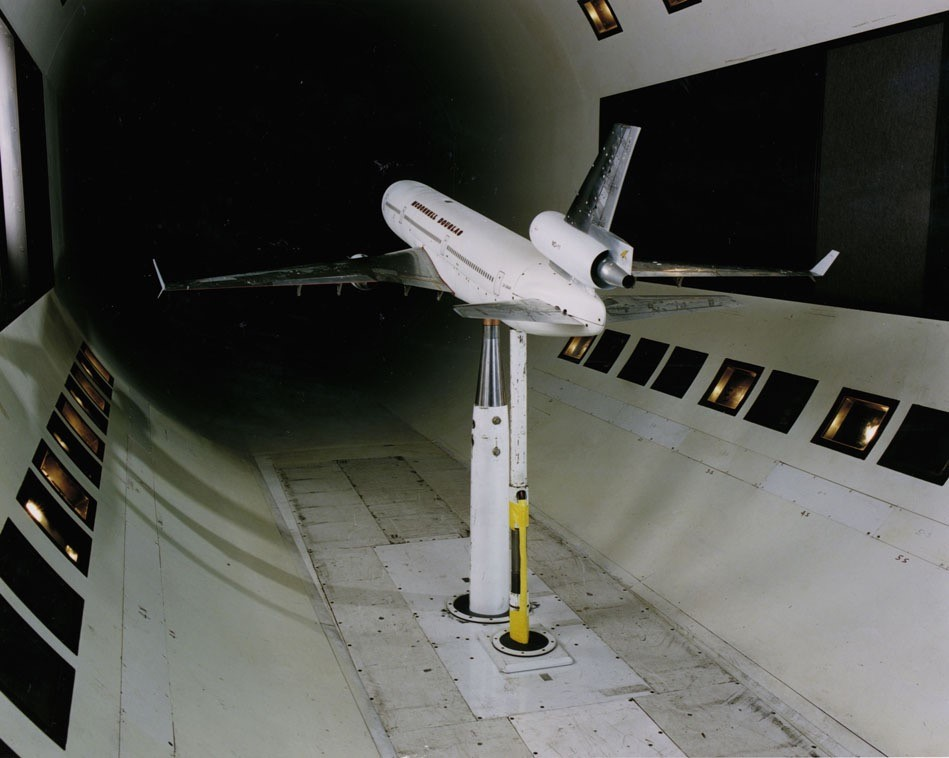
Airplane builders have used NASA wind tunnels to test new airplane designs. Image Credit: NASA.
The introduction of control systems engineering into the public consciousness has opened several doors, making things previously thought impossible possible. Improvements to the field of control systems engineering allow for more complex and precise execution of tasks by machines with very little error.
The History of Control Engineering
Although control engineering is a relatively new field, the use of automatic control dates back to over 2,000 years ago and is observed in the ancient water clock. Automatic control reemerges in 17th century Europe where open-loop control was used in small dancing figures to keep them repeating the same task over and over.
The next breakthrough was the implementation of closed-loop feedback control and new mathematical techniques for optimal control. In a closed-loop system, the output value of a system regulates the input into the system, making it possible to achieve more robust control.
These breakthroughs in control made space travel possible, allowing for the spacecraft attitude to be altered to align with its desired orbit with high precision and efficiency. Classical control methods, such as PID control, changed the world since their discovery. The use of differential equations to model a physical phenomenon allows for any process to be controlled so long as it represents behavior with a mathematical model.
Recent Advancements in System Modeling, Simulation and Control Engineering
We lie at a technological tipping point in history, where we, as humans, are beginning to model computer processes to mimic the workings of the human brain. Computers are now able to progressively learn from previous iterations of a scenario and improve on its response.
The advent of narrow artificial intelligence and computer vision will have a significant impact on robotics control. Control is primarily based on selecting the right control inputs to make a system stable using a derived mathematical model or transfer function.
Although wear e still a long way from using AI to determine the required control, artificial intelligence will prove largely useful in understanding the various unknown parameters used in the model.
When making a product, an integral part of the design stage is testing and experimentation. This is done by creating different experimental models for testing the product design. An example of this is through the testing of aerodynamic properties of specific aircraft designs in a wind tunnel.
For this design to be approved, different experiments have to be modeled by the engineer to prove the effectiveness and safety of the design under normal to extreme conditions. In larger design projects such as the design of space shuttles and bridges, there is very little room for error as unanticipated problems could be fatal.
To avoid malfunctions, vigorous testing becomes a huge part of the design process. Every scenario needs to be taken into consideration as a result of this engineer's attempt to model experiments to simulate the different possible scenarios.
Physical experimentation falls short when trying to understand the performance of a design under extreme conditions. This is solved by the use of computer simulations based on the systems governing physics.
The computer simulation discipline involves designing a model of an actual or theoretical physical system, executing the model on a digital computer, and analyzing the execution output (Fishwick, 2015). Before a computer simulation is processed, a design model is created and parameters are then inputted based on what is being tested.
Computer simulations are important as errors are easily identified since the computer runs every possible scenario and simulates the different conditions the product would be subjected to.
During results analysis, flaws are corrected. If the designer previously overlooks a condition, control systems can be put in place to help adapt the design to the overlooked condition. This makes running computer simulations useful in the design process. Recent advances in the design process can be seen in generative modeling. This involves using an AI to determine the optimal geometry for design depending on its desired purpose.
System models and simulations help push testing designs to their limits with little to no cost. In the design process of bridges, different structures are taken into consideration, and these structures have to be tested to determine the most efficient and cost-effective design.
Testing a design in extreme conditions can prove difficult or impossible in the real world. An example includes testing a bridge design in extreme conditions such as tornados or hurricanes. With the use of computer simulation, any possible situation can be replicated in the model, or experiments in a controlled environment such as a wind tunnel can be carried out. Computer simulation can help perform tests and experiments at a faster time scale. Some designs need to last a lifetime, and testing properties of materials over a long period is a lot easier with computer simulation.
The use of computer simulations has proven to be more cost-effective for several engineering sectors. Design projects are primarily based on a budget, so any option to reduce costs is usually better accepted.
The use of computer simulations has given us the ability to gain detailed insight into problems that may not have been obvious at the beginning. It also allows us to target these issues and build structures or products which are more fit for the function. Along with this, we have improved financial savings. The use of simulations allows for innovation to occur at a faster rate as failures can be disregarded earlier in the designing process.
References and Further Reading
NASA (2020). Airplane builders use NASA wind tunnels to test new airplane designs. [Image] Available at: https://www.nasa.gov/audience/forstudents/k-4/stories/nasa-knows/what-are-wind-tunnels-k4.html [Accessed on 30th February 2020].
Dorf, R. and Bishop, R. (2017). Modern control systems. Essex: Pearson.
Control of Temperature Using PID Controller. (2015). International Journal of Science and Research (IJSR), 5(5), pp.1203-1206.
Disclaimer: The views expressed here are those of the author expressed in their private capacity and do not necessarily represent the views of AZoM.com Limited T/A AZoNetwork the owner and operator of this website. This disclaimer forms part of the Terms and conditions of use of this website.