Apr 25 2019
To create a microrobot, one used to require a microscope, two needle-nosed tweezers, steady hands, and a minimum of eight hours. But currently, scientists from the University of Toronto Engineering have formulated a technique that requires just a 3D printer and 20 minutes.
MASc student Tianqi Xu holds up a microrobot that was fabricated using their automated system. (Photo credit: Liz Do)
In the lab of Professor Eric Diller (MIE), scientists build magnetized microrobots — the size of a pin head — that can move through fluid-filled vessels and organs within the human body. Diller and his team regulate the microrobots’ motion wirelessly using magnetic fields.
Each microrobot is constructed by precisely positioning microscopic sections of magnetic needles over a flat, flexible material. Once set up, the scientists apply magnetic fields to prompt the microrobots to move with worm-like motion via fluid channels, or close its miniature mechanical “jaws” to procure a tissue sample.
“These robots are quite difficult and labour-intensive to fabricate because the process requires precision,” says Tianqi Xu (MIE MASc candidate). “Also because of the need for manual assembly, it’s more difficult to make these robots smaller, which is a major goal of our research.”
That is why Xu and his labmates formulated an automated method that considerably reduces design and development time, and expands the varieties of microrobots they can produce. Their results were published recently in Science Robotics.
Smaller and more complex microrobots are required for future medical applications, such as assisted fertilization, targeted drug delivery, or biopsies.
“If we were taking samples in the urinary tract or within fluid cavities of the brain — we envision that an optimized technique would be instrumental in scaling down surgical robotic tools,” says Diller.
To prove the capabilities of their new method, the scientists developed over 20 different robotic shapes, which were then preset into a 3D printer. The printer then constructs and solidifies the design, positioning the magnetically patterned particles as part of the process.
Previously, we would prepare one shape and manually design it, spend weeks planning it, before we could fabricate it. And that’s just one shape. Then when we build it, we would inevitably discover specific quirks — for example, we might have to tweak it to be a little bigger or thinner to make it work.
Eric Diller, Professor, Department of MIE, University of Toronto Engineering.
“Now we can program the shapes and click print,” adds Xu. “We can iterate, design and refine it easily. We have the power to really explore new designs now.”
The researchers’ enhanced method paves the way for creating even smaller and more intricate microrobots than the present millimeter-size. “We think it’s promising that we could one day go 10 times smaller,” says Diller.
Diller’s lab plans to apply the automated process to study more advanced and complicated shapes of microrobots.
As a robotics research community, there’s a need to explore this space of tiny medical robots. Being able to optimize designs is a really critical aspect of what the field needs.
Eric Diller, Professor, Department of MIE, University of Toronto Engineering.
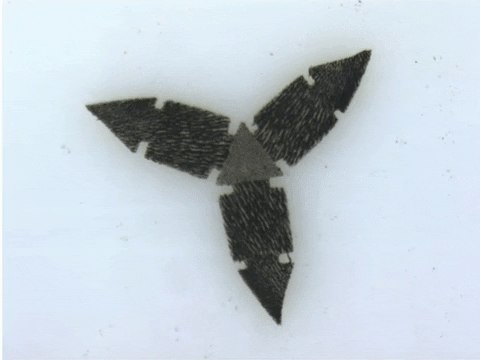
A microrobot with gripping-jaw, cargo-carrying capabilities. (Courtesy of Tianqi Xu)