Reviewed by Mila PereraOct 25 2022
For several years, scientists have attempted to build robotic hands that possess similar dexterity to human hands in how they can hold and control objects. However, these robotic hands could not endure the physical collisions that can occur in unstructured settings.
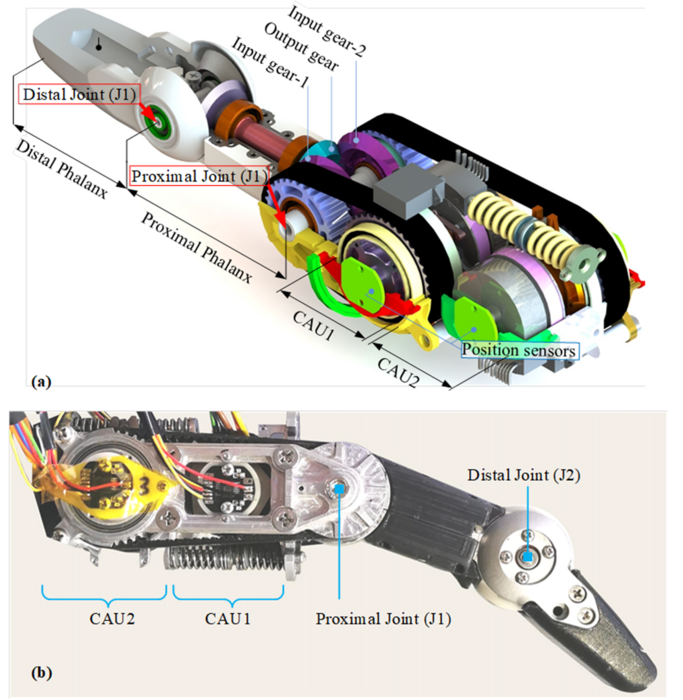
A sectional view of the CAD model of the finger (top) and the prototype antagonistic variable stiffness finger mechanism (bottom). Image Credit: Higher Education Press Limited Company
Researchers have now built a small robotic finger for dexterous hands, which can endure physical impacts in its work setting.
The research group from Harbin University of Technology (China) discussed their work in an article published in the October 14th, 2022, issue of the journal Frontiers of Mechanical Engineering.
Robots regularly work in settings that are volatile and occasionally unsafe. Physical collisions cannot be avoided when multi-fingered robotic hands are essential to work in unstructured surroundings, such as settings where objects move rapidly, or the robot must work alongside humans or other robots.
The energy produced by these impacts can deform the hardware units of the robotic hands. The existing dexterous hands are stiff and thus can be easily deformed by physical collisions or impacts. Robots fitted with robust, dexterous hands that can endure physical impacts are, therefore, required.
The researchers aimed to develop a robotic finger that could imitate the human finger in dexterity and ability to absorb and endure physical collisions.
This will enable the dexterous hand to have better mechanical robustness, thus solving the problem that the rigid driven dexterous hand is easily damaged by physical collisions in unstructured environments.
Yiwei Liu, Professor, Harbin Institute of Technology
Current technology concerning robotic hands uses a variable stiffness actuator device. These devices are engineered to make the robotic hand’s dexterous features possible. In the human body, the natural stiffness and flexibility of the muscles vary based on the job at hand.
The variable stiffness actuators deliver human-like flexibility and stiffness modification to the robotic hand based on the required task.
The variable stiffness actuator is stimulated by two actuators. This means that the robotic hand system must comprise two sets of actuation devices, decelerators, and sensors.
Since the variable stiffness actuator’s complexity, weight and volume are all increased, it is not an appropriate solution for creating a compact, dexterous hand.
To overcome these challenges, the researchers created an antagonistic variable stiffness finger mechanism. This finger is based on gear transmission that is likely to be more dependable and easier to build and maintain than the existing cable-powered dexterous hands.
The mechanically robust finger is based on the concept of mechanical passive compliance, where the contact forces between a stiff environment and a robotic manipulator are regulated. The mechanical finger can absorb physical impacts while also modifying its stiffness, depending on the needs of the task it is executing.
The benefit of this finger mechanism is that it offers an adjustable stiffness function and small structure without the complexity and weight of extra actuators.
The finger prototype created by the team weighs 480 g and is made using 3D-printed material and alloy material. The researchers conducted a series of grasping and manipulation tests on the finger. They used a range of standard objects - rectangular objects, cylindrical objects, and spherical objects - of various sizes to test the grasping capability of the finger.
Their finger mechanism is strong for enduring physical impacts while also functioning well for grasping, power, and manipulation.
In the future, the researchers plan to enhance the stiffness adjustment range of the finger while simultaneously working to make it smaller in size and weight. The eventual goal is the design and construction of a completely dexterous hand.
This research is of great importance to improving the manipulation level of dexterous hands in unstructured environments or physical interacting tasks.
Yiwei Liu, Professor, Harbin Institute of Technology
The research team includes Handong Hu, Zongwu Xie, Yiwei Liu, Hong Liu, and Jianfeng Yao, who work in the State Key Laboratory of Robotics and System, Harbin Institute of Technology, China.
The National Key R&D Program of China and the Major Research Plan of the National Natural Science Foundation of China funded this research.
Journal Reference
Hu, H., et al. (2022) Mechanical design, modeling, and identification for a novel antagonistic variable stiffness dexterous finger. Frontiers of Mechanical Engineering. doi.org/10.1007/s11465-022-0691-5.