In the Consumer Electronics Show (CES) 2017, the industry’s vision of the future was showcased, highlighting a fascinating consumer trend towards robot personal assistants. Inspired by the show, Chris Johnson, managing director of precision bearings provider SMB Bearings, details what design engineers, a well as customers specifying a robot, needs to know about thin section bearings.
Those who visited CES this year encountered a humanoid robot, Lynx, which is powered by the Ewaybot MoRo, and Amazon’s Alexa, designed for helping around the house. While the concept of personal robots assisting with housework appears to be fascinating, there is still a long way to go before this technology can be effective and affordable enough to be developed on a large scale.
Nonetheless, the accuracy and precision required of consumer robots has become possible owing to the research and development performed in industrial automation, especially in the past 10 years.
Robots are carrying out increasingly complex and precise tasks, more easily and faster than ever before, from production and packaging to surgery. In operating theatres, robots, some of them using EZO brand bearings, can now perform complicated surgery with radically reduced impact on patients, enhancing recovery time.
On the factory floor, automatic guided vehicles and collaborative robots are breaking barriers that have traditionally limited automation and are beginning to be used in the open alongside people. For instance, Sapporo Precision is now delivering EZO bearings to producers of a newer branch of robotics.
Robotic exoskeletons are allowing social care workers to lift people and warehouse workers to lift heavier weights with considerably reduced risk of injury. In the food industry, robots are presently being used in production environments, as well as palletizing and packaging, indicating that the sector has genuinely evolved.
These developments have been enabled through advancements in motor, actuator, bearing and sensor technology as well as communications and software. Although steel and hybrid chrome bearings, slewing bearings, and ceramic bearings are all common in robot applications, thin section bearings are the option most commonly selected by SMB Bearing’s customers.
Not only do thin section bearings deliver improved efficiency, high levels of accuracy, and higher speed, they also have reduced friction and impressive design flexibility. As there is only a slight difference in size between the external and internal ring, they also lower the weight and bulk of an application, making them a perfect choice for robotics, where both weight and footprint are premium items.
However, meticulous attention has to be paid to the roundness of the ring itself, considering how thin it is. If a thin section bearing is used without any lubricant and the inner ring is rotated, a light squeeze of the outer ring between thumb and finger will halt the bearing in its tracks, owing to the incredible flex in the device.
Consequently, the manufacturing process has to be extremely precise to guarantee the highest possible degree of roundness in both rings, in addition to good noise levels in the bearing itself.
This will generally require fine grinding and machining, complimented by a very high level of quality in the process as well as the raw materials. In case the rings are not completely formed, even a slight discrepancy prevent the bearing from running smoothly, which in turn produces excess noise.
For instance, the EZO range of thin section bearings is produced to such a high standard that every single item that comes off the production line is tested seperately. Even if a minor deficiency is found, it is rejected. This means one can be confident that the millionth bearing produced is as high in quality as the first.
These thin-section ball bearings can be supplied sealed, shielded, or open in 440 grade stainless steel or SAE52100 chrome steel and are designed to endure both radial loads and moderate thrust loads in both directions. Some of the smaller thin-section bearing sizes are available with a fiberglass reinforced nylon high-speed synthetic retainer.
A low torque, free turning and low noise grease should be selected, such as those used as a standard in the EZO bearings re-sold in the UK by SMB Bearings. A grease that is too stiff will not deliver the best results as it could increase the bearing torque to unacceptable levels for a thin-section bearing.
A grease with a wide temperature range, possibly from -40 °C to +150 °C would be ideal. This enables a variety of applications in which a robot can almost certainly be used, from refrigeration to conditions close to those of a furnace. A food grade grease should be selected in case the robot is to be employed in food or beverage production or packaging.
The correct choice of grease will lead to a free running bearing, which will consequently lower the power consumption of the machine itself and the long-term maintenance costs. It is also one of the factors that can contribute to the overall speed of the robot arm.
While it may take some time before humanoid robots are spring cleaning our houses, it does seem likely that their impact on industry will continue to increase rapidly. The technology presented at CES, which evidently draws on developments from the industry, acts as strong evidence for the continued march of the robots.
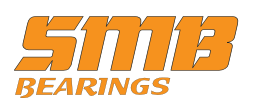
This information has been sourced, reviewed and adapted from materials provided by SMB Bearings.
For more information on this source, please visit SMB Bearings.