In the future, soft robots will be able to undertake activities that cannot be done by conventional robots. These soft robots could be deployed in hard-to-reach areas and in situations where they are exposed to radiation or chemicals that would be harmful to metal-based electronically controlled robots.
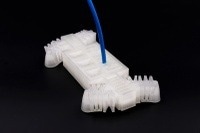
The modules make it possible for the first time to produce flexible and electronics-free soft robots entirely in a 3D printer using filament made from conventional printing material. Image Credit: Lucia Brunold
This necessitates that these soft robots be controlled without the need for electronics, which is currently a difficult development task. Recently, a University of Freiburg research team has created 3D printed pneumatic logic modules that use air pressure alone to control the movements of soft robots. These modules mimic electrical control by allowing the air flow to be switched logically.
For the first time, the modules enable the complete production of soft robots that are flexible and devoid of electronics within a 3D printer using standard filament printing material.
The team led by Dr. Stefan Conrad, Dr. Falk Tauber, Joscha Teichmann, and Professor Dr. Thomas Speck from the Cluster of Excellence has published its results in the renowned journal Science Robotics.
Our design makes it possible for anyone with 3D printing experience to produce such logic modules and use them to control a soft robot without the need for high-end printing equipment, and this marks a significant step towards completely electronics-free pneumatic control circuits that can replace increasingly complex electrical components in soft robots in the future.
Dr. Stefan Conrad, livMatS Cluster of Excellence, University of Freiburg
Modules Can Perform Boolean Operations and Direct Airflow into Movement Elements in a Targeted Manner
There are two pressurized chambers in each module. Between these chambers is a 3D-printed canal. The expanding chambers can control the air flow in the channel like a valve by compressing the channel and stopping it. The modules can direct the air flow into the soft robot's movement components while carrying out Boolean logic operations "AND," "OR," and "NOT" in a manner akin to electrical circuits by precisely opening and closing the valve.
The chambers into which air pressure is supplied dictate the function each particular module does. The modules can function at pressures ranging from 80 to over 750 kilopascals, depending on the material chosen. They react quickly in contrast to other pneumatic systems around 100 ms
Wide Range of Applications
The potential applications of these modules are enormous. We have developed a flexible 3D-printed robotic walker that is controlled by an integrated circuit using air pressure. The flexibility of the logic modules is demonstrated by the fact that this walker can even withstand the load of a car driving over it, as an example of more complex control systems, we have also developed an electronics-free drinks dispenser.
Dr. Falk Tauber, Project Leader, livMatS Cluster of Excellence, University of Freiburg
Journal Reference
Conrad, S., et.al., (2024). 3D-printed digital pneumatic logic for the control of soft robotic actuators. Science Robotics. doi.org/10.1126/scirobotics.adh4060.