Article Updated 12 May 2021
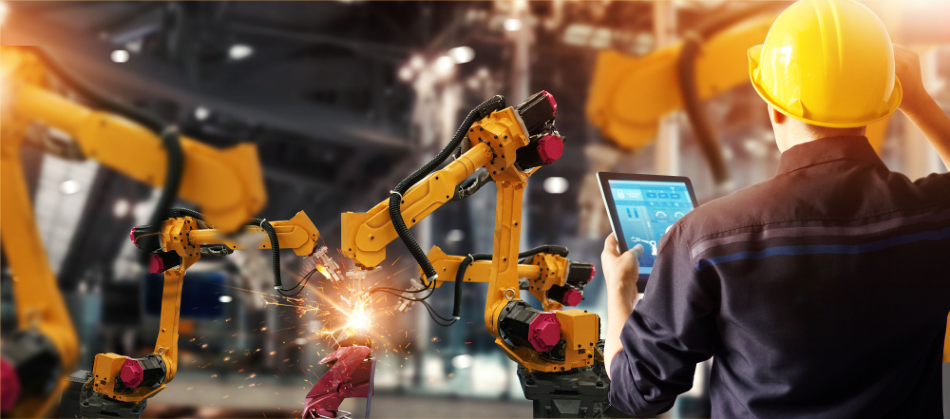
Image Credit: PopTika/Shutterstock.com
Optical emission spectroscopy (OES) is a widely used analytical technique for the identification of elements in samples. It is commonplace in metal-producing industries, such as steel and copper manufacture, and in fabrication industries.1
OES’s power as a technique for elemental identification has seen its widespread adoption within industrial automation. It works by detecting light emitted from atoms or molecules that have been excited to higher energy states, typically using an energetic electrical discharge source.
The excitation or discharge source promotes electrons to higher energy levels from which they subsequently relax and emit light. The emitted wavelengths of light are detected, and their specific wavelengths are characteristic of the emitting atom.
An optical emission spectrometer is composed generally of three main components: the excitation source, a diffraction grating, and the detector.
Read more: An Overview of All Spectroscopic Techniques Used in Robotics
The diffraction grating spatially separates the different emitted wavelengths of light, so a position and intensity sensitive detector can be used to record all the various components or spectral lines that the emitted light is composed of.
What makes OES such a powerful analytical technique is that the energy spacings of the spectral lines reflect the underlying electronic structure of the emitting species.
As there may be hundreds of lines in the emission profile, these can be fit to known reference data for unambiguous assignment of the presence of an elemental species. With suitable calibration, the intensity of the light can also be used to quantify concentrations of different elemental species.2
The Advantages of Using Optical Emission Spectrometers for Automation
The relative simplicity of optical emission spectrometers makes them ideal for integration into automated industrial processes. One common application of OES is for quality control in wafer manufacturing.
Plasma deposition is commonly used to create layers of chemical species onto a substrate, and it is critical that all wafers are treated in the most similar way possible.
OES can be used to monitor the conditions in the plasma and the relative ratios of different chemical species to monitor the progression of the chemical reaction and more accurately determine the best endpoint for the processing.3
Click here for more information on service robotics and automation.
For this type of fabrication process, the data output of the spectrometer can be integrated as part of a feedback system with the manufacturing process.
Automation of data analysis and element identification is relatively straightforward and is suitable for use in many types of deposition processes, including atomic layer deposition for the creation of ultra-high quality thin films.4
Automated OES is also a popular tool in metallurgy. OES can be used to identify a wide range of elements, including carbon and phosphorous, but works particularly well with softer metals, as they are more easily ‘sparked’ or excited during the initial excitation step.
Impurity testing as part of quality control is one common use of automated OES, but this can be extended to investigative work looking at how the presence of impurities and their relative concentrations have on the physical properties of a material.5
Multiplex Analysis
Another advantage of OES for automated analysis and processing is that minimal sample preparation is required. Even for more complex samples such as soils, OES can be used as a direct measurement of most solids or any plasmas that are formed as part of the manufacturing process.
