Oct 7 2012
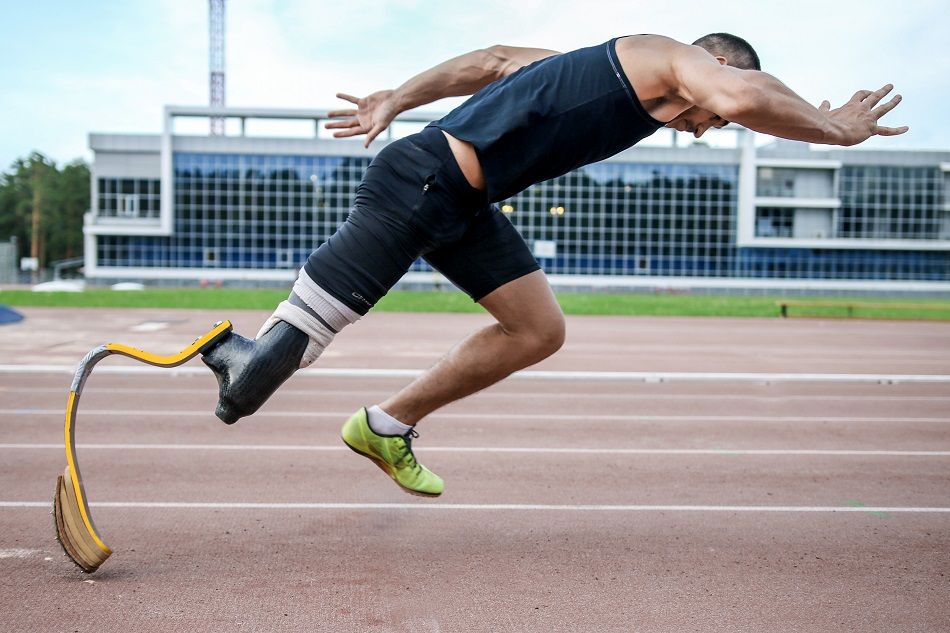
Image Credit: sportpoint/Shutterstock.com
The utilization of prosthetics dates back to the ancient Egyptian era and became more popular in the last few centuries due to an increase in amputations during the American Civil War and the discovery of anesthetics.
Modern prosthetics have become more light, compliant, and easily adaptable to different shapes and styles with the invention of more sophisticated materials and electronics. The state-of-the-art C-Leg is one of the best prosthetics available with a hydraulic cylinder, a built-in computer, and a carbon fiber frame that ensures high-performance grades. Available upper-limb prosthetics, unlike lower-limb prosthetics, are not yet versatile enough to function as a healthy limb.
Light and compact exoskeletons have been developed recently. Robotic devices used nowadays have an edge over prosthetics and exoskeletons as the user need not wear them.
Example of an Exoskeleton Design
Exoskeletons are usually articulated at seven single-axis revolute joints:
- Wrist radial–ulnar (rad-uln) deviation
- Wrist flx-ext, fore-arm pronation–supination (pron-sup)
- Elbow flx-ext
- Shoulder internal–external (int-ext) rotation
- Shoulder flexion–extension (flx-ext)
- Shoulder abduction–adduction (abd-add)
Configuration of these joints with the body is generally of one of these types:
- Anthropomorphic joints - This configuration can be classified into three types namely, 90°, 180° and axial.
- Human-machine interfaces - The design of this configuration is challenging as the human arm occupies the joint axis of rotation.
- Joint cable routing - In cable-driven devices, the mechanical joint ROMs are achieved by routing the cables either through or around the joint axes at a constant cable length.
- Singularity placement – Device configuration is known as a singularity involves the loss of degrees of freedom (DoF) while aligning two rotational axes. However, in an exoskeleton arm, the singularities occur while aligning joints 1 and 3 or joints 3 and 5.
