Sep 11 2013
As raw materials and other resources become scarcer and plants look for new ways to be more efficient with energy use and operations, Metso is developing its offering in intelligent processes and service solutions to help customers meet these challenges.
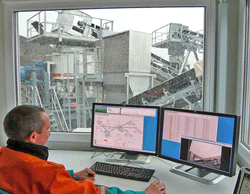
In minerals processing and aggregate production, today’s top drivers are safety, productivity and cost efficiency. Automation and intelligent solutions enable plants to improve both their financial and environmental performance. Metso provides these industries with a unique combination of in-house expertise on processes, plant-wide automation and energy-efficient equipment and processes. Recently, Metso DNA systems have been ordered, for example, from SSGPO in Kazakhstan, Codelco El Teniente in Chile and Norilsk Nickel Kolskaya GMK in Russia.
“In hard economic times when plants have no extra money for new machine investments, they can get more out of their existing equipment and processes through automation and intelligent solutions. Productivity and cost efficiency can be improved by optimizing process performance and minimizing lost time,” says Kari Heikkilä, Director, Minerals Processing Systems, Automation, Metso.
According to Heikkilä, Metso is currently developing solutions that will embed automation even further within the machines, enabling them to intelligently communicate with each other. Active R&D within Metso and collaboration with recognized research institutes keeps the company at the forefront of technology.
Better availability and productivity
By enabling better process control and visibility, an advanced automation system keeps processes running smoothly. Accurate online measurement information and diagnostics show how the machines and the plant are working; a single piece of data can make or break the process. For example, condition monitoring solutions installed on large machines enable preventive maintenance and help avoid costly unplanned downtime, resulting in better machine reliability and availability.
“You have to measure a process in order to control it. Plant stability is the key to good overall capacity, high-quality end products and safe operation,” Heikkilä continues.
Declining ore grades and complex ores with more impurities mean getting more out of less and cause headaches in minerals processing. Minerals recovery can be optimized and production boosted through seamless integration between Metso’s systems, online data, equipment, services and innovations. It also enables the reduction of energy and water consumption, resulting not only in cost efficiency but also in a lower environmental impact.
Towards zero accidents
Safety is a high priority, and having zero accidents is every plant’s goal. Automation removes operators from the vicinity of the machines to the safe control room environment. The level of safety is increased through better information distribution.
“Automation also helps with the shortage of skilled mining employees. As plants are often far from urban areas, recruiting staff can be difficult,” Heikkilä points out. “Automation reduces the need for experts, thus lowering costs. Remotely operated machinery can be run from a faraway location. And Metso’s remote support can be reached 24/7.”
References around the world
Metso’s flagship system for minerals processing and aggregate production is Metso DNA. It is a scalable system that can be expanded step by step from one subprocess to another to build a complete plant-wide system including advanced process controls, analyzers and information management. It can also be integrated flexibly with other suppliers’ systems. The system is complemented by a wide technology and service offering.
“Over the years, we have delivered systems to mining customers, for example, in Scandinavia, Europe, Russia, Brazil and Chile,” Heikkilä lists. Project deliveries are always secured with Metso’s local customer service that focuses on life-cycle support. The role of service and performance agreements is constantly growing.
One of Metso’s longest-standing mining customers is Yara Siilinjärvi, located close to Kuopio, Finland. It is the only phosphate mine in Western Europe and has boosted its productivity with the Metso DNA automation system since 1979. Cooperation between the two companies for more than 30 years has ensured reliable, high-quality production at the plant. With accurate measurements and analyses, the plant has been able to optimize both the process and use of raw materials, thus preventing any overuse of expensive materials. Being able to control the entire production chain has increased control accuracy and improved both the quantity and quality of the plant.