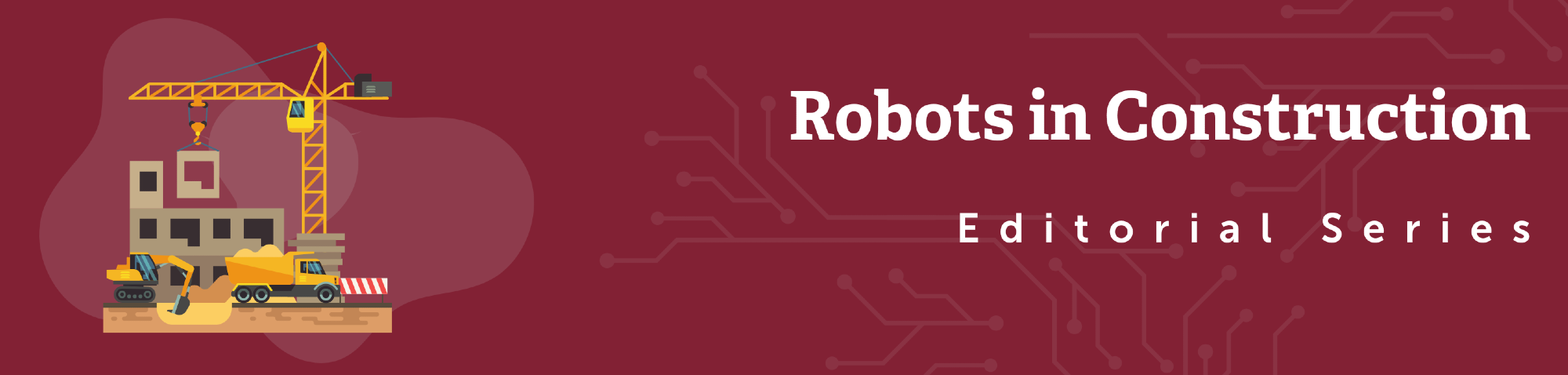
Demolition, one of the most labor-intensive and hazardous tasks in construction, has traditionally relied on manual labor, exposing workers to dangers such as collapsing structures and flying debris. This led demolition contractors to increasingly adopt robotic solutions for safer, more efficient, and precise operations.
Demolition robots are revolutionizing the construction industry by enabling uninterrupted, continuous operation, minimizing downtime, ensuring a favorable return on investment, and delivering consistent and accurate performance. Simultaneously, they prioritize safety, alleviating ergonomic strain on human workers and allowing them to concentrate on more cognitive-oriented responsibilities.
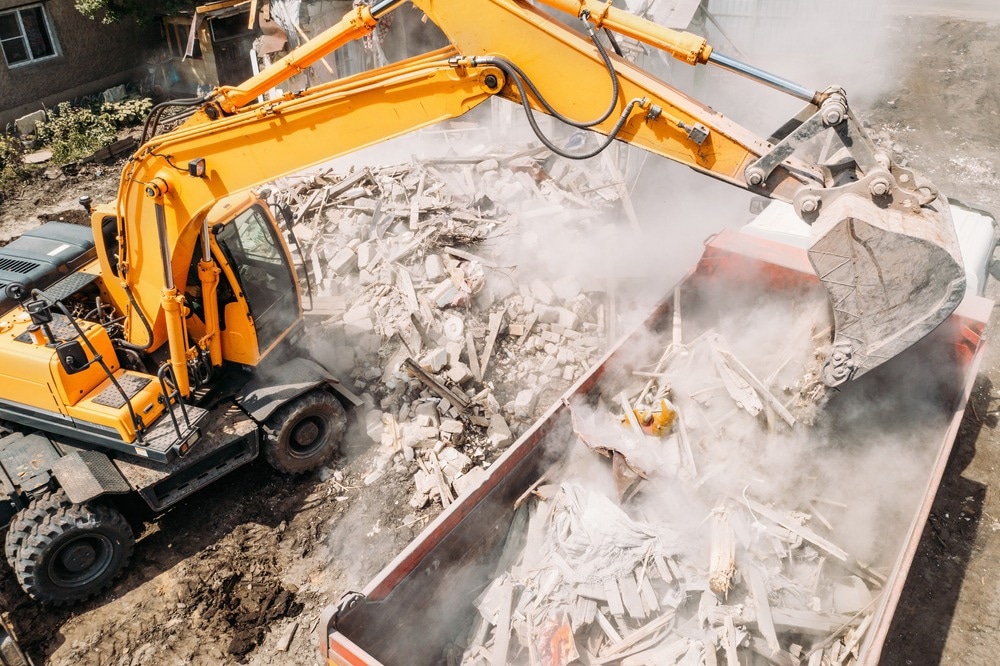
Image Credit: DedMityay/Shutterstock.com
The Origins and Evolution of Demolition Robots
The world's first demolition robot emerged in 1976 when a Swedish contractor invented a remote-controlled machine to demolish a hazardous smelting furnace interior from a safe distance. This established the basis for today's compact track-mounted demolition robots equipped with hydraulic breakers, crushers, rock drills, and grapples for versatile demolition operations.
