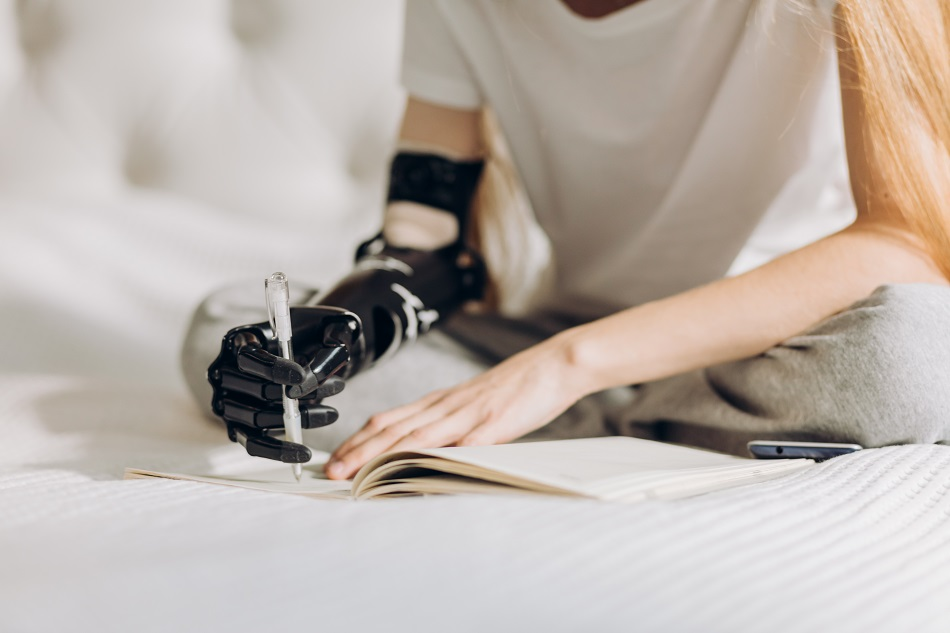
Image Credit: UfaBizPhoto/Shutterstock.com
Scientists are exploring how nanotubes can be used in robotics to improve on function and capabilities. Recently, two significant steps forward in robot technology have been achieved by incorporating nanotubes, this enhances the skin-like sense of touch in robotic and prosthetic devices, and in the creation of higher-quality artificial muscles that move soft robots.
Why Nanotubes?
Nanoparticles have been a particular focus of scientific study in recent years. The nano-sized particles have unique characteristics separate from those that they have as a bulk material, and so scientists have been exploring how to take advantage of these attributes by using nanoparticles in a variety of different applications.
Nanotubes are created from nanoparticles, specifically single particles of carbon atoms (graphene) in the form of rolled-up sheets. The reason nanotubes are of interest to researchers is because they are incredibly strong, light, and excellent conductors of both heat and electricity.
These nanotubes are useful in two specific applications in robotics.
Bringing a Sense of Touch
Scientists have devised a way to bring a skin-like sense of touch to robotics and prosthetic devices through using nanotubes.
A team at Stanford University and Xerox Palo Alto Research Center have designed a ‘digital tactile system’ (DiTact) which uses carbon nanotubes as pressure sensors alongside organic printed circuits resulting in a human-like response to touch.
The team was driven by the need to create a skin for prosthetics that communicates touch more naturally. Commonly, artificial prosthetics use a microprocessor or computer to connect the sensors with neural signals, but the innovation eliminates the need for this, combining all processes into a single system of piezoresistive pressure sensors.
The sensors are made from carbon nanotubes integrated into a flexible polyurethane plastic that is molded into pyramidal structures. When pressure is applied, the carbon nanotubes are forced closer together, allowing an electrical current to flow, resulting in changes in pressure directly converting to digital signals, mirroring the function of the skin’s tactile receptors.
Artificial Muscles
Artificial muscles currently used in robotics generally rely on systems involving hydraulics or pneumatics, which tend to be slow to respond, limiting the capabilities of movement in soft robots.
A recent breakthrough incorporating carbon nanotubes into actuators (artificial muscles) have resulted in the possibility to produce robots with more human-like movements that are quick to respond and move, and are more natural than hydraulics or pneumatics currently allow.
Researchers incorporated a carbon nanotube yarn into the actuators to create the new kind of artificial muscle. The system works by using a stiffness-variable carbon nanotube spring-like nanocomposite yarn. The yarn is created into artificial muscles by inflating epoxy resin directly onto the spring-like carbon nanotube yarn. Researchers have found it to be rapidly responsive, offering a marked improvement on current alternative systems.
The implications for this work extend from creating soft robots that have faster responses. The tests showed that the nanocomposite yarn artificial muscle could also create forces that were over 20 times greater than what is possible from human skeletal muscle.
Scientists believe that the innovation will lend itself to applications in numerous fields, such as in actuators, but also in sensors and micro-robots.
Future Directions
Research into nanotubes is still in its infancy, and the applications of this material in various sectors are still being discovered. Here, we discuss its use in improving artificial muscles and bringing human-like touch to robots. One day, we can expect more applications to be developed.
Sources and Further Reading
Disclaimer: The views expressed here are those of the author expressed in their private capacity and do not necessarily represent the views of AZoM.com Limited T/A AZoNetwork the owner and operator of this website. This disclaimer forms part of the Terms and conditions of use of this website.