Industrial environments can be inherently unsafe, with work-related accidents costing, on average, $41,353, with medical bills and wage and productivity losses pushing this figure even higher. Robots have improved safety and productivity somewhat, but critical challenges still exist. Here, we will discuss how position sensors integrated into robots can improve the safety of industrial operations.
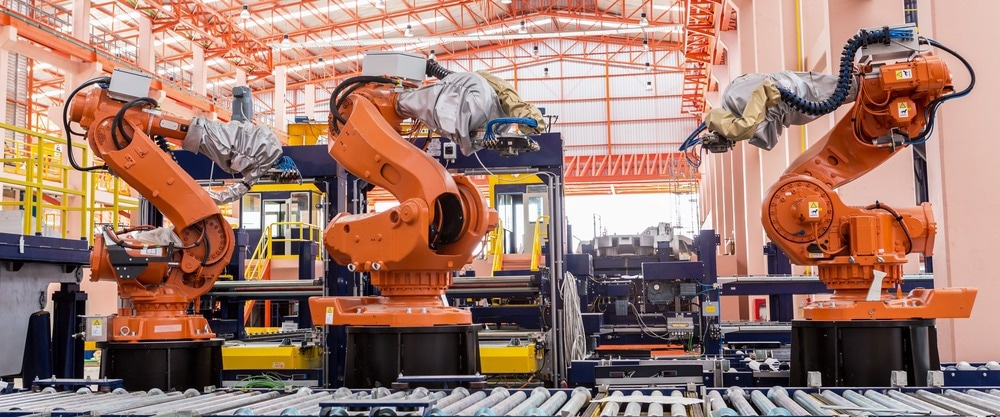
Image Credit: SasinTipchai/Shutterstock.com
What Are Position Sensors?
Position sensors are commonly used components in many industries. An object’s motion or relative position to an established reference point can be determined accurately by a position sensor. Additionally, position sensors can detect the presence or absence of another object and its relative position and direction of motion compared to the object the sensor is installed in.
Position sensors perform similar functions to motion sensors and proximity sensors. Motion sensors trigger an action, such as activating a camera when an object is detected, and proximity sensors can detect an object that has entered its range. Both of these can be regarded as specialized position sensors.
Position sensors differ from both these types of sensors in that they not only detect an object but also record its position via feedback signals containing the object’s positional information. Types of position sensors include potentiometric sensors, inductive sensors, ultrasonic sensors, optical sensors, eddy-current based sensors, and fiber-optic based sensors.
How Can Position Sensors Aid the Safety of Industrial Robots?
Over the past few decades, workplaces have undergone a profound change, with many tasks traditionally carried out by human workers now being performed by robots. However, while this has reduced the need for human workers in unsafe environments, accidents still occur.
In 2022, according to the U.S. Bureau of Labor Statistics, there were 5,486 workplace fatalities in the United States alone. Many of these fatalities and other incidents which cause injury and disfigurement can be avoided by the use of innovative technologies such as position sensors.
Industrial robots come in many different forms, performing a number of key tasks in the workplace. To be effective, robots must be strong, fast, accurate, and able to perform repetitive tasks. They can handle extremely heavy loads or be precise enough to manipulate fragile electronics.
Position sensors detect the relative position of human workers or other workplace assets, mitigating any hazards that may occur. This is especially useful for the emerging field of autonomous mobile robots (AMRs.)
AMRs are increasingly employed in workplaces such as distribution centers, warehouses, and factories to navigate dynamic and complex environments containing workers, other assets, and infrastructure elements. Once an object is detected, the robot will slow down, stop, or change direction to avoid a collision.
One of the central sensor technologies employed in AMRs is LiDAR (Light Detection and Ranging.) This technology utilizes lasers to determine accurate range and directional information in multiple directions by measuring the time reflected light returns to the receiver. Using this sensor technology, AMRs can build a complex 3D map of the entire dynamic environment.
LiDAR sensor-equipped AMRs remove the need for safety interlocks and fences in workplaces. This, in turn, lowers production costs and improves productivity and flexibility in industrial and commercial facilities, making the workplace a safer, more collaborative environment between humans and autonomous robots.
Other types of position sensors commonly used in industrial robots include linear position sensors, which detect the variable position, proximity, and distance of objects and angular position sensors, which detect the angle of equipment. GPS is used as a standard positioning sensor to determine the robot’s location.
AI-based technologies are also improving the capabilities of position sensors in industrial robots. By merging AI and sensor technologies, robots can learn from the realm of data available to them, facilitating better and safer performance and innovative Industry 4.0 technologies such as the Internet of Robotic Things (IoRT.)