Where required, different excitation techniques such as glow discharge or plasma induction can be used to optimize conditions for the detection of specific elements.
Inductively coupled plasma optical emission spectroscopy (ICP-OES) is a variety of OES that uses a high-temperature argon plasma to ionize the sample of interest.
There are many commercial ICP-OES instruments available that are optimized for the analysis of multiple elements in the same experiment. This is important for automating processes where several contaminants may be an issue and for minimizing the analysis time under such conditions.
While the sensitivity of ICP-OES may not be as high as mass spectrometry variants of the technique6, for industrial processing OES has the advantage of being significantly cheaper in terms of equipment cost and less demanding in terms of personnel training.7
However, the sensitivity of ICP-OES is still sufficient for use in most applications that do not require the detection of ultra-trace levels of elements. Sample processing and analysis times also often compare favorably.
Efficiency and Quality
Many commercial optical emission spectrometers are available with robot-based automatic samplers for analysis. This makes for more straightforward process integration, for example, in applications such as metal identification and scrap sorting.
Automation reduces processing bottlenecks and extended operating times with the advantage of complete reliability and reproducibility in the processing and analysis of samples.
Particularly for industries, such as the semiconductor industry, that rely on plasma processing for fabrication, which is often challenging to control in a reproducible fashion, automated OES can be a significant cost and efficiency-saver given that testing of devices often accounts for a large proportion of manufacturing costs.8
References and Further Reading
- Zhou, Z., Zhou, K., Hou, X., & Luo, H. (2005). Arc / Spark Optical Emission Spectrometry : Principles , Instrumentation , and Recent Applications Arc / Spark Optical Emission Spectrometry : Applied Spectroscopy Review, 40, 165–185. https://doi.org/10.1081/ASR-200052001
- Devia, D. M., Rodriguez-Restrepo, L. V., & Restrepo-Parra, E. (2015). Methods Employed in Optical Emission Spectroscopy Analysis : a Review. Ingenieria y Ciencia, 11(21), 239–267. https://doi.org/10.17230/ingciencia.11.21.12
- Gifford, G. G. (1990). Applications of Optical Emission Spectroscopy in Plasma Manufacturing Systems. SPIE Advanced Techniques for Integrated Circuit Processing, 1392, 454–465.
- Mackus, A. J. M., Heil, S., Langereis, E., Knoops, H., van de Sanden, M., & Kessels, W. (2010). Optical emission spectroscopy as a tool for studying , optimizing , and monitoring plasma-assisted atomic layer deposition processes. Journal of Vacuum Science & Technology A, 28(1), 77–87. https://doi.org/10.1116/1.3256227
- Al-mejali, J. A., Haarberg, G. M., Bensalah, N., Benkahla, B., & Lange, H. P. (2016). The Role of Key Impurity Elements on the Perfomance of Aluminium Electrolysis - Current Efficiency and Metal Quality. Light Metals 2016, 389–394.
- Lienemann, C. P., Dreyfus, S., Pecheyran, C., & Donard, O. F. X. (2007). Trace Metal Analysis in Petroleum Products : Sample Introduction Evaluation in ICP-OES and Comparison with an ICP-MS Approach. Oil and Gas Science and Technology, 62(1), 69–77.
- Perkin Elmer (2020) Atomic Spectroscopy – A Guide to Selecting the Appropriate Techniques and System https://www.perkinelmer.com/lab-solutions/resources/docs/BRO_WorldLeaderAAICPMSICPMS.pdf (Accessed on March 27 2020)
- Ward, P. (1995). Plasma Process Control with Optical Emission Spectroscopy. IEEE International Electronics Manufacturing Technology Symposium, 166–169.
Disclaimer: The views expressed here are those of the author expressed in their private capacity and do not necessarily represent the views of AZoM.com Limited T/A AZoNetwork the owner and operator of this website. This disclaimer forms part of the Terms and conditions of use of this website.