The necessity for manufacturing and distribution enterprises to fulfill customer expectations for more variety and quicker delivery is driving many to explore new methods to automate their operations. The employment of mobile robotic systems is one such solution.
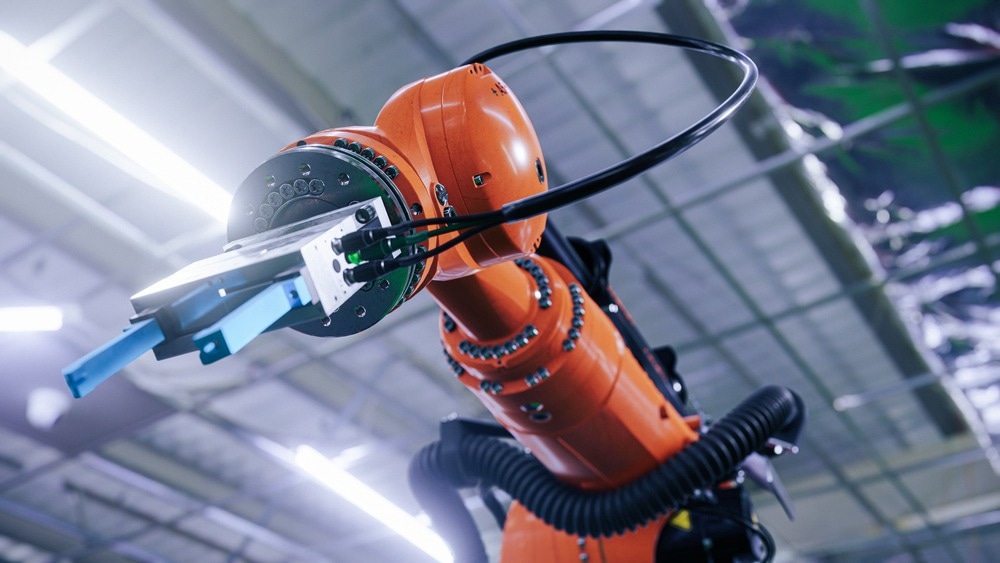
Image Credit: C SCREEN/Shutterstock.com
Mobile robots, which include automated guided vehicles (AGVs) and autonomous mobile manipulation robotic systems (MMRSs), are becoming increasingly popular in industrial operations as organizations seek to utilize their current workforces more efficiently while also enhancing efficiency and productivity.
Mobile Manipulation Robotic Systems – Robots on Wheels
A mobile manipulation robotic system is essentially a robot that incorporates a manipulator arm with a mobile platform, integrating the benefits of both technologies into a single product: the accuracy, delicacy, and versatility of the manipulator and the mobility and autonomy of the mobile platform
The ability of mobile manipulation robotic systems to perform repetitive mechanical activities while covering whole work shifts makes them indispensable instruments for any sector seeking to put itself at the technical forefront and maintain a key position in today's competitive environment.
All organizations participating in the Industrial 4.0 framework are now able to engage in collaborative mobile manipulation. Collaborative mobile manipulation allows multiple autonomous mobile manipulators to operate synchronously and securely in human-populated situations.
Mobile manipulation robotic systems are often employed in industrial applications such as handling, loading/positioning, assembling, screwing, drilling, inspection, and testing.
What Makes Up a Mobile Manipulation Robotic System?
Mobile manipulation robotic systems usually consist of three main hardware components: the manipulator, the tool, and the mobile base, coupled with an array of sensors for localization and augmentation.
The manipulator is usually a robotic arm with multiple degrees of freedom consisting of the base, elbow joints, and shoulder, allowing for large degrees of motion for the robotic arm. Similar joints at the end of the manipulator provide wrist-like motion to the tool. The tool can be anything from a gripper for handling to a drilling device.
The mobile base is a platform with wheels or tracks that carries all the components of the mobile manipulation robotic system, including the robotic arm, batteries, electronics, and the sensor suite.
The sensor suite comprises an array of sensors for multiple tasks; these tasks include localization, which helps the robot determine its position in a particular space and its location relative to other items in the environment. These localization-based sensors are coupled with proximity sensors for collision avoidance.
A successful mobile manipulation robotic system usually incorporates an augmentation system which helps in providing a simulated visual representation of the system to the operators.
This system needs an additional array of sensors to smoothen the user experience and provide as many visual inputs as necessary to perform desired tasks and to provide a real-time view of the surroundings to the operator throughout the task.
