Soft robots are gaining widespread adoption due to their high flexibility and versatility, but their fabrication using traditional methods remains challenging and highly time-intensive. Recent progress in 3D printing and soft materials has enabled direct one-step manufacturing of intricate soft robots.
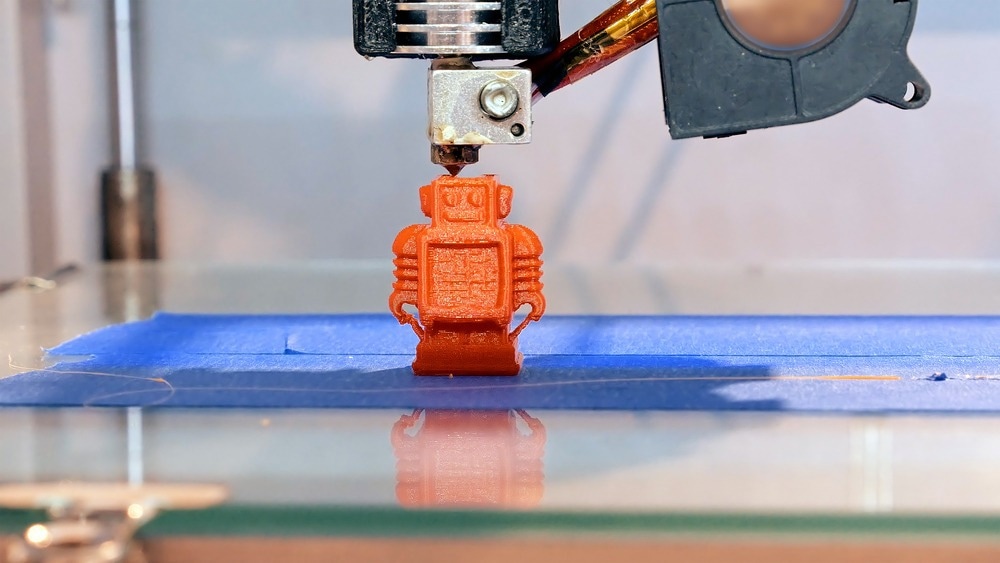
Image Credit: V/Shutterstock.com
Soft robots comprise flexible, soft materials like elastomers or gels for the robotic structures and integrated fluidic actuators to induce motions.
Traditional robots excel at well-defined, repetitive factory operations but struggle with variability beyond strict constraints. In contrast, soft robots' compliance allows seamless adaptation to unpredictable conditions, overcoming obstacles in dynamic environments.
The inherent soft elasticity and continuously deforming nature of such soft-bodied robots allow them to handle fragile objects gently, traverse confined spaces, and physically interact safely with humans, avoiding risks of damage from collisions.
In the medical field, soft robots excel in surgery and assistive tasks by conforming to the human body and facilitating physical rehabilitation by mimicking natural movements to restore motor functions. Other promising applications include disaster relief and space exploration operations involving navigation through unstructured environments and cluttered debris to search for survivors.
Traditional Manufacturing Challenges
Fabricating soft robots has relied on complex multi-step processes that severely hamper widespread development and adoption.
The common approach involves separately manufacturing the individual components using conventional techniques like molding and casting, followed by intensive manual assembly to construct the final soft robotic system.
This tedious, time-consuming and labor-intensive process limits designs predominantly to assembling stacks of basic 2D shapes that can be feasibly molded and cast.
How has 3D Printing Evolved Soft Robotics?
In recent years, there has been a significant trend towards employing 3D printing technology to fabricate soft robots for diverse applications. This approach provides designers enhanced freedom and streamlines the implementation of key soft robotic design principles, such as the separation of control and power actuators. Additionally, it facilitates the precise fabrication of mechanically intricate designs.
Initially, 3D printing in soft robotics involved creating molds for casting flexible elastomers, allowing customization but requiring manual post-processing. Further advancements enabled separate 3D printing of flexible components or embedding functional elements within soft robots, which still needed to be assembled manually to create a functional robot.
For example, Zhang et al. used a polyjet printer to create soft robots with shape memory polymers, involving an assembly process after printing.
However, current state-of-the-art technologies have fully integrated 3D printing to achieve one-step direct digital fabrication of functional soft robots with minimal manual intervention. This leverages the geometric design freedoms facilitated by various printing approaches to produce intricate flexible 3D architectures, embed internal features like pneumatic microchannels, and integrate multiple materials handling different functionalities into standalone structures.
The availability of elastomeric, gel-based and thermoplastic 3D printing materials greatly diversifies usable materials for soft robotics beyond previously dominant silicone rubbers. The rapid digital fabrication approach also permits quick design iterations and adjustments and enables cost-effective customization of soft robots tailored for specific manipulation tasks.
Recent Developments and Case Studies
3D Printing a Human-Like Hand Using Slow-Curing Polymers
ETH Zurich researchers and a US start-up developed a new 3D printing technology that uses slow-curing plastics for fabricating highly durable, elastic, and robust soft robots in one print.
Using slow-curing thiol-ene polymers, the researchers successfully printed a robotic hand with bones, ligaments, and tendons, showcasing the benefits of enhanced elastic properties and faster return to the original state.
"Robots made of soft materials, such as the hand we developed, have advantages over conventional robots made of metal. Because they're soft, there is less risk of injury when they work with humans, and they are better suited to handling fragile goods." Katzschmann, Study First Author and Professor, ETH Zurich.
