The use of shape memory polymers in soft robotics and actuators is discussed in this article, exploring the benefits they bring and future outlooks on this technology.
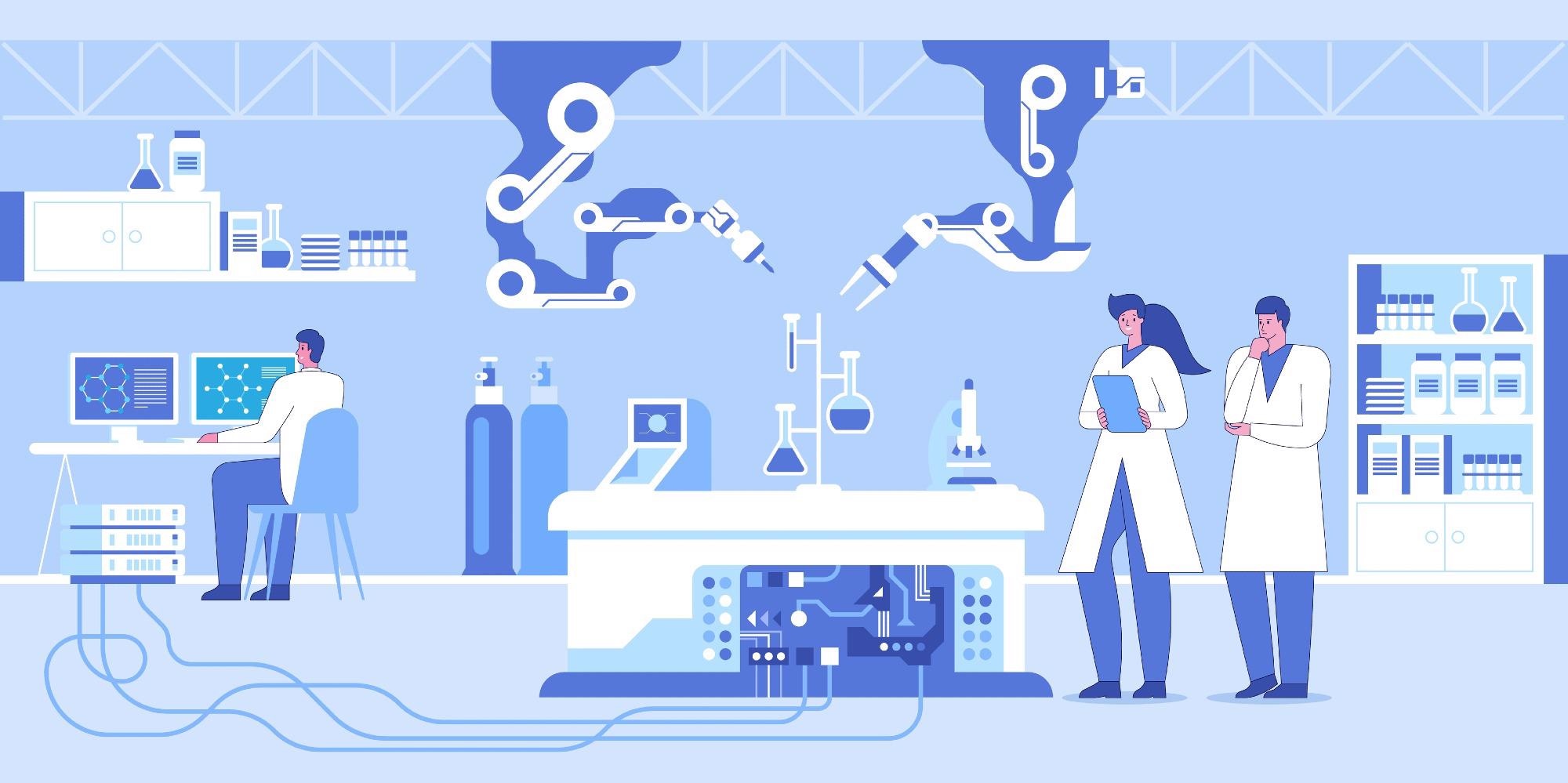
Image Credit: Ico Maker/Shutterstock.com
Soft robotics has expanded rapidly due to the inexpensive mass production of materials, as well as their lightweight and flexible properties. Soft robots can resist massive deformations, conduct complicated movements, adapt to shapes, and survive collisions without being damaged, making them ideal for applications requiring safe contact with humans, fragile items, and the environment. Therefore, there has been a lot of research in designing and fabricating more advanced soft robots for various sectors like renewable energy, medical, wearable, aerospace, and automotive sectors in recent years.
