AZoRobotics speaks to Prof Matt Reed, Strategy Director for the Materials Innovation Factory (MIF) at the University of Liverpool, about how the application of industry 4.0 technologies such as robotics and automation can unlock chemistry and advanced materials research and innovation.
Can you explain what the Materials Innovation Factory is and how it works?
The Materials Innovation Factory (MIF) at the University of Liverpool is an £81 million facility designed to significantly speed up the discovery process of new materials and provide potential solutions to a range of global challenges, including climate change, clean water, and battery energy storage.
The 12,000 m² MIF building is “open by design”, meaning the labs, staff, and advanced equipment are available for use by any academic or industry specialists alike. A dedicated team of technical experts is located on-site to assist with experiments and train scientists on how to use our cutting-edge kit. The MIF is founded on a strategic innovation partnership between the University of Liverpool, Unilever, and UK Research and Innovation.
Since opening in 2017, the MIF has attracted funding from commercial partners and the Henry Royce Institute – the UK’s national institute for advanced materials research and innovation. We are changing the way that functional materials are designed at the atomic scale by fusing chemical knowledge, state-of-the-art computer science, lab automation, and digital research and development techniques.
World-class knowledge leadership in materials chemistry is the value-creation engine at the core of the MIF. We are home to pioneering and highly decorated scientists, including Professors Andy Cooper and Matt Rosseinsky who are both Fellows of the Royal Society, and Professor Steve Rannard. It is this scientific excellence that attracts funding and produces a constant stream of publications in quality journals.
How does the MIF use robotics and lab automation to accelerate materials discovery and design?
The MIF houses one of the highest concentrations of materials science robotics in the world and a suite of advanced analytical equipment. Our expertise in automated materials discovery has enabled us to develop a bespoke robotic platform – the Formulation Engine. Capable of handling multiple workflows simultaneously, the modular Formulation Engine allows a range of automated techniques to be flexibly incorporated into a research workstream.
MIF researchers at the University of Liverpool have also built and developed an intelligent mobile robot chemist capable of carrying out its own experiments and working around the clock with minimal human intervention. Developed by Professor Andy Cooper and Dr Benjamin Burger, the 1.75-meter-tall robot chemist is equipped with a high level of artificial intelligence, allowing it to learn as it works and make its own decisions about which chemistry experiments to perform next.
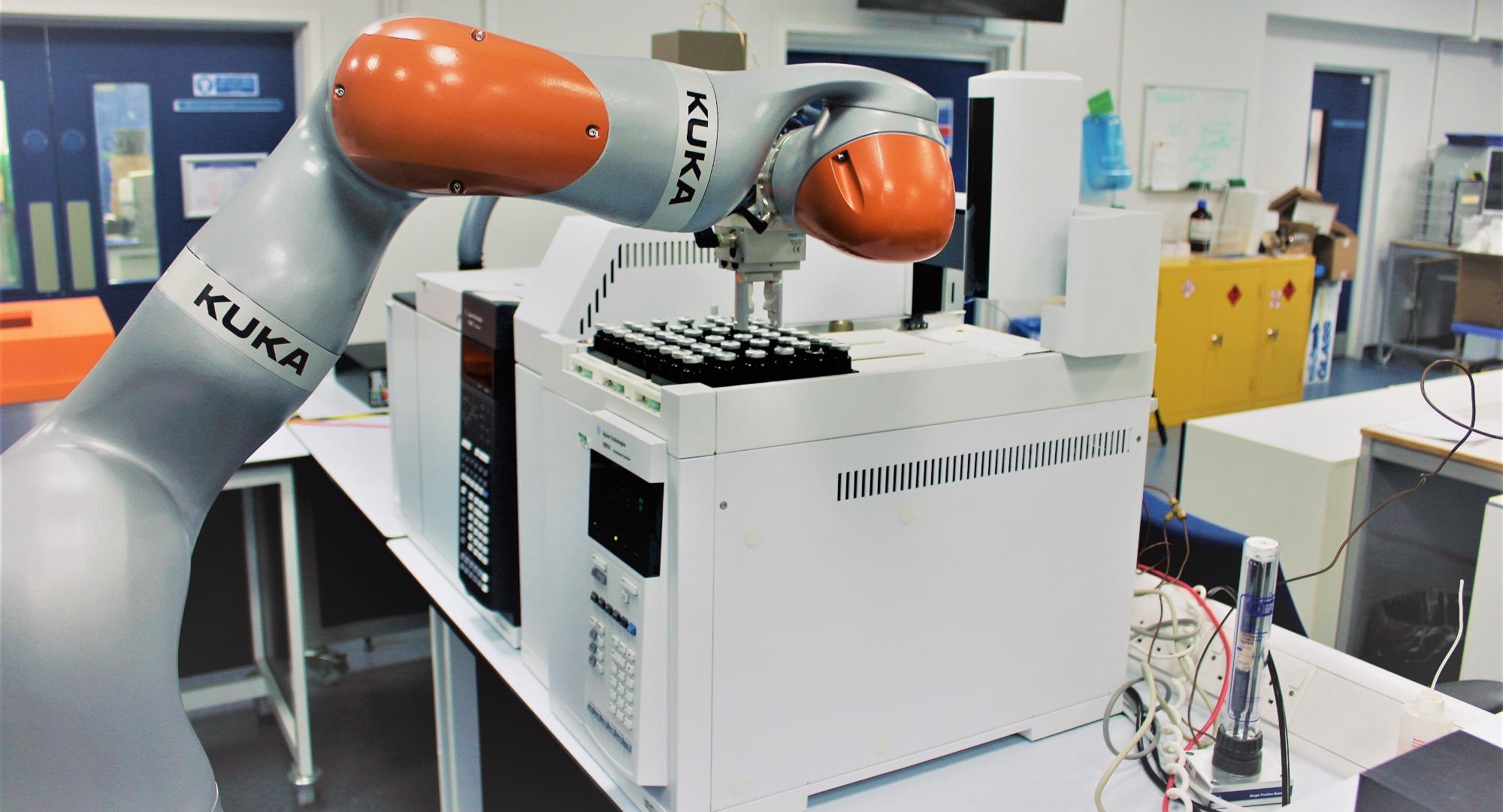
The University of Liverpool has developed the robot chemist to intelligently carry out tasks around the laboratory with minimal human intervention. Image Credit: University of Liverpool