The technology incorporates a 3D laser scanner to check each layer for irregularities in real-time, enabling precise printing with slow-curing polymers.
Fast Track Robotics: UC San Diego's Efficient 3D Printing Method
UC San Diego engineers designed insect-like soft robots using fused deposition modeling (FDM) 3D printers and standard filament materials. Their innovation involves printing the rigid exoskeleton features onto a soft body rather than inserting soft materials into a rigid frame.
This flexoskeleton approach results in high bond strength between materials, improved resistance and easier printing of detailed structures. The process takes around 10 minutes per unit, costing less than $1 in materials, and requires less than three hours to assemble and fabricate a functioning robot.
The method allows for the efficient production of groups of robots with minimal manual assembly and holds potential applications in industries such as disaster response and exploration of unsafe zones.
3D Printed Magnetically Actuated Soft Robots for Biomimetic Functions
Chinese researchers blended polylactic acid (PLA) and iron particles to 3D print magneto-active soft material (MASM) samples. In addition, adjusting the magnetic structures enables programming the desired deformation capabilities. The results are published in Composites Science and Technology.
The team's 3D-printed biomimetic structures, inchworm, manta ray, and soft gripper demonstrated complex functions like locomotion, swimming, and grabbing under magnetic control.
The successful fabrication of actuators and soft robots from the stable, accurate and quickly transforming MASM showcases 3D printing's potential to design the complex geometries needed for high-performance soft robots in medical care and bionics.
Autonomous 3D-Printed Pneumatic Gripper
UC San Diego roboticists, in collaboration with BASF, designed a 3D-printed soft robotic gripper with integrated gravity and touch sensors. The innovative printing method, involving continuous nozzle tracing, minimizes defects and enables thinner walls (0.5 mm), enhancing flexibility.
The gripper has built-in gravity and touch sensors alongside pneumatic valves to control compressed air to trigger grip and release functions. Its fluidic logic enables the robot to autonomously remember when it has grasped an object.
It's the first time such a gripper can both grip and release. All you have to do is turn the gripper horizontally. This triggers a change in the airflow in the valves, making the two fingers of the gripper release.
Yichen Zhai, Lead Author of the paper.
Future Outlook
3D printing has revolutionized the speed and efficiency of design and fabrication processes in soft robotics. However, some persistent challenges remain to be addressed before 3D-printed soft robots transition from academic research prototyping to widespread real-world implementations.
For example, the restricted range of printable soft materials limits attainable mechanical properties and performance metrics for intended robot functionality, highlighting the necessity of developing custom-formulated 3D printable materials tailored to specific application requirements (e.g., wearable assistive robots).
Nonetheless, the tremendous progress in 3D printing soft active materials and structures has established highly promising foundations and an outlook for accelerating innovations in soft robotics. Advancements in multi-material printable formulae matching diverse functionality needs will likely transform 3D-printed soft robots from early lab studies and proofs-of-concept closer towards practical realizations.
References and Further Reading
Bergamin, F. (2023). Printed robots with bones, ligaments, and tendons. [Online]. ETH Zurich. Available at: https://ethz.ch/en/news-and-events/eth-news/news/2023/11/printed-robots-with-bones-ligaments-and-tendons.html
Buchner, T. J., Rogler, S., Weirich, S., Armati, Y., Cangan, B. G., Ramos, J., ... & Katzschmann, R. K. (2023). Vision-controlled jetting for composite systems and robots. Nature, 623(7987), 522-530. https://doi.org/10.1038/s41586-023-06684-3
Gul, J. Z., Sajid, M., Rehman, M. M., Siddiqui, G. U., Shah, I., Kim, K. H., ... & Choi, K. H. (2018). 3D printing for soft robotics–a review. Science and technology of advanced materials, 19(1), 243-262. https://doi.org/10.1080/14686996.2018.1431862
Patringenaru, P. (2020). Thanks to "Flexoskeletons," These Insect-Inspired Robots are Faster and Cheaper to Make. [Online]. UC San Diego. Available at: https://today.ucsd.edu/story/flexoskeletons
Patringenaru, P. (2023). This 3D Printed Gripper Doesn't Need Electronics to Function. [Online]. UC San Diego. Available at: https://today.ucsd.edu/story/this-3d-printed-gripper-doesnt-need-electronics-to-function
Qi, S., Guo, H., Fu, J., Xie, Y., Zhu, M., & Yu, M. (2020). 3D printed shape-programmable magneto-active soft matter for biomimetic applications. Composites Science and Technology, 188, 107973. https://doi.org/10.1016/j.compscitech.2019.107973
Sachyani Keneth, E., Kamyshny, A., Totaro, M., Beccai, L., & Magdassi, S. (2021). 3D printing materials for soft robotics. Advanced Materials, 33(19), 2003387. https://doi.org/10.1002/adma.202003387
Wallin, T. J., Pikul, J., & Shepherd, R. F. (2018). 3D printing of soft robotic systems. Nature Reviews Materials, 3(6), 84-100. https://doi.org/10.1038/s41578-018-0002-2
Yap, Y. L., Sing, S. L., & Yeong, W. Y. (2020). A review of 3D printing processes and materials for soft robotics. Rapid Prototyping Journal, 26(8), 1345-1361. https://doi.org/10.1108/RPJ-11-2019-0302
Disclaimer: The views expressed here are those of the author expressed in their private capacity and do not necessarily represent the views of AZoM.com Limited T/A AZoNetwork the owner and operator of this website. This disclaimer forms part of the Terms and conditions of use of this website.