Often likened to the hand and fingers of a robot, End-of-Arm Tooling (EOAT) is the key to unlocking the potential of automated systems, enabling them to perform a myriad of tasks with precision and efficiency. This article provides a comprehensive guide to EOAT, delving into its working applications in various robot handling scenarios and exploring the latest developments in this ever-evolving field.
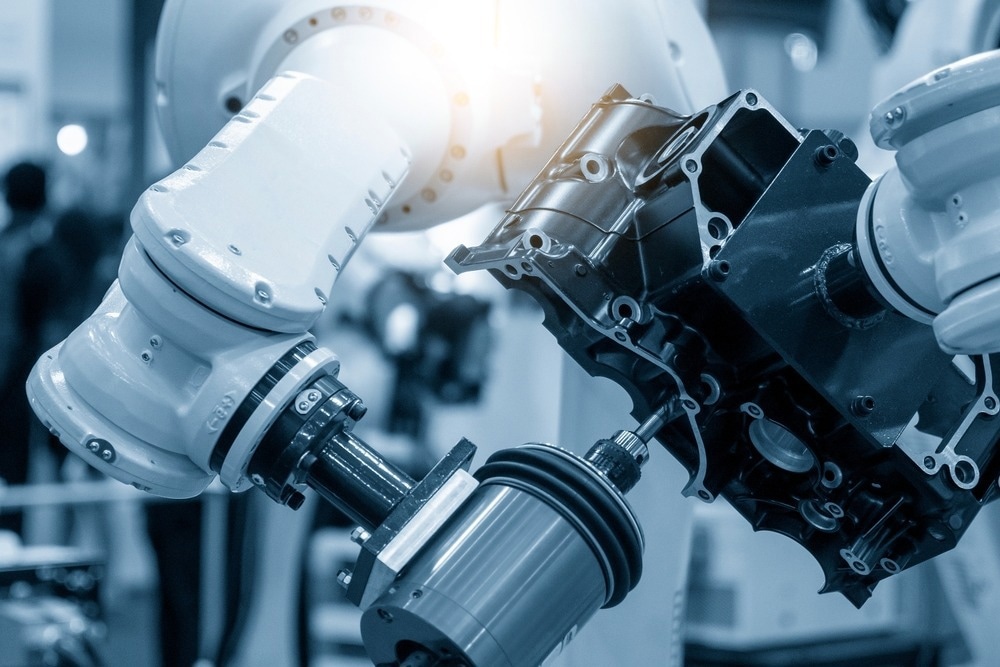
Image Credit: V/Shutterstock.com
What is End-of-Arm Tooling (EOAT)?
EOAT refers to the devices attached to the end of a robotic arm, facilitating interaction with the objects in its environment. The design and functionality of EOAT are highly diverse, ranging from simple grippers and suction cups to more complex systems incorporating sensors, cameras, and specialized tools depending on the specific task a robot is assigned.
The primary function of EOAT is to grasp, manipulate, or interact with objects in a manner that mimics human dexterity. Achieving this requires a careful balance between rigidity and flexibility, as the tool must be sturdy enough to handle varying loads while being adaptable to different shapes and sizes. EOAT can be pneumatically, hydraulically, or electrically powered, with the selection depending on factors such as speed, force requirements, and the nature of the application.
Applications of EOAT in Robot Handling
EOAT, with its versatile design and adaptability, revolutionizes various industries by excelling in tasks ranging from precision pick-and-place operations to intricate assembly processes.
Pick and Place Operations
One of the most common applications of EOAT is in pick-and-place operations. In manufacturing and logistics, robots equipped with specialized grippers can efficiently pick up items from one location and precisely place them in another. This is particularly valuable in assembly lines where speed and precision are paramount. The ability of EOAT to adapt to different shapes and sizes ensures a wide range of products can be handled seamlessly.
Material Handling
EOAT plays a vital role in material handling tasks, facilitating the movement of raw materials or finished products within a facility. Whether lifting, stacking, or organizing items, robots with well-designed EOAT can significantly enhance efficiency in warehouses and distribution centers. The ability to handle different materials, including fragile items, makes EOAT an indispensable tool in this domain.
Welding and Assembly
Robots equipped with EOAT are often employed for welding and assembly tasks in manufacturing processes, especially in the automotive and electronics industries. Advanced EOAT designs can hold and position components with utmost precision, ensuring the accurate assembly of intricate products, improving the quality of the end product and enhancing the speed and consistency of the assembly process.
Packaging and Palletizing
EOAT finds extensive use in the packaging industry, where robots equipped with specialized tools can efficiently pack products into boxes, crates, or pallets. The ability to handle various packaging formats and adapt to different product sizes makes EOAT an ideal solution for automating packaging processes, reducing labor costs and enhancing packaging operations' overall speed and accuracy.
Inspection and Quality Control
With the integration of sensors and cameras into EOAT, robots can perform intricate inspection and quality control tasks. This is particularly valuable in industries where precision and quality assurance are critical, such as electronics and pharmaceuticals. The combination of robotic manipulation and sensor technologies allows for detailed inspections, identifying defects or inconsistencies with high accuracy.
Recent Development
In a recent case study conducted by researchers at the University of Greenwich, the focus was on addressing the challenges faced by manufacturing organizations in developing robotic tooling assets. Traditionally, the incremental development of these assets led to highly customized and costly designs, hindering reusability. The researchers proposed a strategic approach involving the development of modular tooling platforms to streamline the design process, reduce manufacturing costs, and improve time-to-deployment.
The case study applied modular design concepts to create a robotic end-of-arm tooling (EOAT) platform for pick-and-place operations in the medical plastic injection molding industry. By incorporating modularity archetypes such as Bus Modularity, the researchers achieved significant cost reductions and reduced lead times for EOAT manufacturing.
The modular platform not only allowed for the efficient purchase of components in volume but also demonstrated potential for remanufacture, saving up to 100% of the original tool cost. The study highlights the success of applying modular design principles in a real-world industrial setting, emphasizing the potential for broader applications in complex design environments.
Conclusion
End-of-arm tooling is undeniably the linchpin of robotic handling systems, allowing robots to extend their reach into various industries and applications. From pick and place operations to intricate assembly tasks, the versatility and adaptability of EOAT make it an indispensable element in the realm of automation.
As technology continues to advance, integrating sensors, machine learning, and modular designs, EOAT is evolving to meet the increasing demands of modern industries. As we look to the future, EOAT will continue to shape the automation landscape, driving efficiency, precision, and innovation across diverse sectors.
References and Further Reading
Arey, D. & Gao, J. (2019) A Modular Platform Design Approach to Cost Reduction in Robotic end-of-arm Tooling: a Case Study. Available at: https://www.researchgate.net/publication/337486739
Gómez-de-Gabriel, J. M., et al. (2019). Rapid end-of-arm-tooling manufacturing of vacuum grippers. International Journal of Computer Integrated Manufacturing. doi.org/10.1080/0951192X.2019.1690684
Ong, U. et al. (2018). 3D printed end of arm tooling (EOAT) for robotic automation. Robotics. doi.org/10.3390/robotics7030049
Pesca, P. & Afonso, D. G. (2023). Extended Reality in End of Arm Tooling Development and Assembly. Advances in Science and Technology. doi.org/10.4028/p-SUb3W5
Disclaimer: The views expressed here are those of the author expressed in their private capacity and do not necessarily represent the views of AZoM.com Limited T/A AZoNetwork the owner and operator of this website. This disclaimer forms part of the Terms and conditions of use of this website.