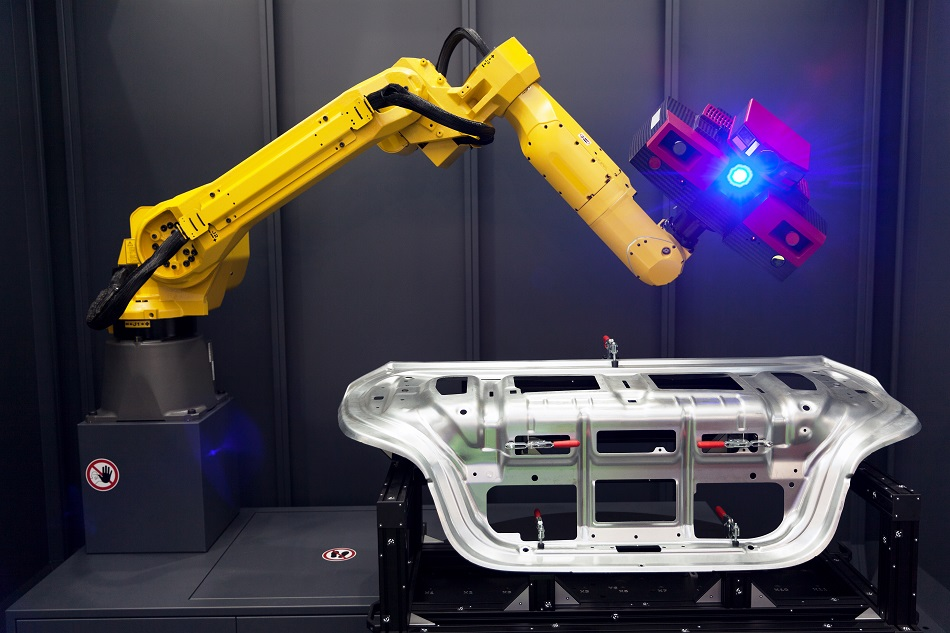
Image Credit: wellphoto/Shutterstock.com
The use of industrial robots has grown rapidly over the last few decades. A wide range of industries has adopted them. For some, they have become integral to the success of the industry.
For example, the automotive and aviation sectors heavily rely on robots to automate production lines. As these robots are developed for new and more complex tasks, the requirement for them to be precise every time has become paramount.
This is where metrology, the science of measurement, steps in. In response to the need to measure and correct the automated actions of robots, the field of automated metrology has arisen.
Coordinate measuring machines (CMMs) with direct computer control (DCC) have been developed for the auditing of automated robots used in various applications. These automated metrology solutions are commonly integrated within robotic automation processes to provide direct feedback and correct for errors in real-time.
The Need to Make Robots More Accurate
The main driver for the establishment of metrology automation has been the advancement in industrial automation. Industrial robots have been widely adopted by a number of industries to automate production lines.
These robots rely on repetitive actions. In the 70s and 80s when they had already become firmly integrated into the automotive industry, engineers were aware of their limitations in precision and accuracy.
Small errors in repetitive movements conducted over a long time can lead to big errors. This prevented them from being adopted by the aviation industry. Scientists recognized the need to improve their accuracy to make them suitable for use in this industry.
Metrology Allows Robots to Build with Perfect Accuracy
It was recognized that metrology could eliminate the errors made by the automated, repetitive movement of robots. By measuring the robot’s intricate movements over a set number of poses, the data can be used to calculate and automatically correct the robot’s movements, giving them the highest possible accuracy.
When developments to use metrology in this way first began, scientists faced a major challenge in that it was difficult to take accurate measurements from robots in varying ranges of temperature.
The laser interferometer was the equipment of choice for making the required measurements. However, the laser beam that is relied on to make precise calculations was easily disturbed by the interruption. This resulted in having to start the process again and prevented the laser interferometer from being suitable for making adjustments for robotic automation.
Modern Metrology Automation
Modern metrology automation began with the use of trackers incorporated in robots to measure actual positions and compare them with theoretical and predicted ones. The software was used to make adjustments when a mismatch occurred.
This was a successful method and many manufacturers developed their own versions of this technique. In time, this led to a demand for the development of robot calibration packages to harmonize calibration processes and platforms. At this point, the software was also able to compensate for the effects of thermal variation.
While metrology automation has remained rooted in the same basic methodology, it has seen significant advancements to improve robotic automation further.
The laser trackers were updated to be able to measure in a full six degrees of freedom. This means that fewer poses are required to gain enough information to make a correction of the end effector of the robot during a calibration cycle.
This development has moved metrology automation forward significantly as it no longer needs to calibrate the robot. Instead, the tracker can correct the position of the end effector in real-time.
These new trackers have allowed automation to finally become commonplace in the manufacture of planes. Before corrections were able to be made in real-time, automated robots were still not deemed accurate enough for many key parts of airplane construction. Now, even the placing of stringers for the fuselage section, which must be done at specific distances, is carried out by automation.
Sources and Further Reading
Disclaimer: The views expressed here are those of the author expressed in their private capacity and do not necessarily represent the views of AZoM.com Limited T/A AZoNetwork the owner and operator of this website. This disclaimer forms part of the Terms and conditions of use of this website.