Industrial Examples of Mobile Manipulation Robotic Systems
Robotnik, a manufacturer of robotic systems, has been a forerunner in the design and implementation of autonomous mobile manipulation robotic systems, extensions of commonly used autonomous mobile robotic systems.
One of Robotnik's latest success stories predicated on an industrial application at the Dutch gear manufacturing business Hankamp Gears BV illustrates mobile manipulation robotic systems integrated into the industry.
The RB-KAIROS+, an autonomous mobile manipulator, is a novel collaborative mobile manipulator robotic system that was created specifically for industrial applications. The RB-KAIROS+ robot is designed for logistical and manipulation tasks, such as pick and place, machine tending, fetch and carry, and operations on large components.
The RB-KAIROS+ is made using industrial-strength steel and can carry almost 250 kilograms of weight. The 360° kinematics of the mobile platform are based on four high-power drive wheels. The mobile manipulation robotic system is equipped with a URe10 arm manipulator with various sensors, including a safety laser scanner, 2D LiDAR, a 3D camera, six degrees of freedom camera, and a tool camera.
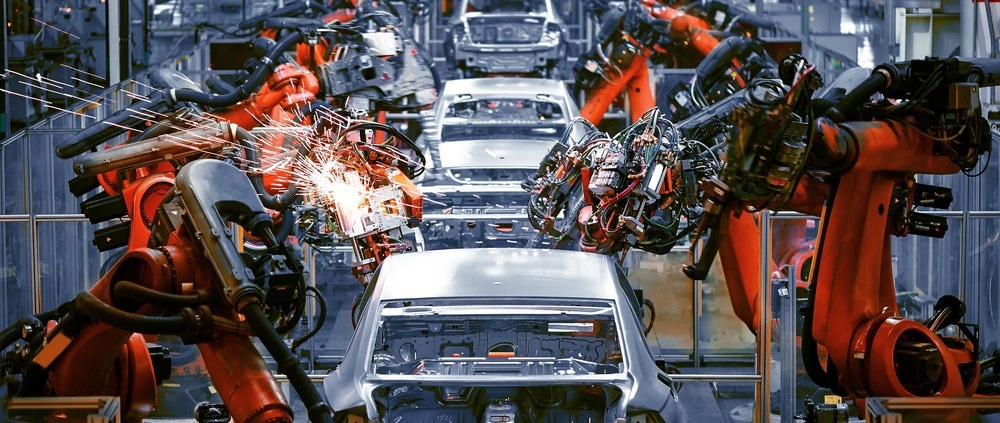
Image Credit: Jenson/Shutterstock.com
Latest Advancements in Mobile Manipulation Robotic Systems
Recent advancements in artificial intelligence (AI), computer vision, and navigation, along with a considerable reduction in costs, have made autonomous mobile manipulation robotic systems more practical for a wide variety of activities.
With the ever-increasing capabilities of robotic systems, these systems have become more capable of reacting in real-time to their operational surroundings, avoiding barriers such as humans, and determining the optimum pathways to minimize transit times and enhance efficiency.
Recent advancements in areas including 2D and 3D computer vision have increased the amount and quality of data being provided to mobile manipulation robotic systems. This improvement in data has directed companies towards implementing edge-based systems to deliver the required computational power for big data processing and relay the necessary information to the analytical engine at groundbreaking speeds, allowing for accurate real-time decision-making.
Edge-based computing offers a scalable alternative to acquiring and maintaining extra hardware and software in-house, lowering both cost and complexity while allowing mobile manipulation robotic system fleets and their capabilities to be expanded as needed.
References and Further Reading
Robotnik (2022). Mobile manipulators: the intelligent production for your factory. Robotnik. Available at: https://robotnik.eu/mobile-manipulators-the-intelligent-production-for-your-factory
Annem, V. et al. (2019). Towards Remote Teleoperation of a Semi-Autonomous Mobile Manipulator System in Machine Tending Tasks. International Manufacturing Science and Engineering Conference. doi.org/10.1115/MSEC2019-3027
Artigas, J. (2022). Mobile robot use on the rise in manufacturing. Control Engineering. Available at: https://www.controleng.com/articles/mobile-robot-use-on-the-rise-in-manufacturing
Disclaimer: The views expressed here are those of the author expressed in their private capacity and do not necessarily represent the views of AZoM.com Limited T/A AZoNetwork the owner and operator of this website. This disclaimer forms part of the Terms and conditions of use of this website.