The global online retailer Amazon set the Amazon Picking Challenge, in which roboticists are tasked with developing a robot that can pick and put away 12 products from a shelf, into a bag. The Shadow Robot Company, designer and manufacturer of next-generation anthropomorphic robot hands, approached precision bearing specialist, SMB Bearings, to assist them with the challenge.
Sounds easy right? Well, Amazon put forth this challenge as it is the only area of its warehousing process that isn't presently mechanized, owing to the sheer variety of objects to be packed. This presents a gap in robotics for a smart grasper that is able to effectively recognize and pick different objects. effectively.
Grasping is an issue for several industries-not just picking up an object, but grasping it well and making sure that every grasp is suitable for the object being picked.
"More and more I’ve had people come up to me asking how we can improve robotic grasping," said Rich Walker, managing director at The Shadow Robot Company. "The market is pushing us to improve the technology."
Traditional industrial grippers are built to lift up one thing before moving it and putting it down. If there are two different sets of objects, then two different grippers will be required to execute the task. Contemporary manufacturers are increasingly diverse, manufacturing reams of different products, usually with custom finishes.
Single-use tooling is no longer enough to meet the demand. An easily adaptable tooling that can pick up many different types of objects is required.
The robot engineers at the Shadow Robot Company have extensive expertise in manufacturing dextrous robotic hands for academia and nimble work. However, this type of robot is unsuitable for industrial applications. Instead, they looked to create a reliable and robust Smart Grasping System™, with the intelligence to recognize various objects and choose the appropriate grasp.
As part of the design process, the Shadow Robot Company required specific bearings with very low tolerances in dimensional accuracy. This is essential for accuracy and ease of installation of the smart grasper’s movements. So, the team got in touch with SMB Bearings as the business is renowned for reliability and a vast supply of non-standard bearings.
According to the requirements of this exclusive project, SMB Bearings suggested and supplied EZO thin-type precision bearings.
"The EZO thin-type precision bearings we provide have such accuracy as a result of EZO’s advanced manufacturing techniques and quality control," explained Chris Johnson, managing director at SMB Bearings. "If every bearing that comes off the production line is not the same shape and size every time, then the accuracy of the robot joint positions and overall behavior would be compromised."
With the help of SMB Bearings and using a small sample of the EZO thin-type precision bearings, the research and development team at the Shadow Robot Company experimented with various grease levels to find the optimal grease fill.
As robotic movements need to be accurate and predictable, some friction is important to ensure this control. A method of testing and trial and error established the correct friction coefficient and its corresponding percentage grease fill for optimum performance. SMB bearings then provided the complete amount of bearings required to this exact specification.
"These bearings were very easy to install in our Smart Grasping System™," said Luke Moss, robot engineer at the Shadow Robot Company. "This is a direct result of the quality, tolerance and consistency of these bearings, something that is essential for repeated assembly and high precision across multiple robots. Additionally, as the essential core to the lifespan of any robot, we expect these bearings to outlive most other parts of the Smart Grasping System™."
Created to be different from the regular graspers on the market, the Smart Grasping System is still under development, but eventually will have integrated “smart” intelligence, enabling it to pick up many types of objects, and thus reducing the need for multiple hands in a factory.
Moreover, torque sensing on each joint will allow the Hand to make the most accurate and dependable grasp of whatever object it picks up.
Industry 4.0 is on everyone's lips at the minute, but we can't forget the basics. Bearings may not be considered smart, but if they enable the reliability and robustness of smart systems such as this Smart Grasping System™, then I guess that is as close to being smart as a bearing can get.
Chris Johnson, SMB Bearings
“I’m calling it transformative, because I know it will transform the manufacturing industry," added Rich Walker, managing director at the Shadow Robot Company.
"When companies have deployed robots in the past, they’ve used grippers that were designed to perform one function, so you get a robot that performs one function. The modern manufacturing industry needs more flexibility than this, and the Smart Grasping System™ will address this need."
The need for manufacturers to keep investing in new grippers for various tasks will be reduced by the Smart Grasping System™. Changing machinery is time-consuming and very costly. Equally, having several robots carrying out a single task is extravagant in terms of both floor space and capital costs.
Jointly, the Shadow Robot Company and SMB Bearings are working on finding a solution to this real-world manufacturing problem, freeing up floor space for a more efficient production line.
Remember the Amazon Picking Challenge mentioned earlier? The Shadow Robot Company sets its own picking challenge, using objects from Amazon's challenge as well as others, to test the Smart Grasping System™. The Smart Grasper recognized and grasped these objects easily, demonstrating the success of high precision bearings and smart engineering, to provide the manufacturing industry with what it is in desperate need of.
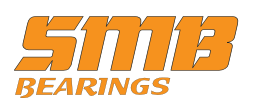
This information has been sourced, reviewed and adapted from materials provided by SMB Bearings.
For more information on this source, please visit SMB Bearings.