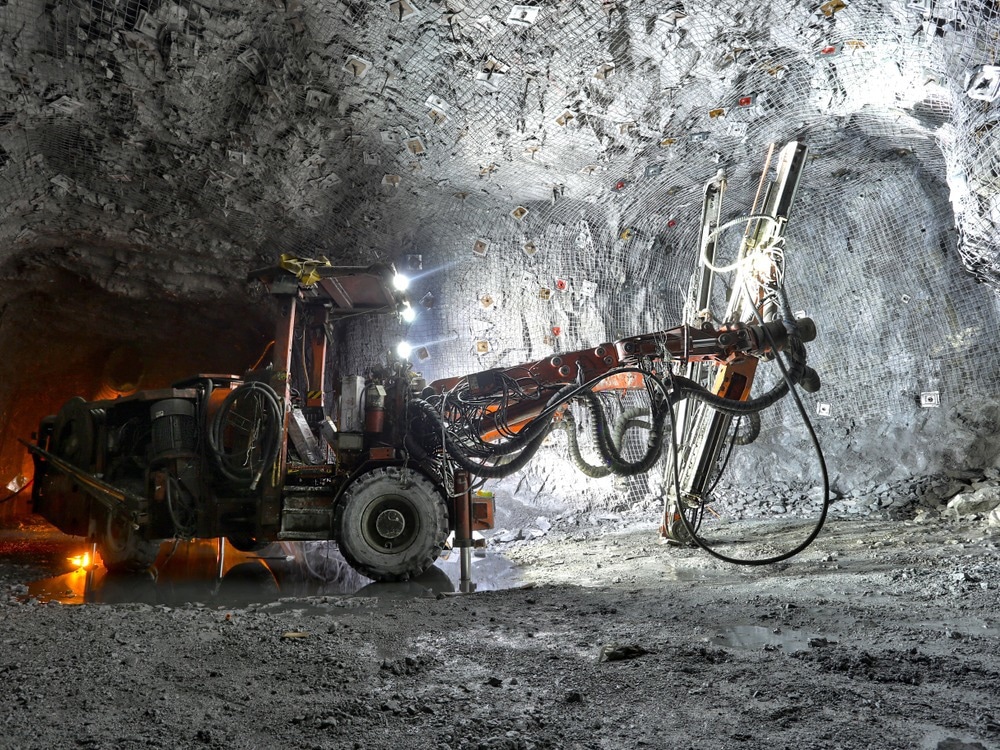
Image Credit: I Made Pasek/Shutterstock.com
Improving Safety with Robots
Worker safety is paramount in mining to avoid catastrophic and potentially fatal accidents such as fires, explosions, and cave ins. Moreover, mines are highly dynamic workspaces, with multiple vehicles and pieces of equipment in operation, presenting a further risk to life.
Mining has become inherently safer compared to previous centuries, despite some well-publicized accidents in recent decades. ICMM members reported 287 occupational fatalities in 2019, a marked increase from 2018, which saw 50 fatalities. There is still much to do to safeguard lives.
The ICMM report notes that the majority of the fatalities in 2019 (250) were due to the catastrophic failure of the tailings dam at the Corrego do Feijão mine. Mobile equipment and transportation accounted for eight fatalities, seven fewer than in 2018, representing a general downward trend in equipment-associated deaths.
Many activities within mines are hazardous, such as surveying, extraction, haulage, and dozing. Increasingly, these activities are being conducted by autonomous robotic systems, saving money and improving productivity. Robots can operate for twenty-four hours without a break (except for routine maintenance.)
Drilling and blasting, for instance, are vital for the extraction of resources but are also extremely dangerous. Automating these activities takes workers away from the mine face, which is one of the most hazardous areas within a deep underground mine.
Case Study: Rio Tinto’s Autonomous Drilling Systems
Several companies are investing in autonomous robotic drilling systems to replace workers at the mine face and improve safety and productivity. Rio Tinto, one of the largest mining corporations in the world, has doubled down on the development of autonomous drilling in the past five years.
According to a 2018 report, Rio Tinto has employed a total of twenty autonomous drilling rigs at its mines in Western Australia.
Rio Tinto’s Automated Drill System (ADS) allows a remote operator, far away from the dangerous mine face, to operate four autonomous rigs fully simultaneously through a single console. This improves equipment utilization and precision.
Between 2008 and 2018, the company’s drills extracted 5,000km worth of material. Rio Tinto’s autonomous robotic systems can perform exploration, infill, and production drilling.
Semi-Automated Explosives Delivery System from Orica and Epiroc
Orica, explosives and blasting systems provider, and Epiroc, a mining equipment manufacturer, announced a joint effort in 2019 to develop and implement semi-automated explosives delivery systems for blasting.
The result of this joint effort was Avatel, which is a twin-boom, fully mechanized, and semi-autonomous explosives charging system. A single operator can fully deploy explosives and complete the charging cycle safely. The operator sits in a fully protected cabin.
According to Orica, the Avatel robot is equipped with the most advanced underground development charging system on the market. One of the key challenges with fully automating the blast cycle is sufficiently providing manual connections to initiate the blasting process.
This problem is resolved by an in-hole initiating system. A firing command signal can initiate the process remotely (even through water and rock) and a failsafe boosts system safety. Energy control is completely controlled by operators remotely.
Worker safety is improved, operational downtime is reduced, and productivity is enhanced by the Avatel system. Moreover, the system could make it easier for mining companies to access deeper ore pockets, even in areas that provide challenges due to seismic activity or other issues.
In Summary
The future of mining lies in increased automation. Robots are playing an increasing role in the industry, replacing workers in dangerous and increasingly deeper and remote environments.
This article has provided a brief exploration of automated drilling and blasting systems in the mining industry. Automating these operations will bring enhanced safety and productivity benefits for mines, reducing instances of fatal accidents and providing round-the-clock capabilities.
References and Further Reading
Turner, J (2018) Mining robots: Rio Tinto doubles down on autonomous drilling [Online] mining-technology.com. Available at: https://www.mining-technology.com/features/mining-robots-rio-tinto-doubles-autonomous-drilling/
Hall, M (2021) Digitising drill and blast operations [Online] mining-technology.com. Available at: https://www.mining-technology.com/features/digitising-drill-and-blast-operations/
Greenwood, M (2022) Orica Creates Rock-Blasting Robot for Safer Underground Mining [Online] Available at:https://www.engineering.com/story/orica-creates-rock-blasting-robot-for-safer-underground-mining
Markets and Markets (2022) Mining Automation Market Global Forecast, 2027 [Online] marketsandmarkets.com. Available at: https://www.marketsandmarkets.com/Market-Reports/mining-automation-market-257609431.html
Disclaimer: The views expressed here are those of the author expressed in their private capacity and do not necessarily represent the views of AZoM.com Limited T/A AZoNetwork the owner and operator of this website. This disclaimer forms part of the Terms and conditions of use of this website.