AZoRobotics speaks with Michael Bartlett from Virginia Tech about his multifunctional shape-morphing robotic endoskeleton. The material has great promise for multifunctional robotics, wearable devices and self-healing applications.
What inspired your research into creating a multifunctional shape-morphing material with reversible and rapid polymorphic reconfigurability?
When we started the project, we wanted a material that could do three things: change shape, hold that shape, and then return to the original configuration, and to do this over many cycles. These types of shape-morphing materials are key components for emerging technologies, ranging from stretchable electronics and soft robotics to reconfigurable structures and multimodal vehicles.
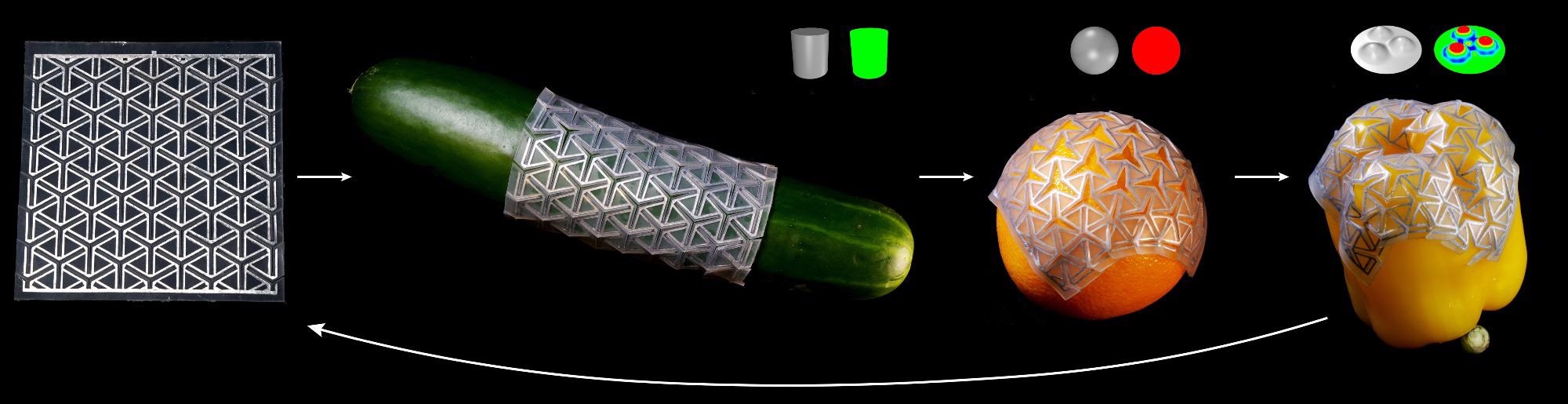
Image Credit: Virginia Tech
One of the challenges was to create a material that was soft enough to dramatically change shape yet rigid enough to create adaptable machines that could perform different functions.
What role did kirigami – the Japanese art of making shapes out of paper by cutting – play in the creation of the material?
We utilized kirigami designs in soft rubbers in combination with a metal endoskeleton and embedded liquid metal heaters. This created a multimaterial kirigami composite. The kirigami architecture allows us to undertake extreme deformations, achieve complex shapes, and display nonlinear force-extension characteristics, which enables high shape retention during shape fixing in different configurations.
This kirigami composite design allows us to create and fix complex shapes, from cylinders to balls to the bumpy shape at the bottom of a pepper.
Present-day soft machines struggle to achieve complex configurations, morph into shapes to support loads, and go between multiple states reversibly. Why is this?
Soft machines display unique abilities to undergo large deformations due to the soft and deformable materials that make up the machine. However, this softness can also make it challenging to support loads during operation.
