The usage of additive manufacturing, often known as 3D printing, is a prominent innovation creating waves in the automation business. Additive manufacturing, like other forms of manufacturing technology, is evolving and may therefore be employed in a wide variety of applications and functions. This article discusses the relevance, workings, benefits, and industrial breakthroughs in additive manufacturing, notably for the automation industry.
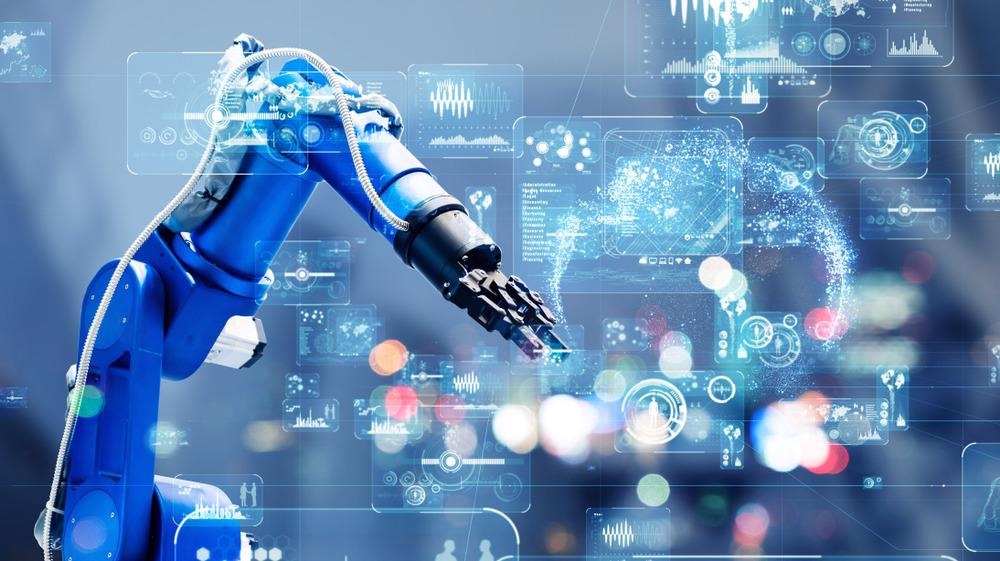
Image Credit: metamorworks/Shutterstock.com
What is Additive Manufacturing?
3D printing, also known as additive manufacturing (AM) or additive layer manufacturing (ALM), is a computer-controlled technology for creating three-dimensional objects by layering materials.
Employing computer-aided design (CAD) or 3D object sensors, additive manufacturing allows for creating products with precise geometric characteristics. In contrast to traditional manufacturing, which often requires grinding or other operations, the products are built layer by layer.
In the 1980s, additive manufacturing was used to construct prototypes that were rarely functional. As additive manufacturing advanced, its uses expanded to include fast prototyping, which was used to create molds. Since the early 2000s, additive manufacturing has been utilized to create highly functional items.
How Does Additive Manufacturing Work?
The design of an item must be finalized before employing additive manufacturing to manufacture it.
This is primarily accomplished by scanning the object to be printed or by using computer-aided design (CAD) software. After that, the design is turned into a layer-by-layer framework. This is sent to the 3D printer, which immediately begins work on the object. Polymers, metals, and ceramics are among the materials utilized in additive manufacturing, as are foams, gels, and even biomaterials.
Although other methods of additive manufacturing exist, sintering and stereolithography are the most often employed in the automation sectors. Sintering is the process of heating material without dissolving it to create complex, high-resolution objects.
In selective laser sintering, a laser is used to attach thermoplastic particles together, while direct metal laser sintering utilizes metal powder.
Stereolithography utilizes a photopolymerization technique in which an ultraviolet laser is fired into a vat of liquid resin to fabricate torque-resistant and temperature-resistant ceramic components.
Additive Manufacturing: The Future of Automation Industries
Additive manufacturing (AM) provides a huge competitive edge in automation industries such as robotics and automobiles, acting as a disruptive strategy by shortening manufacturing time, increasing operational flexibility, and offering optimal automobile parts and custom-designed vehicle products on demand.