The robot chemist works with equipment designed for human operation because of its human-like dimensions and physical reach. It uses a combination of laser scanning coupled with touch feedback for positioning, rather than a vision system.
The robot independently carries out all tasks in the experiment such as weighing out solids, dispensing liquids, removing air from the vessel, running the catalytic reaction, and quantifying the reaction products. This work has already led to a new start-up business called Gearu to provide commercial companies with innovative mobile robotic solutions in their own R&D labs.
Your new lab partner: A mobile robot chemist
Video Credit: nature video/YouTube.com
What is innovation 4.0 and how does it differ from industry 4.0?
The fourth industrial revolution (Industry 4.0) continues to transform the manufacturing sector. By harnessing the power of advances in digital technologies such as artificial intelligence (AI), machine learning, robotics, and virtual reality technologies, it is creating new opportunities and economic growth.
These “digital” techniques are not purely virtual. In addition to new classes of virtual assets, such as data and “digital twins”, these new technologies have had a transformative effect on the physicality of manufacturing, the use of robots for multiple tasks, the layout and specification of factory units, the way that manufacturing staff work in those units, and the sensor and data infrastructure of manufacturing plants.
An opportunity exists to apply similar digital technologies, both virtual and physical, to the R&D and innovation process itself. The systematic application of digital technologies to innovation has, by analogy with Industry 4.0, become known as Innovation 4.0.
What are the benefits of applying innovation 4.0 technologies to research and development for companies in the chemical and pharmaceutical sector?
The majority of R&D leaders in academic science, commercial research, product development, and innovation activities expect that over the next five to ten years, digital techniques will become increasingly mainstream in R&D, including in the materials chemistry industries. These leaders believe that these technologies have the potential to deliver a step-change in the innovation efficiency of UK and global materials chemistry industries.
Laboratory work remains a crucial value-creating activity for organizations in these industries.
This lab work is not optional: it is how they meet customer needs, create resilience in their activities, innovate, create competitive advantage, secure IP, guarantee the quality of manufactured goods, and justify advertising claims. Much of this lab work is currently manual and its efficiency will not easily be improved without investments in digital technologies and in particular, lab automation.
Lab automation can be used for research, product development, and testing, and is also of high value for routine lab testing in a production environment for both quality control (QC) and quality assurance (QA).