- Power transmission - Power can be transmitted from one location to another through gear trains, fluid lines, cables, and shafts. However, the bandwidth and rigidity of the wearable robots can be achieved by selecting suitable transmission type and adjusting the placement of actuators.
Exoskeleton joint design must meet these system requirements.
- Kinematic and dynamic requirements - These requirements can be met by conducting a pilot study of activities of daily living (ADL).
- Mechanical human-machine interfaces - These interfaces are the components that mechanically link the exoskeleton structure and the human arm and also transmit force between them.
- Safety requirements - Safety precautions are required to be implemented on three levels: software, electrical and mechanical.
- Modeling the human arm - Modeling of anthropomorphic joint approximations can be performed at varying degrees of complexity and accuracy.
- Performance - The performance of the system is measured with the help of its bandwidth.
Biomechatronic Hand
The design and analysis of a multi-fingered hand prosthesis have been presented in a paper by Jingzhou Yang and colleagues and are described below.
The IOWA hand prosthesis consisting of multi-segmental joints was developed to actuate each finger segment with the help of a cable-conduit system that is connected using two or three mechanical springs that help capture the functional capacity of the hand. As in the human hand, flexor tendons help bend and rotate this structure and this can also be seen with the prosthetic hand by using a single cable-conduit mechanism that transfers the linear force into axial and lateral deflection to help mobilize flexible element.
The five active fingers of the IOWA hand can bend at the distal interphalangeal, proximal interphalangeal, and metacarpophalangeal joints. However, each finger consists of conduits, cables, compression links for cable, and springs acting as joints. Compression links function as a restrainer for the conduit and as a connecting holder for the cable.
The key elements of the IOWA hand are listed below:
- The actuators can be fixed anywhere on the body as the cable conduit system realizes remote actuation of the flexible element.
- Each joint in each finger can be bent or rotated at different angles, which allows the hand to grasp complex geometry.
- The IOWA hand has adjustable stiffness/compliance characteristics to meet the user’s needs.
- Though pinch force is high at fingertips, fine motion control between two fingers is hard to achieve.
- With adjustable hand compliance and consistent design parameters, the IOWA hand has realistic finger movement.
Biomechatronic Knee
Nearly 34,500 knee amputations are being carried out every year to improve the living standards of patients. However, a completely functional prosthetic knee has not been developed yet. During amputation, a femur is cut 10 cm above the knee. The femur is joined to muscles which are located above the amputation point and this does not affect other muscles. Some of the problems faced with currently available knee prosthetics are as follows:
- Inability to turn or use a staircase
- Abnormal gait
- Navigating obstacles
The C-leg is currently the most widely used prosthetic knee. It has hydraulic cylinders to enable leg movement and a microprocessor to determine the movement by acquiring muscle impulses. It also uses strain gauges to identify where the force is applied to the knee. However, the user will face difficulties while walking downhill and running while using the C-leg.
A customized prosthetic knee for different individual needs has been proposed. It would involve these steps:
- Data mining should be carried out to imitate normal gait by measuring the length and diameter of the leg, knee flexion angles, and structure of the muscles
- Muscle impulses can be acquired to improve the maneuverability and neuro signals are recorded by using electrodes.
- The impulses are transferred to a microprocessor and power source mounted on the prosthetic. The power source can be charged using a 120V outlet.
- Muscles are simulated using actuators, which generate walking movements by controlling the microprocessor.
Sources and Further Reading
- Dellon B., Matsuoka Y. 2007. Prosthetics, Exoskeletons, and Rehabilitation. IEEE Robotics & Automation Magazine.
- Eckel B., Moore K. Revolutionizing Prosthetics: The Biomechatronic Knee.
- Perry J.C., et al. Upper-Limb Powered Exoskeleton Design. IEEE/ASME Transactions on Mechatronics 2007 12(4): 408–417.
- Yang Y, et al. A multi-fingered hand prosthesis. Mechanism and Machine Theory 2004 39: 555–581.
This article was updated on 6th February, 2020.