Industry 4.0 is a new paradigm for technology, where humans, robots, and computers work together seamlessly to produce value more efficiently. Despite extensive preparations and discussions around actualizing Industry 4.0, the technological limitations of current robotics must be overcome first.
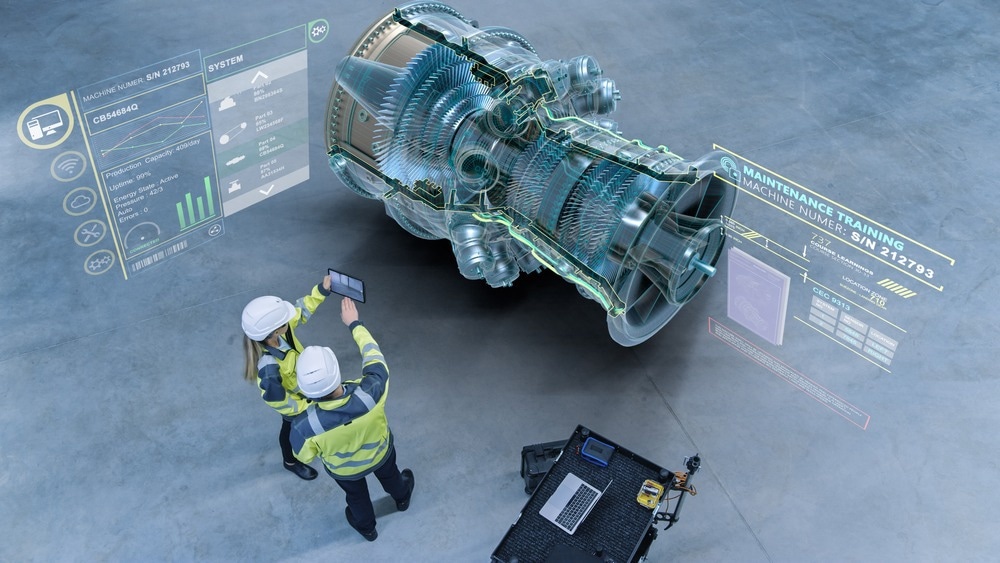
Image Credit: Gorodenkoff/Shutterstock.com
What Is Industry 4.0?
The first industrial revolution saw the arrival of steam power, the second saw the arrival of long-distance communication and electric power, and the third saw the introduction of computers to industry.
The term “Industry 4.0” was coined by the German government in 2011. Industry 4.0 was introduced as a way to acknowledge the increased digitization of industrial devices, systems, and processes. It illustrates a fourth industrial revolution in which digital and physical systems work together for value and efficiency benefits.
In part, this is reflected in the advent of the Internet of Things (IoT) systems, in which components are imbued with computer processing and connectivity capabilities.
What Role Do Robots Play in Industry 4.0?
The role of robots in Industry 4.0 is integral to the vision laid out above. One of the key elements of the new industrial paradigm is increased collaboration between robot and human workers, hinged on improved robot capabilities, artificial intelligence (AI) technologies, and redesigned industrial processes.
This will require lightweight, adaptable, easy-to-use, and safe robot technologies to be developed or deployed across the industry. Cutting-edge robot technology today must be responsive to their surrounding environment, workers and other machines within it. Robots must also be better connected with production cycles and big data acquisition and manipulation, as well as integrated into manufacturing processes involving other machines, data acquisition, and human workers.
The State of Robotics and Innovations Required for Industry 4.0
In 2020, MIT researchers and members of the institute’s Interactive Robotics Group published a research summary entitled The State of Industrial Robotics: Emerging Technologies, Challenges, and Key Research Directions.
The research was focused on surveying robotics and connective technology developments in the decade since the introduction of the Industry 4.0 concept. Below are some key areas for robotics development that facilitate the new industrial processes that Industry 4.0 envisions.
Sensing, Perception, and Vision
A key bottleneck identified by the MIT researchers is in developing sensing, perception, and vision technologies for robotics. These functions are necessary for “pick and grip” robots to work effectively in unplanned and changing physical environments.
The researchers stated that vision systems on the market and the algorithms that drive them often break down in real industrial settings. While this technology tends to work in laboratory settings, it demonstrates poor reliability in the field. Algorithmic solutions to poor image sensors are not robust enough, said the researchers, for industrial use.
Collaboration with Humans and Ease of Use
Human-robot collaboration is a key driver of modern industrial practices. The MIT researchers cited evidence that collaboration is more effective - in terms of production results and smooth operations - than work silos in which robots are kept well away from humans and other robots.
Collaborative robots, or cobots, are designed to work alongside humans and other robots without safety fences in shared spaces in close physical proximity to one another. This is a step change away from the “lights out” fully automated factories of the past few decades.