Early demolition robots were diesel-powered, but growing emissions concerns led manufacturers like Brokk to offer electric versions. Recent models also incorporate smart technologies - automatic motor control for optimized demolition performance, power regulation for generator use, and robust components for easier maintenance.
Complementing demolition robots, hydro demolition techniques using high-pressure water jets controlled by automated robots also emerged in the 1980s for precise, vibration-free removal of deteriorating concrete. Modern hydro demolition robots integrate positioning systems to execute complex geometric cutting patterns accurately according to digital plans.
How Are Demolition Robotics Transforming the Construction Industry?
Unparalleled Safety
By enabling remote operation at safe distances from collapsing structures and flying debris, demolition robots eliminate worker exposure to intrinsic demolition hazards. Continual monitoring through the operator camera enhances oversight compared to restricted on-site vision. This prevents injuries or even fatalities.
ADEP Group, a demolition and remediation contractor, tackled the challenge of removing a concrete pool from a 120-year-old YMCA facility in Beverly, Massachusetts. Faced with hazardous materials in historic structures, traditional methods were impractical due to limited access, floor load restrictions, and COVID-19 safety measures.
ADEP opted for the Brokk 200 robotic demolition solution, offering a compact size and powerful performance. This choice ensured the safe and efficient demolition of a 36-inch-thick concrete pool within just eight days, achieving a 25% cost reduction and saving 456 hours of labor.
Maximized Productivity
Demolition robots guarantee unparalleled productivity, surpassing human labor with continuously optimized demolition and specialized attachments for diverse tasks. They work tirelessly without breaks, equivalent to the output of multiple manual operators. For instance, traditional wall sawing for tasks like removing a 10-by-3-m wall demands extensive time and labor, taking up to four days with a crew of three. In contrast, demolition robots halve the time needed for such tasks, ensuring maximum productivity.
In a time-sensitive scenario, EnviroVantage successfully met the challenge of efficiently demolishing the reinforced announcer's box for handicap seating using the Brokk 100 remote-controlled demolition machine at the University of New Hampshire's Wildcats Stadium. Despite a shift in plans and a month lost in the schedule, the Brokk 100 demonstrated superior productivity, removing 105.8 cubic yards of concrete and rebar in just 72 person days.
Enhanced Precision and Control
Robotic demolition technology ensures precise and forceful material breakdown, safeguarding underlying assets, particularly critical structural components. Adjustable pneumatic breaker power regulation minimizes vibrations, preserves foundations, and enhances sustainability through improved material separation for increased recycling/reuse rates.
Hydro demolition robots excel in precision with programmable cutting for geometric shapes, surpassing remote-controlled machines. Operating at pressures up to 40,000 psi, they prevent microcracks and rebar damage, maintaining asset integrity.
Advanced models like the Aqua Cutter 410V use GPS and a multiaxis 3D positioning system to efficiently access challenging areas, highlighting the technological advancements in next-generation demolition robots.
