One of the most valuable applications for robots is working in environments too hazardous for humans. For example, robots working deep underground or below the sea, on other planets, and in dangerous industrial environments like nuclear power plants. In 2021, a consortium of UK engineering and robotics companies and researchers launched an advanced robot for hazardous environment maintenance: the Connect-R.
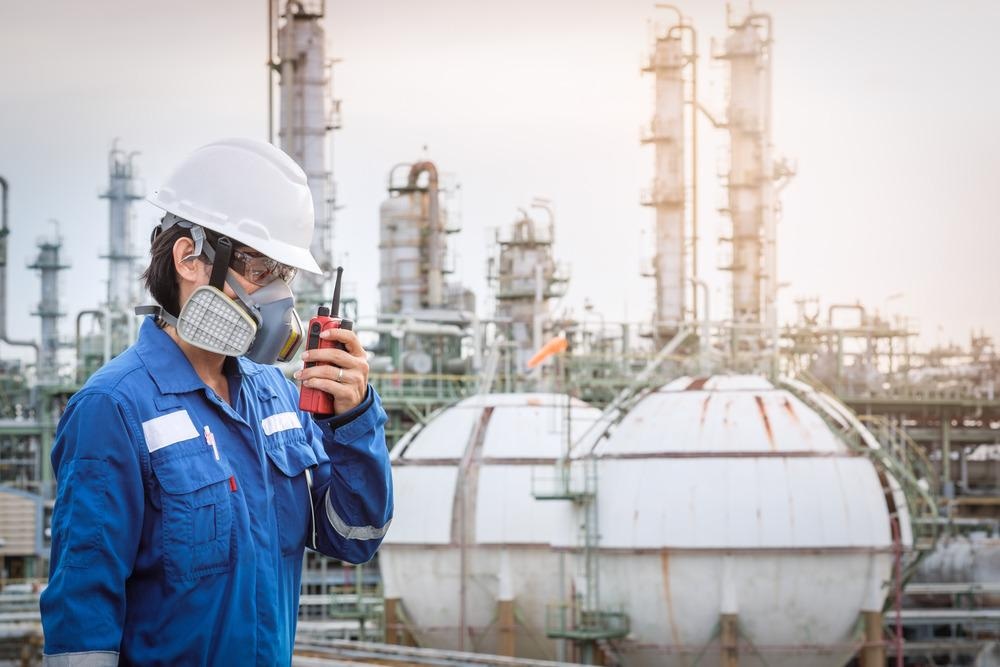
Image Credit: mmmx/Shutterstock.com
Extremely Ruggedized for Hazardous Conditions
The Connect-R is the first modular robot in the world that is designed to undertake missions in hazardous environments and build emergency structures autonomously. It is an industrial-scale robot structure that builds itself on site.
It is made for conditions where hazards like radioactivity, unbreathable air, and unstable structures make any work too risky to human life.
Because it can self-build, the Connect-R completely removes human workers from the equation when it comes to planning works in hazardous environments. It could reduce the large risks associated with decommissioning nuclear power plants, and make building in outer space a reality.
The robot can withstand radioactivity, extremely hot or cold temperatures, high pressures, high acidity and alkalinity levels, and it can operate in a total vacuum.
Modules Self-Assemble Into an Industrial-Scale Robot
The Connect-R is a robotics system made up of modular sections joined together with a combination of hydraulic and electric motors and in-built sensors. An artificial intelligence (AI) program sequences the best possible configuration for the robot and controls the motors to put itself together.
This “body” can then lay down infrastructure for further operations. It can also shore up compromised structures, such as buildings damaged by earthquakes or nuclear material storage containers decayed with age.
Individual modules can extend from 1.5 m to 2.5 m, and the system can be used to build structures as large as entire spacecraft, factory floors, or buildings according to the consortium behind its development.
The Connect-R has a reconfigurable “multi-task bot” included. This smaller robot helps the larger system build itself by moving elements of the system around and completing construction and maintenance tasks on the main structure. A sophisticated AI also powers the small robot, and it can analyze its surroundings and move around autonomously.
Major Breakthrough for UK’s Industrial Strategy
This project achieved a number of discrete technological breakthroughs on the path to developing a modular, self-building robot system for industrial applications in hazardous environments. To get there, it received £6 million in funding from the UK government’s science and technology investment agency.
The UK government is pursuing an industrial strategy that targets growth in advanced and high-value manufacturing, and builds on local expertise in a number of industrial digital technologies (IDTs) that support this growth. Robotics is a key IDT for the UK’s economic ambitions.
To produce the Connect-R system, the partners working on the project had to tackle several important challenges in robotics and engineering.
They created the first AI path planning software that could make a robot work a previously unreachable area in a 3D space. The software engineers used symbolic planning to overcome this.
The team also created a new micro-sized hydraulic component that could cope with intense loads while enabling modular units to move in any direction.
They invented a “genderless” connection system to interlock modules across flat planes. Dropping the conventional “male” and “female” ports for mechanical locking systems means Connect-R modules can connect from any plate to any plate on any other module.
Finally, a control architecture for the hydraulic system was developed to enable valve and control elements to fit into small spaces. The team used a novel hydraulic circuit system to pack all of Connect-R’s hydraulic controls in as small a space as possible.
World-Leading Robotics in the UK
The Connect-R project was led by Barrnon, an engineering firm based in Cumbria, UK, that specializes in robotic engineering for harsh environments. The project was built around Barrnon’s prior experience in removing and extracting waste from extremely radioactive environments.
Barrnon’s founder and managing director, Andy Barr said: “It started as an idea, then became a concept, and now it’s deployable in harsh radioactive environments. It’s the culmination of lots of hard work from the team and many stakeholders. I am proud of it as it’s a step-change in robotic accessibility.”
ROSS Robotics, a UK-based leader in robotics, also joined the project. ROSS was responsible for developing the modular, reconfigurable robots used in the Large Hadron Collider at CERN, Switzerland, as well as robots for inspection and analysis of contaminated zones near Chernobyl.
A leading UK robot manufacturer, Tharsus, provided consulting for the project, while Jigsaw Structures carried out design and analysis. The AI was developed by Royal Holloway University of London while the University of Edinburgh’s Centre for Robotics perfected the control systems.
Continue reading: RE2 Robotics to Subdue Submerged Mines with Intelligent Autonomous Systems
References and Further Reading
Asher, C. (2021). Episode 5 – Robots for Hazardous Environments. Robot Talk. UK Robots and Autonomous Systems Network. [online] Available at: https://www.ukras.org/RobotTalk/episode-5-robots-for-hazardous-environments/.
Cumberland & Westmorland (2021) Herald.Breakthrough robotics system to tackle the world’s most hazardous environments. [online] Available at: https://cwherald.com/news/breakthrough-robotics-system-to-tackle-the-worlds-most-hazardous-environments/.
Disclaimer: The views expressed here are those of the author expressed in their private capacity and do not necessarily represent the views of AZoM.com Limited T/A AZoNetwork the owner and operator of this website. This disclaimer forms part of the Terms and conditions of use of this website.