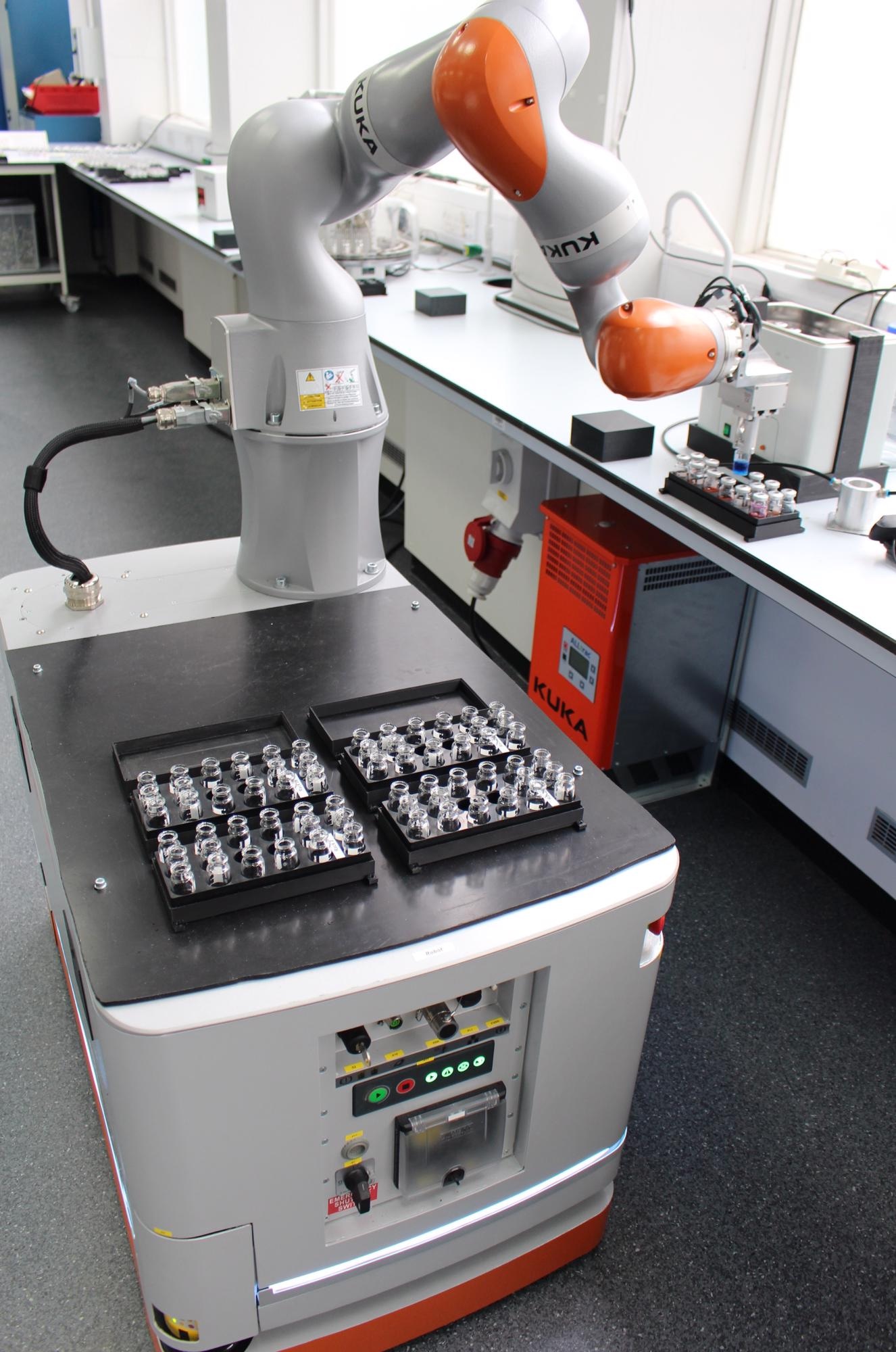
Image Credit: University of Liverpool
Lab automation can simultaneously improve the reproducibility, traceability, reliability, and intensity of lab operations compared with current manual approaches. Even relatively modest improvements in each of these factors can deliver 2x to 10x improvements in the efficiency of the automated lab process. Lab automation can therefore make a substantial contribution to improving the end-to-end innovation efficiency of SMEs, academic labs, and multinational corporations.
Although the sector invests £6 billion in R&D (75% in pharmaceuticals) and employs ~ 40,000 FTE, it has seen lower levels of action on digital R&D compared with the stated ambition of its senior leadership. This reflects the significant barriers which need to be overcome for the widespread deployment of digital R&D in materials chemistry. Many organizations in the chemical and pharmaceutical sectors are looking for help in planning and implementing digitization roadmaps for their organizations.
Most UK-based materials chemistry companies have low levels of investment and expertise in digital R&D approaches. This is partly due to the very high fragmentation of the sector: 92% of the 3,700 active companies in the sector have less than 100 employees. The sector as a whole is therefore systematically under-exploiting lab automation and missing out on the potential benefits of increased efficiency in their lab operations.