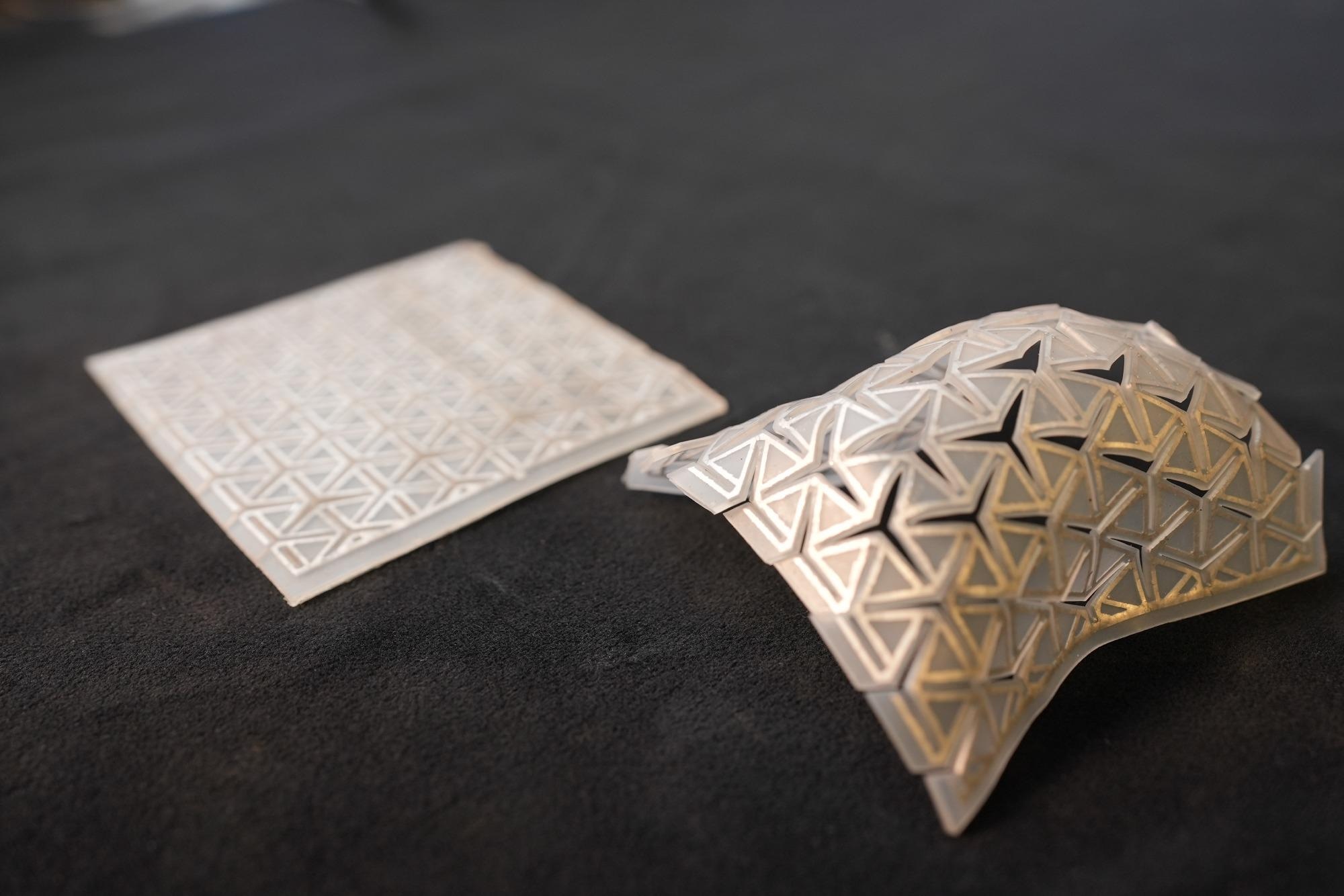
Image Credit: Virginia Tech
This intrinsic trade-off between load-bearing capacity and high deformability in homogeneous sheets can be limiting for soft matter engineering applications that require shape change while also being able to support loads that come from external forces, motors for locomotion, or interaction with the environment.
Can you provide an overview of how your material enables soft robots to change shape, hold shape, and then return to their original configuration?