Robots need to be more lightweight to achieve collaboration, making them safer to work alongside, algorithmically capable (more “intelligent”), and more affordable, both in terms of initial investment and ongoing maintenance. However, the current state-of-the-art cobot technology is still too slow or not strong enough for industrial purposes.
Relatedly, researchers also highlighted the problems of complicated robot programming interfaces that require extensive training and programming knowledge to operate. The ability of workers to repurpose and adapt robots according to dynamic needs in the changing manufacturing environment is limited as a result.
Integration costs are another limitation holding back the widespread adoption of cobots. Even as robot hardware becomes cheaper to acquire, integration with existing processes is costly and frequently requires the services of specialist integrator businesses.
Producing Valuable Data from Large Datasets
While many industries have adopted large-scale data acquisition processes into their practices in the last few decades, the wealth of data generated is not always valuable. In other words, it has not always led to improved processes or greater profitability.
The MIT researchers highlighted this issue of value over size in data acquisition, arguing that better infrastructures and handling processes for data are required to realize the potential of data that IoT-based technology collects.
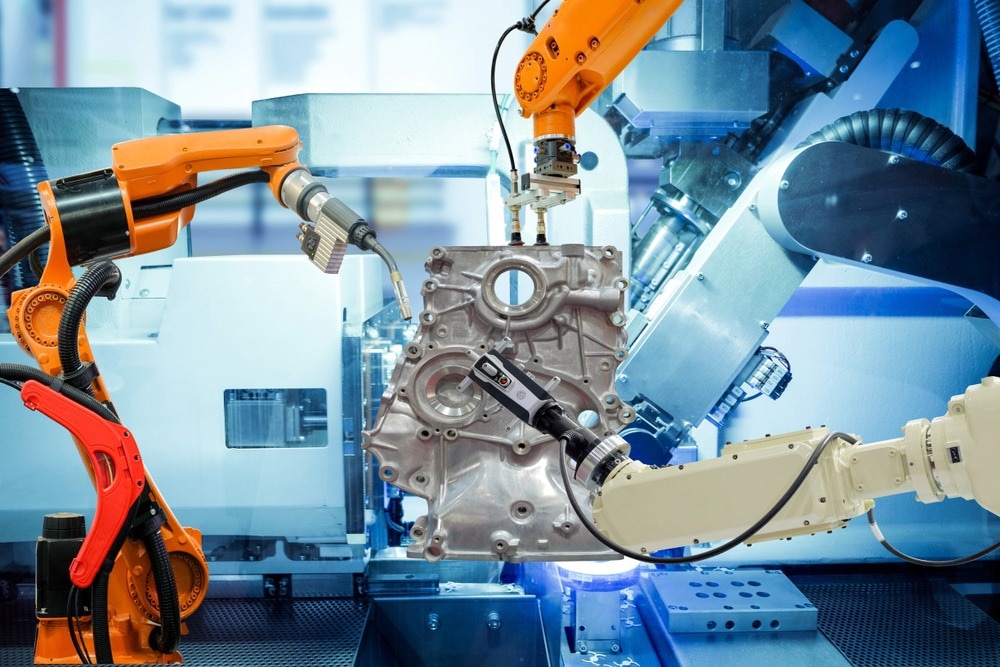
Image Credit: FeelGoodLuck/Shutterstock.com
Autonomous and Adaptable Robots
Again, the autonomy and adaptability of industrial robots are closely related to the above challenges. As robots become better at sensing their surrounding environment, better and safer at collaborating with human workers, and better able to handle data and produce valuable datasets, they will become more autonomous and easier to adapt to dynamic processes.
Robots with high levels of autonomy and adaptability will generate better returns on investment for the industry due to avoiding obsolescence as business needs change.
Related to this is the problem of standardization and integration. MIT researchers cited business concerns that investment in robots for Industry 4.0 could be rendered useless if robot manufacturers stop supporting hardware or integration between products from different companies.
Future Outlook of Robotics in Industry 4.0
These limitations are well-known to researchers and product developers alike. Industry 4.0 still offers a potentially better way of organizing industrial processes, and the role of robots is essential to realizing this vision.
References and Further Reading
Crowe, S. (2021). The state of industrial robotics: challenges & opportunities. [Online] The Robot Report. Available at: https://www.therobotreport.com/state-of-industrial-robotics-challenges-opportunities/
Sanneman, L., C. Fourie, and J. Shah (2020). The State of Industrial Robotics: Emerging Technologies, Challenges, and Key Research Directions. [Online] MIT Work of the Future. Available at:https://doi.org/10.48550/arXiv.2010.14537
Disclaimer: The views expressed here are those of the author expressed in their private capacity and do not necessarily represent the views of AZoM.com Limited T/A AZoNetwork the owner and operator of this website. This disclaimer forms part of the Terms and conditions of use of this website.