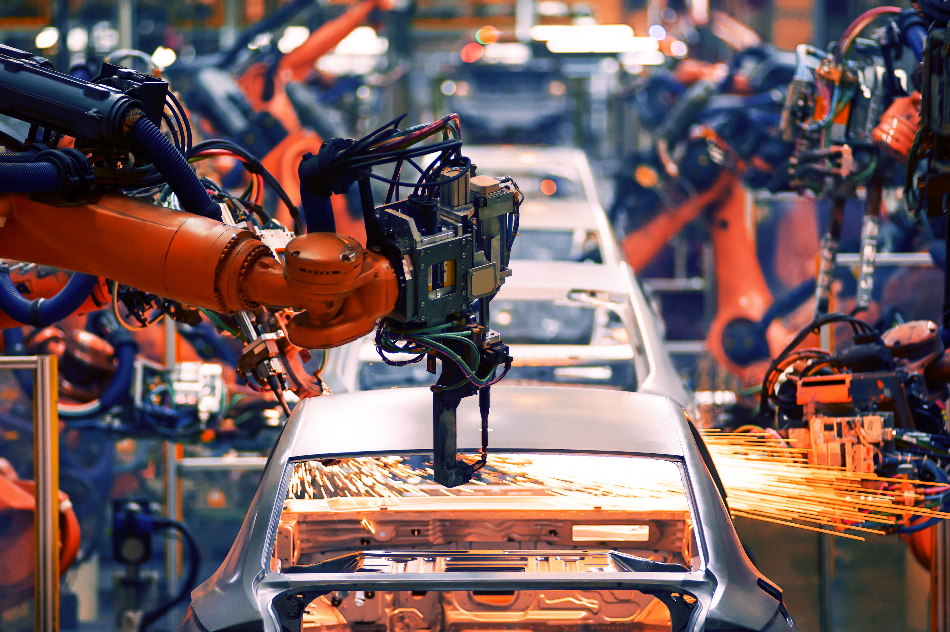
Jenson / Shutterstock
In 2018, 98.1 million motor vehicles were produced globally. One-quarter of all passenger cars are made in Europe, with the US and Greater China being responsible for a large share of the remaining majority. Whilst Henry Ford receives a lot of the credit for the introduction of the industrial production line, it is in Japan where the origins of modern car production can be found.
Modern lines have not changed much since the basic system which was made famous by Ford so long ago. Workers often still operate at individual stations on the line as cars come to them for individual tasks to be performed. The main differences in modern production compared to the older lines lies both in design and technology.
Platform Sharing
In the 1950s, cars were assembled from the ground up in one factory with all parts produced on site. Now car companies buy parts from different companies with many of the parts no longer made on site. The reason this method is widely used is due to platform sharing. To save on time and costs, most car companies will design cars to share parts with different makes and models. This makes production easier and provides consumers with more choices in purchase, repairs, and maintenance.
Efficient Adaptations to Production Lines
Most modern industrial lines use intelligent designs to maximize efficiency. The U-line is the most well known and used production line in car manufacturing. All processes are kept close at hand with operators able to monitor their own station as well as the stations of others. This reduces the risk of error and increases quality control. The U-line is also scalable meaning that human workers can be increased or decreased depending on production demands.
Another modern adaptation to the production line is the Joint Application Development concept (JAD). This concept allows all areas of the process to be connected. From design to quality control, every stage of production is connected holistically between departments. IT is connected with design to assembly to quality control and back to design. This allows projects to be completed quickly and on budget, reducing errors and enabling increased car production.
Robots on the Line
The exo-skeleton system and robot support glove (Roboglove) are now two of the most widely used ‘cobots’ (cooperative robots) used on modern car production lines. The exo-skeleton support frame provides workers with increased strength and support when working in difficult areas of assembly. The frame also provides muscular support and strength when working underneath a vehicle, whilst the Roboglove provides increased grip and strength when workers need to fix bolts and tighten sockets. Robots are common in the modern production line, reducing injuries and accidents that before would mean the end of a worker’s career.
Robots have also taken over most of the duties in the paint shop. Still one of the most expensive sections of a modern production line, robots have made a big difference in performing most of the tasks. The application of protective corrosion coatings, sealants, primers, base, and clear coatings are now all performed by robots monitored by a single human operator. The BMW plant in Spartanburg, South Carolina uses over 100 robots to ensure the car is coated correctly. The task takes 12 hours. Compare this with the 3-5 day turnaround a traditional paint shop requires, and it is easy to see the benefits a robot on the line brings.
Drones have also been introduced in modern car production lines. They are used by General Motors in their casting plants to inspect sand delivery pipes and identify issues; an inspection that would traditionally pose a high risk to human workers. The drone flies around in a cage surveying the pipes and reporting cracks and other potential problems that could cause a line shutdown.
Stock systems are also now being updated to reduce wastage utilizing cloud-based software connected by tablets on the floor. Stock cabinets housing spare parts and replacements used to require separate record manuals that an operator would have to consult. The SEAT factory in Martorell, Spain, introduced a new system that allows operators to access the stock records of individual cabinets from their tablets. Using QR codes, scanners and camera workers can access the parts they need quickly and monitor stock levels more efficiently.
Is Automation the Future?
Not exclusively. Whilst many industrialists still believe that automation will transform industrial car production further, the human factor remains a critical component. Robots are not replacing workers. They are collaborating, with ‘cobots’ like the exo-skeleton and roboglove, enhancing the native ability and performing high risk and repetitive tasks efficiently. Humans are still needed to ensure quality control is maintained. The next challenge lies in adapting modern lines to produce the inevitable high waves of electric cars expected over the next decade. With VW already dedicating its plant in Zwickau, Germany to manufacture electric only, other companies will soon follow to keep up. Extensive automation is part of the integration process, with 1,700 production robots and driverless transport systems expected to increase production by 20%. However human operators are still required to oversee the process and ensure standards are met.
Sources
Disclaimer: The views expressed here are those of the author expressed in their private capacity and do not necessarily represent the views of AZoM.com Limited T/A AZoNetwork the owner and operator of this website. This disclaimer forms part of the Terms and conditions of use of this website.