We created a kirigami composite metamaterial sheet that synergistically combines shape morphing of kirigami architectures, shape fixing through plasticity and phase change of an embedded metal endoskeleton composed of low-melting-point alloy (LMPA), and reversibility with an integrated heater to trigger a phase change in the LMPA to elastically recover shape and enable self-healing.
Morphing drone from the Soft Materials and Structures Lab
Video Credit: Virginia Tech
This kirigami composite overcomes trade-offs in deformability and load-bearing capacity and eliminates power requirements to sustain reconfigured shapes.
How did you assess the efficacy of your material, and what were the results?
One of the key parameters in our shape morphing research was the shape-fixity ratio. This evaluates the amount of a shape that we can fix into place.
We found that we could lock in ~85% of a shape nearly instantly and 100% of a shape if we morphed with the melted endoskeleton and then solidified in a shape. We further evaluated the speed at which we could lock in a shape. We found we were able to achieve and lock in shapes in ∼70 milliseconds.
Did you come across any challenges during your research, and if so, how did you overcome them?
We came across multiple challenges throughout this research. One challenge was the integration of multiple different materials into an architectured material stack. We are currently working to create new materials, structures, and fabrication approaches to enable different morphing capabilities into composite materials.
According to your research, this material can be combined with onboard power, control and motors. What does such a combination achieve?
The ability to incorporate robotic components such as onboard power, control and motors with multifunctional, morphing materials allowed us to create morphing robots.
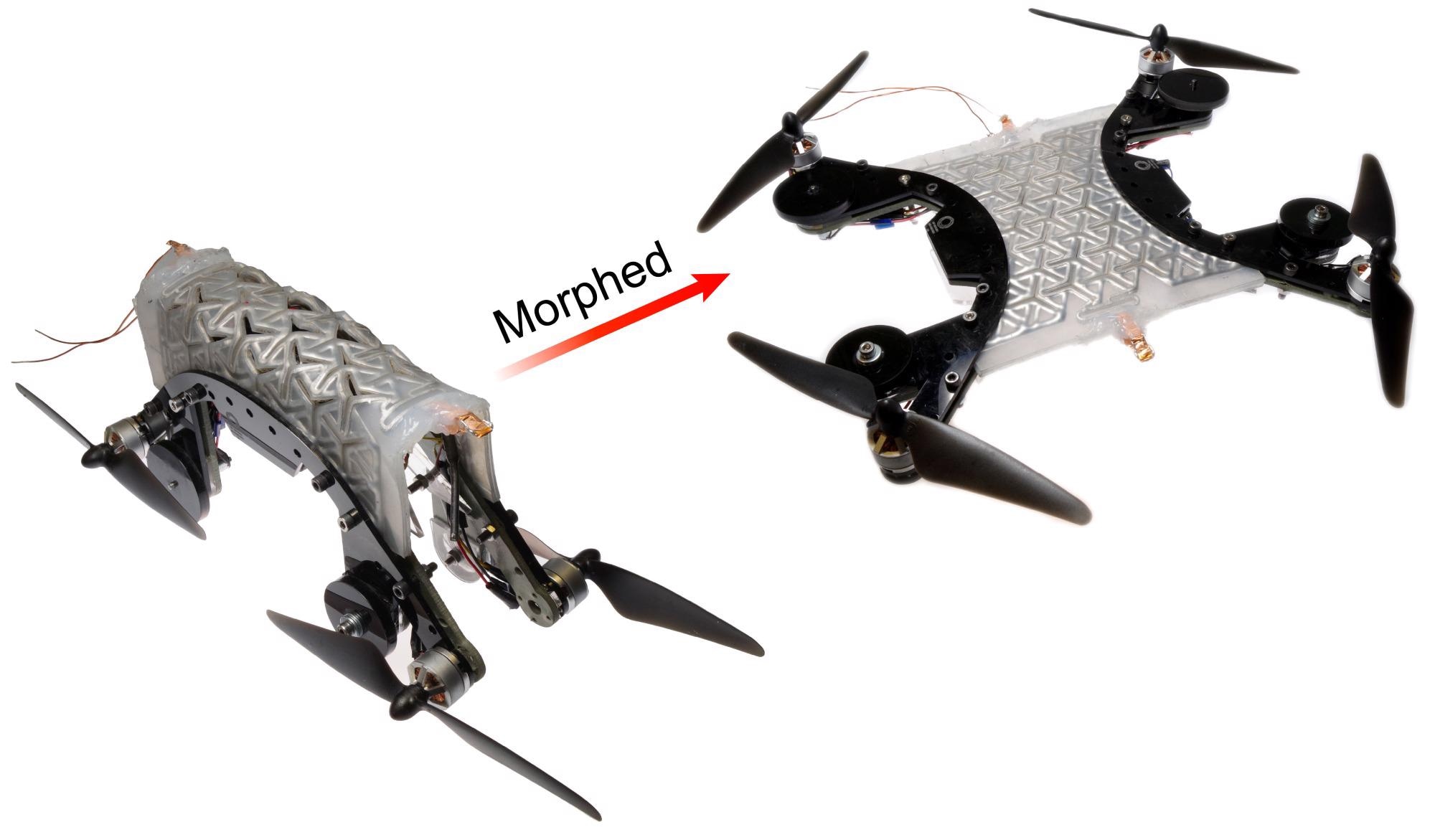
Image Credit: Virginia Tech
We showed this capability by developing a functional morphing drone with multiple remotely controlled locomotion modes enabled by an autonomous morphing from a ground to air vehicle configuration. We further show a morphing underwater machine that can be reversibly deployed to collect cargo through integrated water propulsion and buoyancy control.
What are the potential applications of this novel technology?
We believe this advance can lead to dynamic functionalities in soft robotic systems. This could include mobile and deployable machines that can be reconfigured in the field for multiple tasks that require a load-bearing capability. This could also create additional functionalities such as field reconfigurable materials to rapidly support injuries or multipurpose robotics for gripping, carrying or delivering supplies.
