Sep 17 2014
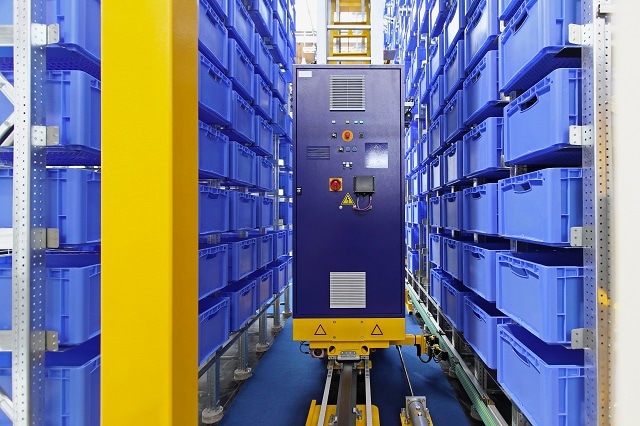
Automated handling vehicles or automated guided vehicles or AGVs are instrumental in improving efficiency and reducing costs by helping in the automation of a warehouse or a manufacturing facility.
Barrett Electronics invented the first AGV in 1953. AGVs are capable of towing objects in trailers and the trailers can be used for moving raw materials or the finished product. Objects can be stored on a bed by the AGV. It is possible to place the objects on motorized rollers and push them off by reversing them. AGVs are used in almost all industries including paper, pulp, newspaper, metals and general manufacture.
The technology has gradually become more advanced and in an automated process, LGVs communicate with other robots to make sure that the product moves smoothly through the warehouse, whether it is directly transferred to the shipping area or whether it is stored for future use.
Design of Automated Handling Vehicles
AGVs are designed to automatically transfer objects or goods between different locations. The different designs of AGVs include the following:
- A wired sensor is placed at the robot bottom and placed ground-facing. A wire is arranged around 1 inch below the ground in a slot cut in the ground. The radio frequency transmitted from the wire is detected by the sensor and the sensor is guided by the radio frequency.
- Guide Tape AGVs also called automated guided carts or AGCs use tape as the guide path. The tapes may be colored or magnetic. The AGC is fixed with the right guide sensor in order to follow the tape path. Another advantage of tape over wire guidance is that it can be removed easily and relocated in case there is a need to change. It is also possible to embed a flexible magnetic bar in the floor like wire that works similar to magnetic tape and remains passive or unpowered. Dual polarity is another benefit of magnetic guide tape. One may place tiny magnetic tape pieces to change states of the AGC based on sequence and polarity of the tags.
- Laser target navigation is done by mounting tape on poles, machines or walls. The AGV has a laser transmitter and receiver on a rotating turret. The laser is sent, then received again and the distance and angle are calculated automatically and stored in the memory of the AGV. The AGV has a reflector map stored in memory and its position can be corrected based on errors between the received and expected measurements. Using the constantly updating position, it can move to a destination target.
- Using modulated laser light, better range and accuracy are offered when compared to pulsed laser systems. A continuous fan of modulated laser light enables the system to obtain an uninterrupted reflection as soon as the scanner achieves line of sight using a reflector.
- AGV guidance is also done using inertial navigation. In this method, a computer control system directs and assigns tasks to vehicles. The workplace floor is embedded with transponders. These transponders are used by the AGV to check if the vehicle is on course. A gyroscope can determine the slightest change in the vehicle direction and the same is corrected to keep the AGV in its path.
Functioning of an Automated Handling Vehicle
The AGV is navigated using two different steer control systems. The most common is differential speed control. Here, two sets of wheels are being driven. Each set is connected to a common drive train. These drive trains are driven at different speeds so as to turn or the same speed to enable the AGV to move forwards or backwards.
Steered wheel control AGV is one wherein the steering is similar to that of a car. This has a smooth turning but sharp turns cannot be made at tight spots. In most applications, steered wheel control AGVs are used.
Vision-guided AGVs use cameras to record features in the route so that the route can be replayed during navigation. These AGVs use evidence grid technology, which is a probabilistic volumetric sensing application. 360 degree images are used to build a 3D map enabling the vision-guided AGVs to follow a trained route without human assistance or by adding special features, positioning systems or landmarks.
Advantages of Automated Handling Vehicles
Benefits of automated handling vehicles are:
- Accurate and safe operation
- Routes remain unchanged over a period of time
- It can operate round-the-clock without any human intervention
- There is no need for any conventional material handling infrastructure
- As the business grows, the number of AGVs can be increased
- It is possible to upgrade the system without shutting down operations
- AGVs in use share work flow efficiently and dynamically between them
- Just-in-time delivery, accurate inventory management and no destination errors
- Low running and maintenance costs
- Is compatible with any kind of automation
- Effective optimization of transport flow based on the vehicle fleet available, transport mission and traffic conditions.
References and Further Reading