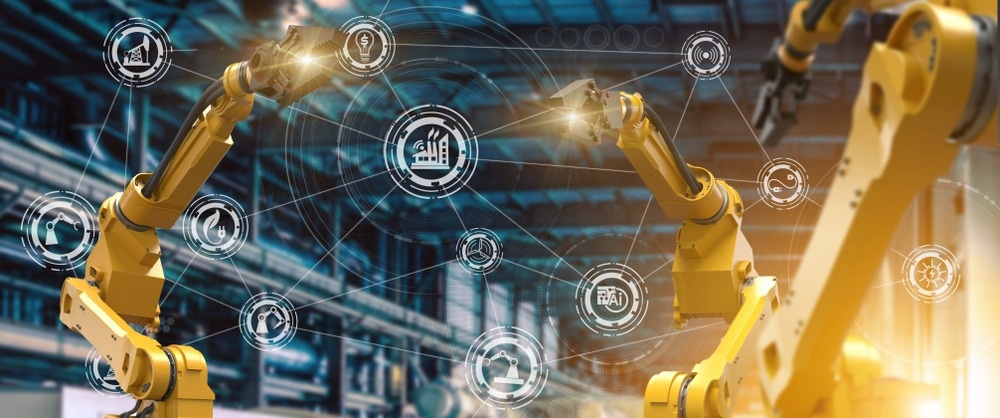
Image Credit: Pand P Studio/Shutterstock.com
Commercial Examples of Position Sensors
According to Mordor Intelligence, the global position sensor market is predicted to reach USD 18.02 billion by 2028. Between 2023 and 2028, the market is expected to experience a CAGR of 10.5%.
There are a number of companies that supply position sensors and sensor-enabled robots for the industrial sector. These include Honeywell International Inc., Balluff Inc., Baumer, Novotechnik, Hamamatsu, and KUKA.
KUKA’s range of autonomous robotic platforms leverages position and proximity sensor technologies to provide safe, omnidirectional travel around complex and dynamic work environments. With unrestricted and flexible mobility, this technology can be employed for various payloads and out-of-the-box applications in multiple industries.
KUKA’s mobile robots use algorithms and sensor data to plan routes, take on payloads, and position themselves within their environment. Laser scanners are employed to navigate autonomously without the need for artificial markings, and the system can adapt to changes in the robot’s surroundings.
Hamamatsu is another company working in this space to improve the safety of Industry 4.0 workplaces. The company provides a range of position sensors utilizing approaches and technologies such as time-of-flight methods, near-infrared (NIR,) advanced imaging, LiDAR, and optoelectronics.
SICK AG is a supplier of sensor-based solutions for the robotics industry and applications in multiple commercial sectors. The company offers modular and tailored solutions leveraging technologies such as LiDAR, RFID, and ultrasound-enabled sensors. AI-enabled functionality allows for a wealth of data collection and machine learning capabilities.
In Summary
Sensors are a central technology in robotics and associated Industry 4.0 technologies, improving the safety, efficiency, and productivity of industrial and commercial facilities.
The key to improving workplace safety is the integration of proximity and position sensors that leverage technologies such as LiDAR, GPS, RFID, ultrasound, NIR, machine vision, and AI.
With workplaces becoming more automated, the challenges of ensuring safety when humans and robots work cooperatively are increasing, requiring innovative technologies to overcome them. The position sensor and robotics markets are well-placed and served by several companies to meet these challenges.
References and Further Reading
KUKA.NavigationSolution [online] kuka.com. Available at: https://www.kuka.com/en-us/products/amr-autonomous-mobile-robotics/navigation-solution
Hokuyo (2023) How Sensors Work in Industrial Robotics to Mitigate Hazards and Risks [online] hokuyo-usa.com. Available at: https://hokuyo-usa.com/resources/blog/how-sensors-work-industrial-robotics-mitigate-hazards-and-risks
SICK Sensor Intelligence (website) Sensor solutions for all variants of mobile robots [online] sick.com. Available at: https://www.sick.com/gb/en/sensor-solutions-for-mobile-robots/w/mobile-robots/
Edwards, E. (2024) All About Position Sensors [online] thomasnet.com. Available at: https://www.thomasnet.com/articles/instruments-controls/all-about-position-sensors/
Disclaimer: The views expressed here are those of the author expressed in their private capacity and do not necessarily represent the views of AZoM.com Limited T/A AZoNetwork the owner and operator of this website. This disclaimer forms part of the Terms and conditions of use of this website.