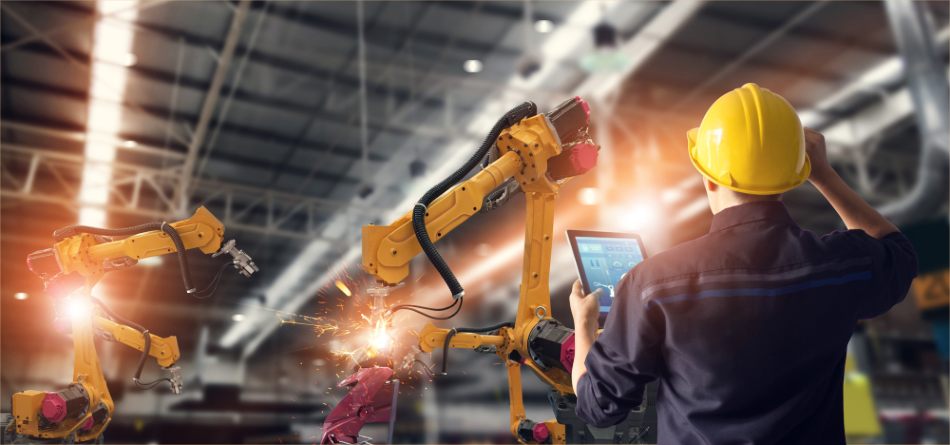
Image Credit: PopTika/Shutterstock.com
In industrial automation facilities, sensors play a pivotal role to ensure safety in the production unit by predicting and preventing numerous potential hazards. These sensors should be positioned accurately to detect any gaseous accumulation before it creates a serious hazard.
The main problem for gas detection systems is that there are no precise guidelines for approximately 95% of installation systems.
Typically, gas sensory systems only have industry-approved best practice guidance protocols for its proper installation. This is because of the varied complexity in the behavior of individual gases. There are over 400 gases and each gas has its own unique sets of properties, which poses difficulties for detection.
The position of a gas detector is primarily determined by the purpose of its usage. Several important factors to be considered for the best positioning of a gas sensor in the industry are discussed below.
Important Factors when Positioning Gas Sensors
Leakage Monitoring
In the case of leakage monitoring, the measuring head is installed with due consideration to the likely points of leakage, such as, flanges, valves, pressure reducers, pumps, etc. This enables leakage detection at the earliest.
Area Monitoring
For area monitoring such as in solvent and paint warehouses, where there are no well-defined potential leakage sources, the detectors are uniformly distributed throughout the hazardous area in view of local flow conditions.
Detectors are placed in the inhalation area (head height) in areas such as laboratory workplaces, where there is a possibility of leakage of toxic gases.
Click here for more information on industrial robotics.
In the case of a possibility of gas entering a confined space, the gas sensors are positioned close to ingress points. For instance, in the case of landfill gas entering a building, the sensors should be placed close to the drains or underground cable conduits.
The dispersion characteristics of gases depend on its density and ventilation patterns. The knowledge of gas density helps to determine the height where the sensors should be positioned relative to the potential source.
For example, methane gas is less dense than air and so it will rise. However, vaporized liquefied petroleum gas (LPG) is heavier than air and so it will remain at a low level. In the case where a gas is about the same weight as air, the sensor must be positioned two to eight feet above the ground.
Prolonging the Operational Life of Sensors
To prolong the operational life of sensors, positioning them in susceptible zones should be avoided due to excessive vibration or heat, contamination, mechanical damage, or water damage. If there are no alternative locations, suitable protection, including vibration isolation mountings, should be provided. This will ensure the longevity of the sensors.
Preventing Sensor Errors
Sensors should not be placed near entrances or fresh air vents, as sample concentrations will be diluted by incoming air and error will take place. Gas leak detection equipment is very sensitive and this is the most desirable property that one would expect in a gas sensor.
Monitoring Airflow
Airflow must be monitored. The gas detection monitors must be positioned in a neutral zone. Gas detection systems use a pump to draw in a sample. Therefore, if air is flowing around the collection point, it may provide inaccurate readings.
Adding detection points in ventilation ducts allows you to correct faulty cylinders or incorrect storage methods.
The direction or velocity of the airflow must be duly noted as gas flowing from the potential leak sources to the detector is essential.
Identifying Appropriate Gas Detector Types
The identification of the most appropriate gas detector type is essential. A gas sensor must be fast, accurate and must not be affected with the cross-interference of other gases present in the area.
In an industrial automation facility that contains lead, sulfur or other fumes, a catalytic-type gas sensor must not be used. These gas fumes could damage the catalytic beads and reduce detection sensitivity.
How Much Area Should a Gas Detector Cover?
Even though there are no official standards that specify an exact area of coverage of gas detector, the general guidelines for fixed-point gas detectors in open areas is approximately a 5 m radius coverage for each detector, or 75 to 100 square meters per detector.
Extra detectors must be placed near potential leak sources or where a gas cloud could accumulate.
Sources and Further Reading
Disclaimer: The views expressed here are those of the author expressed in their private capacity and do not necessarily represent the views of AZoM.com Limited T/A AZoNetwork the owner and operator of this website. This disclaimer forms part of the Terms and conditions of use of this website.