If lab automation is introduced in the right way, it not only delivers a quantifiable and rapid return on investment (ROI), but it is also an excellent way to engage the creativity and energy of existing lab staff in moving the company towards more digitized R&D. Automated lab work addresses issues of experimental excellence, data quality, reducing the volume of waste chemicals, reducing the burden of repetitive manual tasks, and perhaps most importantly to create more space in their daily lab work for invention and discovery.
What impact would the adoption of robotics and advanced automation technologies within chemistry and advanced materials R&D have on productivity and economic growth at the national level?
The UK materials chemistry industries (including chemical, pharmaceutical, rubber, and plastic manufacturing) are a strategic part of the UK’s manufacturing base, both in terms of scale and long-term innovative capacity.
The Chemicals & Pharmaceuticals sector has an annual turnover of £62.8 billion, with £18.3 billion Gross Value Added, which is about as large as the Automotive & Aerospace sector. If rubber and plastics manufacturing are included, the turnover is £87 billion, with £27 billion Gross Value Added.
The chemicals industry has delivered long-term gains in total factor productivity (a proxy for innovation). Its cumulative performance from 1995-2016 was better than financial services and pharmaceuticals. End-user applications of the chemistry value chain include:
- Pharmaceuticals & medicines
- Household and personal care products
- Agrochemicals and fertilizers
- Food and drink
- Paper and pulp
- Life sciences
- Automotive
- Aerospace
- Construction
There is room across this sector for additional increases in innovation efficiency and overall productivity. The adoption of automated techniques in the labs at the heart of this sector’s operational and innovation activities would lead to a step-change in the sector.
What impact has the COVID-19 pandemic had on research and development activities in labs?
Since early 2020, COVID-19 lockdowns have had a major impact on lab usage worldwide and within the UK. It is possible in many office and factory environments to apply social distancing regulations, such as staying two meters apart, but in many chemistry labs, it has been hard to implement these restrictions without significantly reducing the overall capacity of the lab.
Initial analyses by the Materials Innovation Factory and its commercial partners in May 2020 indicated that social distancing had reduced some lab activities to less than 25% of their pre-COVID capacity. This is a substantial loss of innovation capacity, which will lead to an ‘innovation deficit’ and an erosion of future profitability for the UK. We estimated that the total loss of portfolio value caused by COVID-19-related lab disruption could easily exceed £3 billion.
Prompted by the COVID-19 lockdowns, an interest in developing technological means for running lab activities more remotely has emerged. This approach would increase staff safety, improve company monitoring of regulatory and health and safety performance, help employees to work more flexible hours, help those with caring responsibilities, and also allow individuals with disabilities to drive experimental programs who would otherwise have difficulty with laboratory access.
The Power of 10X: Using Materials Innovation to Reach Net Zero
Video Credit: UofLTube/YouTube.com
Where can readers find more information?
To learn more about Materials 4.0, readers can visit the Royce website: https://www.royce.ac.uk/collaborate/roadmapping-landscaping/materials-4-0
My white paper which sets out a roadmap for increasing UK prosperity from the use of robotic science in materials innovation can also be read and downloaded for free via the Royce website: https://www.royce.ac.uk/content/uploads/2021/06/Materials-4.0-Lab-Automation-for-Innovation-in-Materials-Chemistry.pdf
Finally, to learn more about the Materials Innovation Factory more broadly, readers can visit our website: https://www.liverpool.ac.uk/materials-innovation-factory or get in touch via email: [email protected]
About Professor Matt Reed
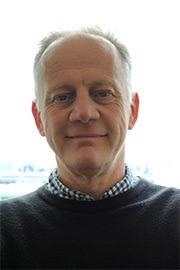
Professor Matt Reed is Strategy Director of the Materials Innovation Factory (MIF) at the University of Liverpool. Matt has a technical background in chemistry, quantitative microscopy, and data science. He holds an Executive MBA in Technology Management and Open Innovation, and has worked for Shell Research and Unilever R&D in both the UK and the Netherlands. He has also published scientific papers, filed patents, co-authored three books, and co-founded three companies based on his intellectual property. He is a Fellow of the Royal Society of Arts.
Matt joined the MIF 2019, but had worked since 2013 to help co-create the facility in partnership with leading academics at the University of Liverpool, Unilever R&D, and the UK Government. In his current role, Matt works to create, maintain and exploit strategic high-impact innovation partnerships between the University of Liverpool, other leading-edge academic institutes, government funding bodies, and commercial innovators.
Disclaimer: The views expressed here are those of the interviewee and do not necessarily represent the views of AZoM.com Limited (T/A) AZoNetwork, the owner and operator of this website. This disclaimer forms part of the Terms and Conditions of use of this website.