In a San Antonio project addressing I-35 congestion, JR Ramon, a demolition constructor, initially used an excavator, leading to significant rebar damage and a $100,000 setback. Recognizing the need for enhanced efficiency and precision, JR Ramon turned to Brokk's remote-controlled demolition robots. The Brokk 120D doubled the efficiency in demolishing inner bridge sections, and its precise operation spared the underlying rebar, preventing costly damage and delays.
Overcoming Adoption Barriers Through Proven Return on Investment
While demolition robots demonstrate immense productivity and safety and control advantages, high initial investments ranging from $100,000 hinder widespread adoption, especially among smaller contractors lacking adequate financial capacity.
However, extensive proof of concept from early adopters highlights the rapid return on investment (ROI) realization and greater profit opportunities that justify the capital expenditure, e.g., Brokk demolition robots commonly achieve full cost recovery within 12-18 months.
In addition, reduced manual labor and project duration contribute to immense savings, while increased demolition project capacity enables additional revenues exceeding machine rental costs.
Duke Long, president and founder of Interstate Sawing & Demolition, highlights that the safety benefits of demolition robots are reflected in metrics like the experience modifier rate (EMR), where the trend is downward, resulting in lower insurance premiums and increased competitiveness in project bidding.
Large contractors like Veit & Company emphasize demolition robots as pivotal sales differentiators across diverse commercial, industrial and infrastructure demolition projects nationwide, encouraging competitor adoption. Successful deployment by Veit on intricate overpass repair jobs has reduced labor requirements by up to 90% while adhering to strict deadlines.
As major industry players lead transformative demolition processes through progressive technology integration, smaller contractors must emulate such investments to remain competitive.
Future Outlook - An Autonomous Demolition Future
Demolition robots have already prevented thousands of lost time injuries annually across the industry. As the technology life cycle matures, many envision an autonomous demolition future - teams of interactive robots efficiently coordinating to rapidly deconstruct buildings with minimal planning. At the same time, remote human oversight ensures quality assurance and interfaces with supplementary trades.
For construction companies, embracing progressive demolition automation serves a dual purpose - resolving intensifying skilled labor shortages while achieving higher margins through expanded project capacity. Such outcomes accelerate further technological innovation and adoption in a virtuous cycle, thereby driving the evolution of autonomous demolition.
While full autonomy remains an aspirational vision, the current capabilities of demolition robots are undeniably profound, indicating an inevitable and widespread proliferation.
References and Further Reading
Bigwood, P. (2018). Remote-Controlled Asphalt and Concrete Demolition. Available at: https://www.concreteconstruction.net/projects/infrastructure/remote-controlled-asphalt-and-concrete-demolition_o
Cottom, T. (2019). Robot invasion: Why remote-controlled machines are the future of demolition. Available at: https://www.cdrecycler.com/news/remote-controlled-demolition-robot/
Keeling, J. (2023). 3 Ways Demolition Robots Increase Efficiency in Concrete Cutting Applications. Available at: https://www.forconstructionpros.com/concrete/equipment-products/article/22861630/brokk-inc-3-ways-demolition-robots-increase-efficiency-in-concrete-cutting-applications
Brokk. (2021). New England Contractor Sees New Opportunities with Remote-Controlled Demolition. Available at: https://www.brokk.com/us/news/brokk-articles/next-gen-demolition/
Boerner, A. (2017). Brokk Demolition Robot Succeeds in Concrete Demolition After Other Methods Fail. Available at: https://www.forconstructionpros.com/equipment/article/20976349/brokk-demolition-robot-succeeds-in-concrete-demolition-after-other-methods-fail
Brokk. (2017). Precise Productivity: Contractor Cuts Labor Costs By 90% On Bridge Project. Available at: https://www.brokk.com/us/news/brokk-articles/precise-productivity-contractor-cuts-labor-costs-by-90-on-bridge-project/
Disclaimer: The views expressed here are those of the author expressed in their private capacity and do not necessarily represent the views of AZoM.com Limited T/A AZoNetwork the owner and operator of this website. This disclaimer forms part of the Terms and conditions of use of this website.