Article Updated 8th April 2021
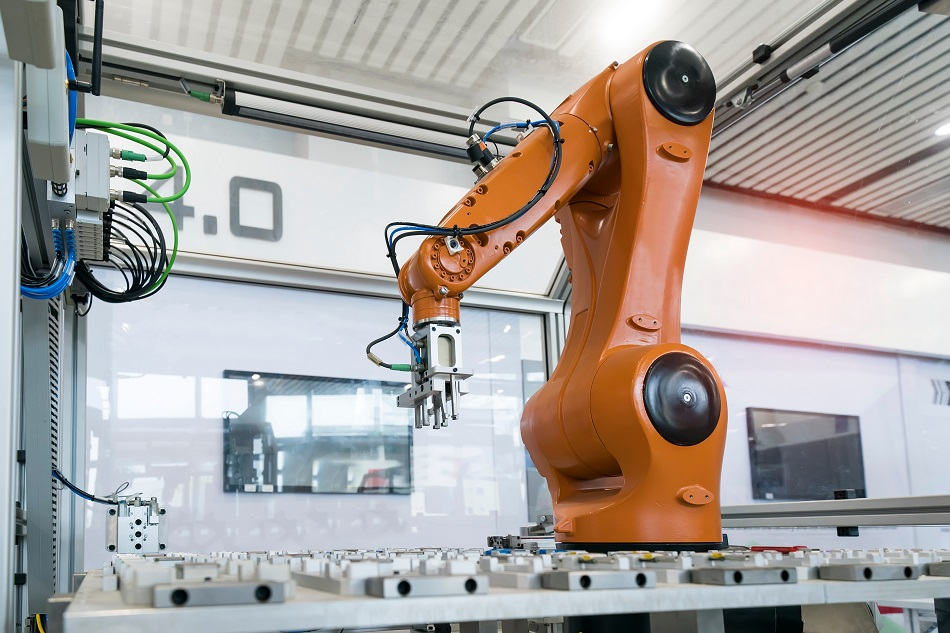
Image Credit: asharkyu/Shutterstock.com
In today’s economy, there is increasing pressure on manufacturers to adopt the agile approach to production, and industrial robotics are an attractive option for companies embracing this approach. The versatility and adaptability of modern robotics make them well suited to agile manufacturing.
Operational industrial robots come in many different shapes and sizes. Performance testing is being used to quantify the defining abilities of these robots and to perform evaluations of various robot systems based on how well they perform these abilities.
Non-destructive tests (NDT) can inform purchasing and implementation decisions. The test techniques that have been developed also inform employee training programs and the development of more advanced robot capabilities.
Industrial robots are often found in agile manufacturing environments, which are known for ongoing and unpredictable change. An agile environment may require a robot to respond to a type of failure, the introduction of a new goal, or a major change in environmental conditions.
NDT was established in the United States by the National Institute of Standards and Technology (NIST). It is used for the assessment of industrial robots and involves tasks for the robot to complete, a test apparatus, and standardized test metrics.
This article describes three categories of NDTs for industrial robots.
Baseline Kit Building Tests
The objective of these test procedures is to assess how well the software controlling an industrial robot can handle a task and minor changes. These tests are used to generate baseline test outcomes that the performance of a system can be evaluated against.
The main goal of a Baseline Kit Building Test is to create a mechanical kit from parts as specified. It begins with a group of parts being put into the kit tray. The parts can be specific to particular production needs if the objective is to compare robotic systems on how well they perform against explicit use cases or situations.
In a typical kit building test, one of the tasks requires the system to pick up parts from the tray and place them down in a specific location and orientation. Another standard task involves picking up shaped pegs and inserting them into a block with appropriately shaped holes.
The metrics for this test are based on time, distance, task completion rate, and failure rate.
Dropped Part Test
Created as a way to test agility, the Dropped Part Test assesses if the system is capable of sensing individual kit parts as they move and how well the system can ascertain the successful completion of an activity.
How effectively the system copes with an unexpected obstacle can be evaluated in relation to the Baseline test results. Its performance in the test can represent how the system will operate in real-life situations.
During the test, a part is forcibly dropped from the grasp of a robot while the robot is moving the part. A duplicate part is also placed in the parts storage bin.
Test technicians then assess the system to see if it notices that the part has been dropped. They also evaluate how the system was able to notice the dropping of the part if an alert was produced, if and how the robot picks the part up, and if the robot instead picks a duplicate part from the storage area to be placed in the kit tray.
The metrics for this test are similar to those of the Baseline test, with the ‘failures’ metrics being mostly focused on the various steps of the dropped part scenario.
In-Process Kit Change Test
This test method is designed to assess how well a system can adapt to a sudden change of plan. It particularly looks at how well a robot is able to stop working on one order and begin working on a higher-priority order.
The test involves the introduction of a higher-priority kit while the robotic system is already in the process of building a kit and has at least two parts stored in the kit tray.
Test technicians observe the system to see if and when it noticed the new kit. They also evaluate if the system assesses the kit tray to see if the part from the lower-priority order can be used in the new order if it removed unnecessary parts from the kit tray, and if the partially-completed kit is set aside in favor of the new kit.
The metrics for this test are the same as those used in the Baseline test. Additional metrics include ‘yes/no’ metrics for tasks that are specific to the in-process test.
Sources and Further Reading
Disclaimer: The views expressed here are those of the author expressed in their private capacity and do not necessarily represent the views of AZoM.com Limited T/A AZoNetwork the owner and operator of this website. This disclaimer forms part of the Terms and conditions of use of this website.