The automobile industry is one of the most demanding sectors on the globe. To stay up with the vehicle industry, new market trends emerge on a regular basis, requiring the adoption of automated manufacturing systems.
Using additive manufacturing on soft assembly tools or advanced machinery to create automobile components accelerates automotive productivity.
Additive manufacturing methods may also aid with robot prototype, tooling, and production, which reduces costs and time and assists robotics engineers meet their aims and goals.
The integration of 3D printing methods with industrial robots is being investigated as a response to the rising requirement for manufacturers to construct massive products in bulk and with accuracy while also automating the manufacturing process.
Advantages of Additive Manufacturing for the Automation Industries
As there is minimal setup and no tooling necessary, additive manufacturing produces prototypes and short-run products far quicker than conventional production, which may assist with both innovation and speed to market. If facilities employ additive manufacturing to generate replacement parts and tools, they may need less inventory space and administration to maintain these goods on hand. This has the potential to cut overhead and recurring resource expenses.
The additive method only utilizes the material required to build the shape of the item. In contrast, subtractive manufacturing requires producers to pay for the raw materials from which component is subsequently taken, which must then be managed and destroyed appropriately.
Recent Industrial Advancements in Additive Manufacturing
Additive manufacturing technology is not new to the automation sectors, as seen by the recent surge in activity in this subject.
Volkswagen (VW) toolmaking division launched an additive manufacturing facility in 2018. VW is investigating the possibilities of binder jet 3D printing for prototyping and tool manufacturing, with the goal of introducing additive manufacturing for end-use component production in the coming years.
VW has also used 3D printing to reduce the weight of systems in production models, such as water connections for the Audi W12 engine.
The researchers at Midwest Engineered Systems Inc. (MWES) in Waukesha, Wisconsin, are employing laser additive printing to construct complex metal components that would otherwise be exceedingly difficult, if not impossible, to fabricate.
The technique is driven by a six-axis articulated robot that uses hot wire deposition and a laser to create metal pieces layer by layer on an existing platform. Exotic elements are deposited precisely and quickly to create prototypes and small quantities of high-value complicated items.
Future Perspective on Importance of Additive Manufacturing
In the coming years, additive manufacturing is likely to become the main mass-production approach. The present progress of additive manufacturing has already outpaced the projections provided in prior research. Renowned research institutes believe that 3D metal printing will play a growing role in mechatronics, robotics, and toolmaking.
The entire automation and digitized processing that additive manufacturing allows will eventually replace large volume, serial production processes. The goal is for additive manufacturing to become quick and accurate enough for mass production.
Currently, additive manufacturing capabilities contend with CNC-controlled machines, which are still more suited for serial production. The long-term objective is for 3D metal printing of complicated items to eventually replace CNC equipment.
References and Further Reading
Anandan, T. M. (2017, October 26). Building the Future with Robotic Additive Manufacturing. From Association for Advanced Automation: https://www.automate.org/industry-insights/building-the-future-with-robotic-additive-manufacturing
Ashima, R. et al. (2021). Automation and manufacturing of smart materials in additive manufacturing technologies using the Internet of Things towards the adoption of industry 4.0. Materials Today: Proceedings. Available at: https://doi.org/10.1016/j.matpr.2021.01.583
ATS inc. (2022). The Value of Additive Manufacturing in The Automotive Industry. From Advanced Technology Services Inc.: https://www.advancedtech.com/blog/automotive-additive-manufacturing/
Haleem, A., & Javaid, M. (2019). Additive Manufacturing Applications in Industry 4.0: A Review. Journal of Industrial Integration and Management. Available at: https://doi.org/10.1142/S2424862219300011
Vasco, J. C. (2021). Additive Manufacturing. Elsevier. Available at: https://doi.org/10.1016/B978-0-12-818411-0.12001-4
Disclaimer: The views expressed here are those of the author expressed in their private capacity and do not necessarily represent the views of AZoM.com Limited T/A AZoNetwork the owner and operator of this website. This disclaimer forms part of the Terms and conditions of use of this website.