Mobile robots capable of both ground and airborne locomotion are few and far between. A few robots can also undertake complicated locomotion tasks that go beyond the simple skills of walking or flying. A double mechanism robot has been developed and named LEONARDO or LEO, which is an acronym of 'LEgs ONboARD drOne'.
Leonardo: The Skateboarding, Slacklining Robot
Video Credit: caltech/YouTube.com
The robot's two locomotion systems, multi-joint legs and propeller-based thrusters, give it the ability to move both on land and in the air and walk and fly in one action.
With LEO, the researchers hoped to do two things: first to develop flying and walking robotic locomotion capabilities; and second, to examine how such a hybrid robotic platform's design, dynamics, and control issues are affected by the use of synchronous propeller and articulated joint control.
Advantages and Limitations of Ground and Aerial Robots
Human-like body forms and their ability to walk, run, and jump over a variety of different terrains, bipedal robots, in particular, have gotten a lot of interest.
The presence of impediments of varying sizes makes it difficult for ground robots to move safely. As a result, they can only be used in well-organized settings, such as by interior service robots.
Aerial robots that can fly over barriers of any size or on any ground have been a major focus of research in the robotics world in the past few years. Despite their potential for real-world use, these robots have several disadvantages, including high energy consumption, short flight and operation times, and a lack of available onboard resources and payload weight.
Integrated Approach
Multi-modal robots provide advantages over robots with only one mode of locomotion, such as navigating difficult areas by switching between possible ways of movement.
The practical implementation of multi-modal locomotion robots has proven to be difficult. For example, mechanical design, modeling, analysis, and control system design are only some of the study concerns that need to be addressed to reach a conclusion.
When standing, LEO weighs 2.58 kilograms and stands 75 centimeters tall. A torso, propeller propulsion system, and two legs with point feet make up the basic structural elements of LEO. LEO can function autonomously using its onboard processors and sensor arrays.
LEO has four propellers on each of its shoulders, which are used to stabilize and control both walking and flying.
The controllability of balancing and walking motions is improved by increasing the propeller's moment about the ground contact using the propeller thrust forces by tilting them inwards. Additionally, LEO's torso holds onboard computers, sensors, and two lithium polymer (LiPo) batteries for supplying the system's energy requirements.
Methods Used in Developing LEO
Kinematics and dynamics models have been used to work on and implement trajectories and different strategies for transition between walking and flying are used. There are several important technical methods that are used to integrate the two system dynamics in LEO:
- Walking phase of LEO using inverted pendulum model
- Linear IP model for walking trajectory
- Propeller controller through IP modeling
- Non-linear tracking of controller for walking phase
- Optimized control allocated for walking phenomenon
- Transition phase and flight controller
- Constrained and unconstrained moment sets
- Torse orientation estimation
Design Trade-Off
Continuously running propellers are required to achieve LEO's great balance; however, this results in higher energy consumption than robots with only their legs.
To keep LEO's weight as low as possible while maintaining its flying performance, the development team decided to employ low-power leg servo motors and flexible, lightweight legs.
However, its cost of transportation (CoT) has been kept as the main feature, which measures how efficient a vehicle is at getting around.
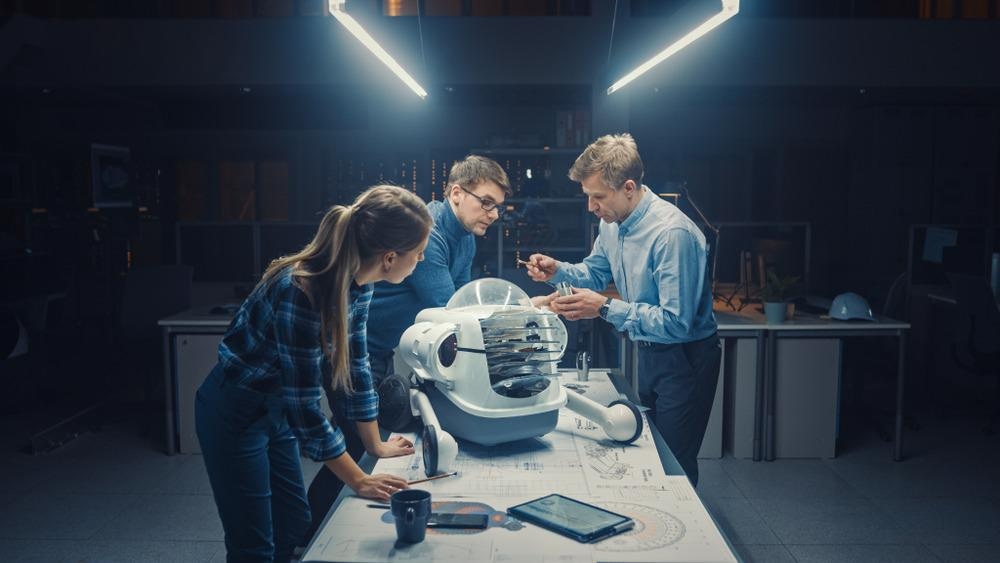
Image Credit: Gorodenkoff/Shutterstock.com
Future Developments of Leo and Other Mobile Robot Designs
Various design trade-offs can be made to improve energy efficiency. A more rigid LEO, for example, would require less push to keep its legs from deforming.
LEO might also walk with less assistance from the propellers by using finite feet for better stability or higher power motors with torque control for joint actuation, allowing for fast and accurate tracking of foot position to stabilize the gait.
Only when the legs lose their balance on the ground may propellers be activated, rather than running continually. Weight gain and increased energy consumption during flight maneuvers would be the consequences of these strategies, while energy consumption while walking would be reduced.
By combining aerial and bipedal locomotion in a single system, LEO aspires to fill a need left by current robots' lack of integration. LEO is designed to carry out various activities that are difficult for ground robots to access.
Compared to a typical multirotor, LEO makes better use of the ground contact and is more robust to disturbances like the wind. LEO's major use case could be multipoint inspection, repair, or replacement at difficult-to-reach areas. Inspection of high-voltage lines is an example.
Continue reading: Artificial Muscles Enhance the Performance of Flying Microrobots.
References and Further Reading
F. J. Boria, R. J. (2005). A sensor platform capable of aerial and terrestrial locomotion. IEEE, (pp. 3959-3964). https://ieeexplore.ieee.org/document/5354102
Kim, K., Spieler, P., Lupu, E., Ramezani, A. and Chung, S., (2021) A bipedal walking robot that can fly, slackline, and skateboard. Science Robotics, 6(59). https://doi.org/10.1126/scirobotics.abf8136
Daler, L., Lecoeur, J., Hahlen, P. and Floreano, D., (2013) A flying robot with adaptive morphology for multi-modal locomotion. 2013 IEEE/RSJ International Conference on Intelligent Robots and Systems,. https://ieeexplore.ieee.org/abstract/document/6696526
M. Kovač, J.-C. Z. (2009). Towards a Self-Deploying and Gliding Robot. In Flying Insects and Robots (pp. 271-284). https://infoscience.epfl.ch/record/130146?ln=en
Richard J. Bachmann, R. V. (2009). Drive train design enabling locomotion transition of a small hybrid air-land vehicle. Proceeding of IEEE, (pp. 5647-5652). St Louis. https://ieeexplore.ieee.org/document/5354102
Disclaimer: The views expressed here are those of the author expressed in their private capacity and do not necessarily represent the views of AZoM.com Limited T/A AZoNetwork the owner and operator of this website. This disclaimer forms part of the Terms and conditions of use of this website.