Festo’s Scharnhausen Technology Plant in the high-tech country that is Germany is at the forefront of automation for the future.
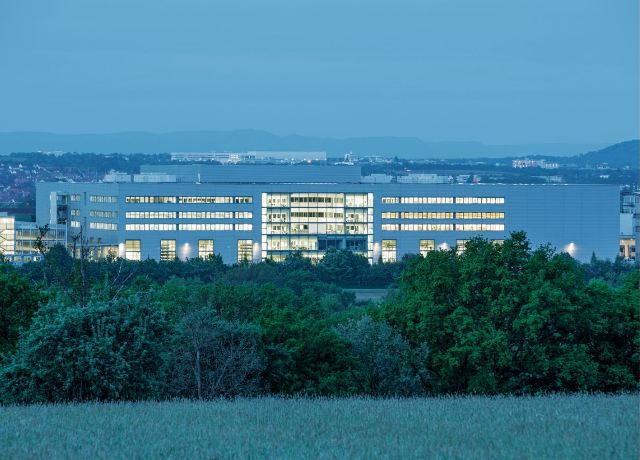
Festo’s Scharnhausen Technology Plant in the high-tech country that is Germany is at the forefront of automation for the future. The factory, where the automation company manufactures valves, valve terminals and electronics, is characterised by lean and energy-efficient processes, top-quality products and a pronounced customer focus, as well as sustainable and green production.
Crucial for the whole concept was the high level of adaptability of the production location, which makes it fit for the future. “A central objective of Industry 4.0 is the completely networked factory. Here at the Technology Plant, we are continually working towards achieving this, but we should stress that we are talking about an evolutionary process,” said Dr Eberhard Veit, Chairman of the Management Board of Festo AG & Co. KG. “The knowledge gained from our research into Industry 4.0 is also channelled into the further development of the plant.”
Industry 4.0 is becoming a reality
Many of the aspects and requirements of Industry 4.0 are already a reality in the Scharnhausen Technology Plant. For example, every day employees work with a flexible robot in a direct and totally safe interaction. It acts as an assistant to people and relieves them of ergonomically one-sided tasks. A holistic energy transparency system is currently being set up and, in future, will provide transparency with regard to energy flow and energy consumption in the Technology Plant. It will do so by taking a systematic look at the interaction between the consumer units in the production department and in the building. Modern information technology is being consistently applied in the Technology Plant. These days, the tablet is therefore the principal tool for service engineers when it comes to quickly detecting machinery faults or processing orders on-site without delay.
A focus on qualification
For Festo, however, Industry 4.0 not only means developing new technologies, but also putting people at the focus of production of the future and preparing them for new tasks through training and qualification. „Our employees are motivated for, aware of and able to get the right qualifications on an ongoing basis to face up to the challenges of the future – they are ready for the production of tomorrow”, says Dr Veit. The Learning Factory integrated in the plant also contributes to this by helping employees gain qualifications and providing them with practical and needs-oriented training.
Efficient value chains
When it came to planning the new plant, experts from purchasing, development, IT, logistics, production and human resources immediately got together and worked in an interdepartmental manner. In this way, it was possible to come up with intricate plant architecture and turn this into a reality in three short years. According to plant manager Stefan Schwerdtle, a dynamic adaptation in line with future requirements is one part of the concept. „The development process is by no means complete when the plant opens. We are faced with new challenges in the global competitive arena that is the automation sector with employees who are ready to learn and are open to the changes in the area of production. This is how we are able to implement even complex changes in a sustainable manner.”
Production site that sets an example
Besides high-performance and competitive production, the new plant also sets an example: it is used by Festo as a reference factory for its customers to demonstrate the latest automation technology and an optimal material flow and well-oiled value chain. „Our innovative strength comes to the fore in the Technology Plant. We have created the space necessary for cooperative technology and product developments there, and also considerably improved the time to market through optimised procedures and realigned core processes”, says Dr Veit. „We can therefore prove to customers and partner companies alike that here in Germany, we also produce to excellent standards and can create attractive and modern workplaces.”
Business location par excellence
Right from the start, the town of Ostfildern also adopted a positive outlook for the project. „The expansion has turned it into one of the most innovative companies in Ostfildern and the biggest employer in the town”, said Mayor Christof Bolay. He believes that, by expanding its production and development facilities in Scharnhausen, Festo has made a clear commitment to the location. The image of the town, located in the business region of Baden-Württemberg, has therefore been significantly enhanced. Once again, Ostfildern proves itself to be an attractive location for successful companies.
The Technology Plant in figures
The Scharnhausen Technology Plant is Festo’s main plant for the production of valves, valve terminals and electronics, and at the same time acts as a reference factory for customers. The plant occupies a total area of 66,000 square metres and employs 1,200 people. Festo has invested a total of 70 million euros in the expansion of the site.