In the world of robotics, researchers and engineers are always looking towards innovation and a novel fabrication technique has allowed researchers at the Massachusetts Institute of technology to produce power-dense, low-voltage, artificial muscles that enhance the agility and performance of flying microrobots.
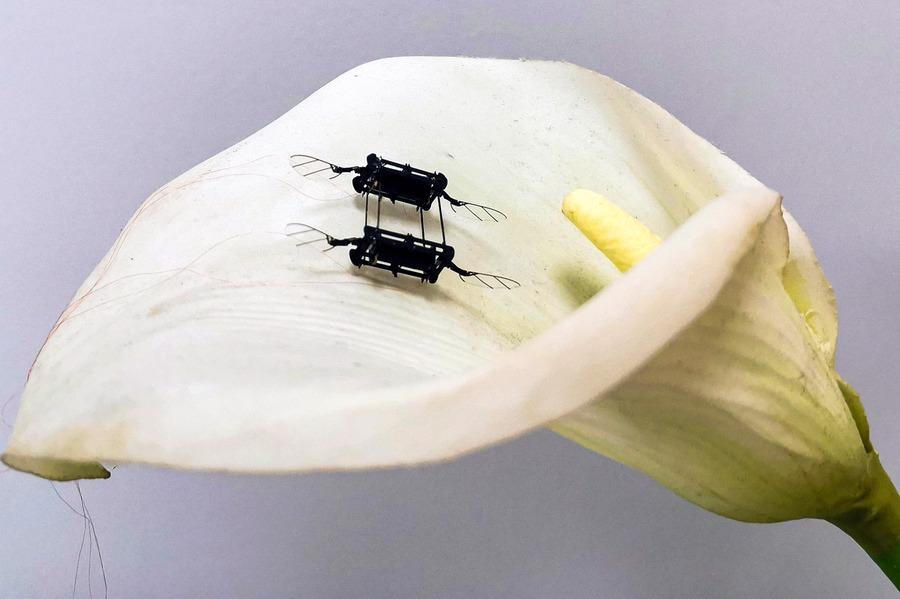
Image Credit: Zewe, A., (2022) Giving bug-like bots a boost. [online] MIT News | Massachusetts Institute of Technology. Available at: https://news.mit.edu/2021/micro-robots-artificial-muscles-1216
The novel technique facilitates the fabrication of soft actuators with 75 percent less voltage power than present-day versions while being able to carry 80 percent more payload. Such soft actuators rapidly flap miniature wings on the robots. This gives them bug-like maneuverability, meaning they could potentially navigate complex, cluttered spaces.
The soft actuators are made up of 20 layers 10-micrometers in thickness (roughly the diameter of a red blood cell). The robot itself has four sets of wings, each of which are set in a rectangular configuration and powered by a soft muscle-like actuator, respectively.
The muscle-like actuators are comprised of layers of elastomer that are fastened between two extremely narrow electrodes and then turned into a soft cylinder. The electrodes squeeze the squishy elastomer cylinder when voltage is applied to the actuator, and the mechanical strain causes the wings to flap.
Overcoming Challenges
The greater the surface area of the actuator, the less voltage required. Thus, the researchers set about creating as many layers as possible by reinventing fabrication techniques. However, during one of the phases – when the elastomer was spin-coated using centrifugal force to make it thinner – microscopic air bubbles appeared in the elastomer.
The thinner the elastomer is spun, the greater the number of air bubbles which has previously held back researchers. However, by introducing a vacuuming process directly following spin coating, the air bubbles can be removed while the elastomer is still wet. This process eliminates defects and improves the power output of the actuator by more than 300 percent, and prolongs the lifespan.
In addition to the development of the novel soft actuators, the researchers were also able to optimize the number of electrodes used in the aerial microrobots. Made of carbon nanotubes, these electrodes are about 1/50,000 the diameter of a human hair, but as they are sharp, they can pierce and rip the elastomer resulting in more defects in the robots.
Furthermore, another challenge the researchers needed to overcome was the curing phase, as they discovered that the more layers added, the longer the actuator took to dry. Previously, it could take up to 48 hours for the layers to dry as they hit double-figures, which is not a sustainable or practical fabrication method.
By baking each layer for a few minutes immediately after the carbon nanotubes are transferred into the elastomer significantly reduces the curing time as the actuator’s layers are built up.
After overcoming challenges and advancing their fabrication method to create the 20-layer artificial muscle, the researchers tested their microrobot’s actuator against a previous 6-layer version, as well as other rigid actuators.
Future Application Potential
During the tests, the MIT team noticed their aerial microrobot required fewer than 500 volts to function with a lift to weight ratio of 3.7 to 1, meaning it can carry almost three times its own weight.
Furthermore, when the 20-layer actuator microrobot hovered, it was more stable than the others and held a flight time of 20 seconds which is the lengthiest ever documented for a sub-gram robot of its kind. After 2 million cycles, the 20-layer actuator was still operating well, exceeding the lifespan of previous systems.
The MIT researchers are extremely happy with the results of their recent work, and while they are breaking new ground with their 10-micrometer actuator layers, the goal is to eventually produce soft actuator layers only 1-micrometer thick which would revolutionize the application potential of aerial microrobots if successful.
To take the next steps, the team will move fabrication methods into a clean room to eliminate dust and other environmental factors that limit spin-coating techniques. Although the team may still need to spend some more time producing scalable untethered aerial microrobots, their recent breakthrough does boost the application potential.
While conventional larger drones require plenty of outdoor space to navigate, aerial microrobots could be used in enclosed spaces or in complex and intricate scenarios, such as search and rescue missions and the pollination of crops, and even used to navigate complex machinery such as checking on the turbine blades on a turbine engine.
Reference and Further Reading
Zewe, A., (2022) Giving bug-like bots a boost. [online] MIT News | Massachusetts Institute of Technology. Available at: https://news.mit.edu/2021/micro-robots-artificial-muscles-1216
Ren, Z. and Kim, S., et. al. (2022) A High‐Lift Micro‐Aerial‐Robot Powered by Low‐Voltage and Long‐Endurance Dielectric Elastomer Actuators. Advanced Materials, [online] p.2106757. Available at: https://onlinelibrary.wiley.com/doi/full/10.1002/adma.202106757
Disclaimer: The views expressed here are those of the author expressed in their private capacity and do not necessarily represent the views of AZoM.com Limited T/A AZoNetwork the owner and operator of this website. This disclaimer forms part of the Terms and conditions of use of this website.