Interoperability is the ability of a computer-based system to exchange information with other computer-based systems. Interoperability is an essential step in growing a future robotics environment, where the full potential of robot assistance for research, industry, and society can be realized.
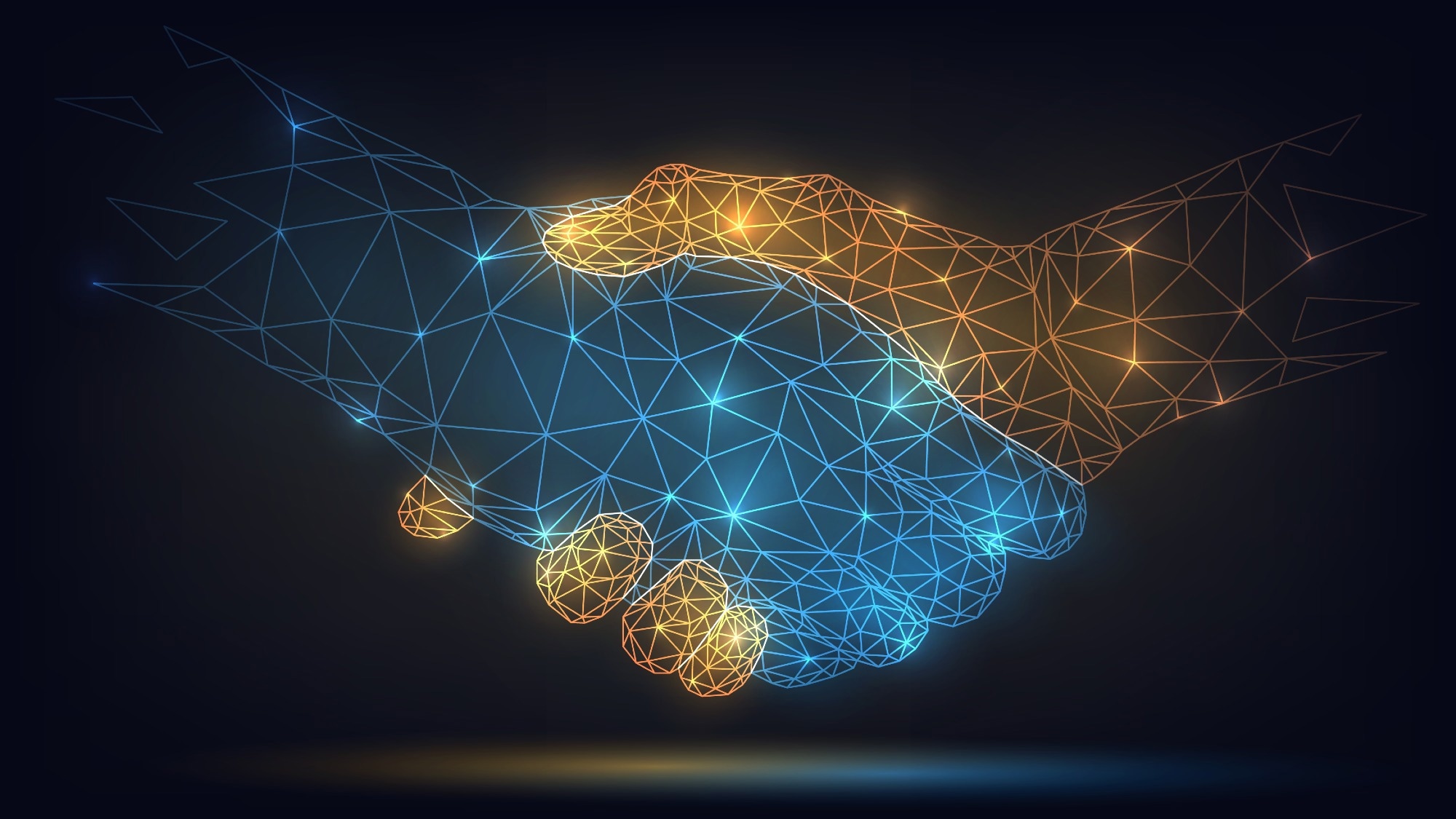
Image Credit: Lidiia/Shutterstock.com
Robot interoperability enables synergies between different technologies to materialize over time. In turn, this creates new businesses, business models, and use cases throughout all realms of human endeavor.
But the recent fast growth in the robotics industry, coupled with the technologically complex nature of innovation in the sector, has presented some major challenges to enabling effective robot-to-robot partnerships.
