Jun 27 2019
Soft robots cannot compete with the hard at all times. Their stiff counterparts rule assembly lines, dive, perform backflips, fly, dance to Bruno Mars' "Uptown Funk," and walk through volcanoes.
A soft mechanotherapy device for the lower leg sequentially contracts around a human user's leg, "pumping" fluid up. The device could be used to treat conditions like lymphedema and chronic venous disease and to prevent deep vein thrombosis. (Image credit: Daniel Preston, Harvard University)
But every year, soft robots attain new abilities. They have learned to jump, grip, and squirm. Plus, in comparison to hard robots, they can grip tomatoes without hurting the fruit, resurface unharmed after being hit by a car, and travel through radiation, disaster zones, and outer-space with few scratches. For animals and people, they possess a "cooperative function": a soft touch.
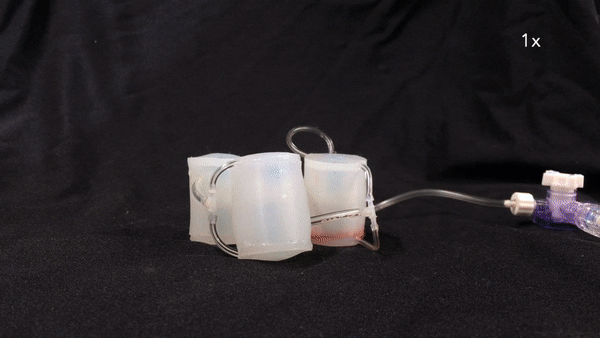
Soft inverters can bounce right back after heavy strain. (Video Credit: D.J. Preston, H.J. Jiang, V. Sanchez, P. Rothemund, J. Rawson, M.P. Nemitz, W.K. Lee, Z. Suo, C.J. Walsh, and G.M. Whitesides)
In recent times, scientists in the lab of George M. Whitesides, the Woodford L. and Ann A. Flowers University Professor, have developed soft replacements for the last hard parts essential to construct a robot. In the place of electricity and wires, pressurized air expands and contracts rubber inflatables to produce movement, soft valves replace the hard, and soft digital logic reproduces the same abilities of an electronic computer.
Now, postdoctoral scholar Daniel J. Preston's newest soft invention offers these robots new, multifaceted movements. As a study’s first author, published in Science Robotics, he demonstrates the first soft ring oscillator, which offers soft robots the ability to roll, sort, meter liquids, undulate, and swallow.
"It's another tool in the toolkit to make these smart, soft robots without any electronics, and without any hard valves," Preston says.
Thus far, ring oscillators were built with microfluidics or electronic transistors. Electronics always require hard parts. The majority of microfluidics require that as well. Glass is used in many for their pressurized water or air systems, and many need thin channels that can only manage very low flow rates, restricting operation speeds. Miniature microfluidic systems might attain higher frequencies than Preston's macroscale pneumatic ring oscillator, but his team already has blueprints to modify their soft system to realize greater speeds, if necessary.
The soft ring oscillator — similar to all ring oscillators — depends on inverters ("NOT" digital logic gates). Preston's inverters, for example, control the air pressure in his robot's rubber tubes: If the output is high pressure, the input will be low pressure and vice versa. When three, or any odd number, of gates are linked in a ring, one gate's shift activates the next, which activates the next, and on and on.
The cool response that you get when you combine an odd number of these inverters in a loop is an instability that travels around the loop.
Daniel J. Preston, Postdoctoral Scholar, Harvard University
Like a slinky that collapses so as to spring down a staircase, one movement triggers the next, forming a constant pace without the need for the subsequent push.
To see what the soft ring oscillator could achieve, Preston and his team designed five soft robot models. Each uses a single, continuous source of air pressure to work three pneumatic actuators (the inverters).
One prototype prods a ball around a ring. Another undulates a stage to make beads of two varying sizes roll against the edge. In due course, all the smaller beads fall via a hole in the side of the stage. They sort themselves out.
"The ring oscillator is really good for things like rolling motions," Preston says. Rolling requires coordination of a number of actions in time. A single output and input will not be enough. For example, to make their hexagonal foam robot to roll forward, the ring oscillator helps inflate a balloon behind the robot and deflate one in front at precisely the same time. The coordinated push-and-release moves the hexagon forward again and again as the balloons inflate and deflate in perfect harmony.
Still, another prototype offers a more concrete purpose. A textile-based sleeve, wrapped around the lower leg and fastened with Velcro, applies coordinated pressure, "pumping" fluid up the leg.
According to the latest studies, this "pumping" motion enhances symptoms of lymphedema and chronic venous disease better than basic compression. The device could also help nurses, police officers, and waiters to prevent deep vein thrombosis, an outcome of working long shifts on tired feet.
Before they begin clinical trials for their sleeve, the researchers want to test the level of interest. If sufficient people desire a softer, less costly way to ease and prevent symptoms, the product might probably find an adequately big market to justify additional research.
The low cost of Preston's materials — rubber-like silicone elastomers — render them suitable for more than just economical homecare. Biocompatible, disposable, sterile, and gentle varieties could be used for drug delivery, lab experiments, or even medical devices inside the body like this sleeve that helps the heart to beat. Preston's end prototype can categorize three different colored liquids based on a pre-defined sequence and time, a tool that could turn out to be beneficial for chemists.
Though all of Preston's models are developed with only soft materials, they are not yet untethered: All depend on a continuous source of pressurized air. Nevertheless, Preston and his colleagues have a few answers for this, too. For the leg sleeve, patients could supply their own air with a hand-held pump similar to those used to capture blood pressure. Furthermore, soft robots in the trenches could employ mobile carbon dioxide cartridges, attached like a backpack, or gas-generating chemical reactions to trigger the bot to move.
But Preston anticipates his new tool can realize a lot more than the applications shown using his five models. Since the paper explains how to reproduce and modify the design, he expects other labs will discover even more applications.
People can use the soft ring oscillator for a lot of different applications in soft robotics, some of which we may not have even thought of or envisioned yet.
Daniel J. Preston, Postdoctoral Scholar, Harvard University