What are the next steps for your research?
One of the challenges in our current approach is the need to combine shape-morphing composites with external actuation mechanisms. For example, we coupled the morphing composite with integrated pneumatic actuators. This allows for controlled transitions between multiple stable states without external intervention. Therefore, the incorporation of actuation schemes is key to cyclic morphing behavior.
In addition to the pneumatic actuators that we have used, other actuation schemes offer intriguing opportunities for integration into the shape-morphing composites. These can include using soft active materials like liquid crystal elastomer (LCE) actuators, artificial muscles like shape memory alloy wires or carbon nanotube fibers, or tendon-driven actuation with electromechanical motors.
Where can our readers find out more?
My lab, the Soft Materials and Structures Lab, is located at Virginia Tech in the Mechanical Engineering department. Readers can visit my lab’s research website and can find the paper in Science Robotics.
About Michael Bartlett
Michael Bartlett is an Assistant Professor of Mechanical Engineering at Virginia Tech. His research focuses on soft multifunctional materials for deformable electronics and soft robotics, adaptive materials, and ‘smart’ adhesives. He received his BSE in Materials Science and Engineering from Michigan in 2008 and Ph.D. in Polymer Science and Engineering from UMass Amherst in 2013. After obtaining his Ph.D., he worked as a Senior Research Engineer in the Corporate Research Laboratory at 3M, as a Postdoctoral Fellow at Carnegie Mellon University, and was an Assistant Professor at Iowa State University before joining Virginia Tech in 2020. His research has resulted in publications, patents, media coverage, and awards, including a DARPA Young Faculty Award (YFA) and Director’s Fellowship, ONR Young Investigator (YIP) Award, the Early Career Scientist Award from the Adhesion Society, a 3M Non-Tenured Faculty Award, an ICTAS Junior Faculty Award, and an Outstanding Faculty Award (student nominated). More at: www.bartlett.me.vt.edu
Disclaimer: The views expressed here are those of the interviewee and do not necessarily represent the views of AZoM.com Limited (T/A) AZoNetwork, the owner and operator of this website. This disclaimer forms part of the Terms and Conditions of use of this website.