At present, too few robot systems are designed with universal interoperability in mind, and no universal protocol has arisen yet to simplify interoperability for robot manufacturers.
Robot interoperability is also a necessary feature for industrial automation technologies that need to fit into existing systems, such as manufacturing facilities and supply chain networks.
Shifting to Robotics
In large businesses or more complicated technological sectors, the level of investment required to make robots and existing infrastructure and hardware work together effectively can be prohibitive.
Retrofitting the various sensors, WiFi or Bluetooth connection, charging points, and supervisory control software can be significant even for medium-scale industrial operations.
In many instances, it is cheaper and more efficient to retain a human workforce than to upgrade devices and sensors for perception, mobility, and manipulation to the point where a robot system is more effective than human labor.
Trending Toward More Interoperability in the Future
Historically, industrial robotic systems have been designed for bespoke applications where the entire automation process is designed from the ground up for a specific purpose. As a result, innovation in robotics has tended to neglect concerns over interoperability.
State-of-the-art industrial automation typically relies on custom software and hardware setups that have been uniquely tailored to work in a simple, constrained environment. Often, these systems include human labor to work with flexible materials, subtle alignment, or adroit fastening.
But as robot technology advances – especially as robots get more degrees of freedom, more ability to work alongside humans simultaneously, and more computer processing “brain” power – interoperability will become increasingly important.
More interoperability between different robot systems would benefit large manufacturing corporations and small industrial facilities just the same. At any scale, modern manufacturing must continually reconfigure production systems and processes as markets and business needs are dynamic.
In advanced manufacturing sectors, this need to be flexible and responsible to dynamic market forces is even more pronounced.
Robotic systems developers, manufacturers, and vendors will also ultimately benefit from giving more attention to interoperability. This is because modular, adaptable robot systems on the market will likely drive more widespread adoption of automation and robotics throughout the industry.
Behind the Rise in Interoperability
There are a number of drivers that will likely increase levels of interoperability in the next few years of robotics research and development.
Chief among these is an increasing availability – and demand – of mobile robot systems. Technological advances are resulting in cheaper and more easily accessible autonomous mobile robots.
As these robots have greater degrees of freedom (that is, they are increasingly not fixed in place, attached to a rail system, or confined to an isolated working area), they present more use cases where multiple robot systems might need to work alongside each other. Interoperability is essential for such an arrangement to work.
Alongside the increase in robot mobility has come an increase in robot autonomy. Ever more advanced software, including artificial intelligence (AI), enables robots to do more tasks for longer without human intervention.
Because of this, again, more use cases are arising in which it will be beneficial to put multiple robot systems to work in the same area, on the same piece of work, at the same time. Again, interoperability will be a must.
Many of these uses are arising as a result of another global trend in robotics today: increased specialization for robots. Robots designed to perform more complicated tasks often achieve this at the sacrifice of performing a wide range of tasks.
This means that more can be done autonomously, but more hardware is needed to do it. To get multiple specialized robots to work according to commercially viable timeframes, they must often work simultaneously and in contact with each other. Interoperability, again, is needed.
Increasingly, the robotics industry is also beginning to move toward modular and investment-light robotics systems. The robotics as a service sector, for example, follows the everything as a service trend by offering temporary use of robot services for a subscription fee, without the requirement for an initial investment in hardware.
Manufacturing and other industrial processes will increasingly be able to deploy custom, bespoke robot systems to tackle unique challenges. These systems will be tailored and made from multiple original equipment manufacturers’ (OEMs’) offerings and will rely on the robotics industry embracing interoperability wholesale.
References and Further Reading
NIST. Robotic Systems Interoperability and Integration. [Online] NIST. Available at: https://www.nist.gov/programs-projects/robotic-systems-interoperability-and-integration
Schlechtriem, M. (2022). Interoperability: A Key Challenge for the Robotics Industry. [Online] How To Robot. Available at: https://www.howtorobot.com/expert-insight/interoperability
Serrano López, D., et al. (2017). Interoperability in a Heterogeneous Team of Search and Rescue Robots. Search and Rescue Robotics - From Theory to Practice. doi.org/10.5772/intechopen.69493
Disclaimer: The views expressed here are those of the author expressed in their private capacity and do not necessarily represent the views of AZoM.com Limited T/A AZoNetwork the owner and operator of this website. This disclaimer forms part of the Terms and conditions of use of this website.