Programmable Soft Robotics
Programmable soft robots have a reversible response and can be retrieved to the initial state once the task is completed. Several actuation techniques have been investigated in programmable soft robotics to create the desired motion when external stimuli are applied. Such actuation methods are often chosen based on the required functionalities, tethered power sources, operational environment, and application size scale.
Why SMEs are Needed in Soft Robotics and Actuators
Conventional actuation mechanisms are irreversible, limiting the development of programmable soft robots since they physically occupy space, complicate the design process, and are difficult to miniaturize. Hence, there is a need for new advances to create untethered, programmable soft robots that show repeatable actuation and multi-functionalities.
Shape memory polymers or SMEs are the solutions to this problem. These materials can remember one or more momentary shapes from a permanent shape and can be classified into three major classes (one way, multi-way and two-way SMEs) based on the number of shapes that they can remember.
For the development of untethered robotic systems and programmable and reversible responses, two-way SMEs have great potential. Moreover, the properties of SMEs like biodegradability, biocompatibility, synthetic flexibility, easy processability, high deformability, low density and low cost make them advantageous, and they can increase the functionalities of soft robots.
Manufacturing of SMEs for Soft Robotics
Mostly conventional fabrication methods are used for the manufacturing of SMEs instead of 3D printing. The reason for not using 3D printers more frequently is that the applicability of current 3D printing methods to more recent SMEs is limited.
The most commonly used 3D printing techniques for the manufacturing of SMEs are polyjet and extrusion printing. For SME-based soft robots, a polyjet printer is used since the materials having tunable mechanical properties can be used in polyjet printing. However, polyjet printing comes with drawbacks like limited material choices, several resin properties requirements, and high equipment costs.
Similarly, extrusion-based printing for SME-based soft robots and actuators is advantageous due to its versatility. However, the drawbacks associated with extrusion-based printing include low resolution and slow printing speed.
Applications
SME-based soft robots have various applications in several scientific fields. For example, programmable soft robots based on SMEs are used in the biomedical field for drug delivery systems. Similarly, these are used in aerospace applications as deployable or exploration components. Two-way SME-based actuators are promising for dynamic building facades and energy savings. To increase the variety of application fields, further efforts are being made. However, extensive research is still needed to enhance material properties like long-term stability, operational temperatures, recovery stress, transparency, and extension rate.
There are several SME-based soft robotic components like complaint mechanisms, periodic structures and stresses capable of programmable motion. Advanced capabilities can be achieved by integrating these components into soft robotic systems that are more complex and advanced.
The application potential for SME-based soft robotics and actuators is very broad. However, the real implications of these applications are limited because of the lack of standards of manufacturing techniques for complex components and of 3D printed SMEs.
Future Outlooks
The future for SME-based soft robotics and actuators looks very promising. With the advancement in technology, the evolution of SME-based soft robotics is expected to lead us to a new era of robotics. However, to achieve that advancement, extensive research is required to develop new and more suitable 3D printing methods. Also, there is a need to study novel inks to achieve 3D printed multi-functional SMEs.
For future advancement, SME soft robots' response time and shape-changing speed should be improved since these are the key features for actuation. These features depend on actuation stimulus, geometrical design and properties of materials.
In advanced soft robotics applications, complex and controllable movements are extremely important. For this purpose, one of the areas where research can further be advanced is localized heating since it provides a simple and efficient method.
Another area where researchers can advance is function or property shifting features. Although shape-shifting features have been very useful in past; however, function or property shifting features will increase the autonomy of these SME-based soft robots. For this purpose, new fabrication strategies and integrated design need to be proposed and developed.
References and Further Reading
Jin, B., Song, H., Jiang, R., Song, J., Zhao, Q., & Xie, T. (2018). Programming a crystalline shape memory polymer network with thermo-and photo-reversible bonds toward a single-component soft robot. Science advances, 4(1), eaao3865. https://www.science.org/doi/full/10.1126/sciadv.aao3865
Scalet, G. (2020). Two-way and multiple-way shape memory polymers for soft robotics: An overview. In Actuators (Vol. 9, No. 1, p. 10). Multidisciplinary Digital Publishing Institute.http://dx.doi.org/10.3390/act9010010
Disclaimer: The views expressed here are those of the author expressed in their private capacity and do not necessarily represent the views of AZoM.com Limited T/A AZoNetwork the owner and operator of this website. This disclaimer forms part of the Terms and conditions of use of this website.