Soft robots offer multiple benefits like dexterous movement, adaptative abilities, and very high security for performing detection and exploration work in cluttered, constrained, and uncharted spaces.
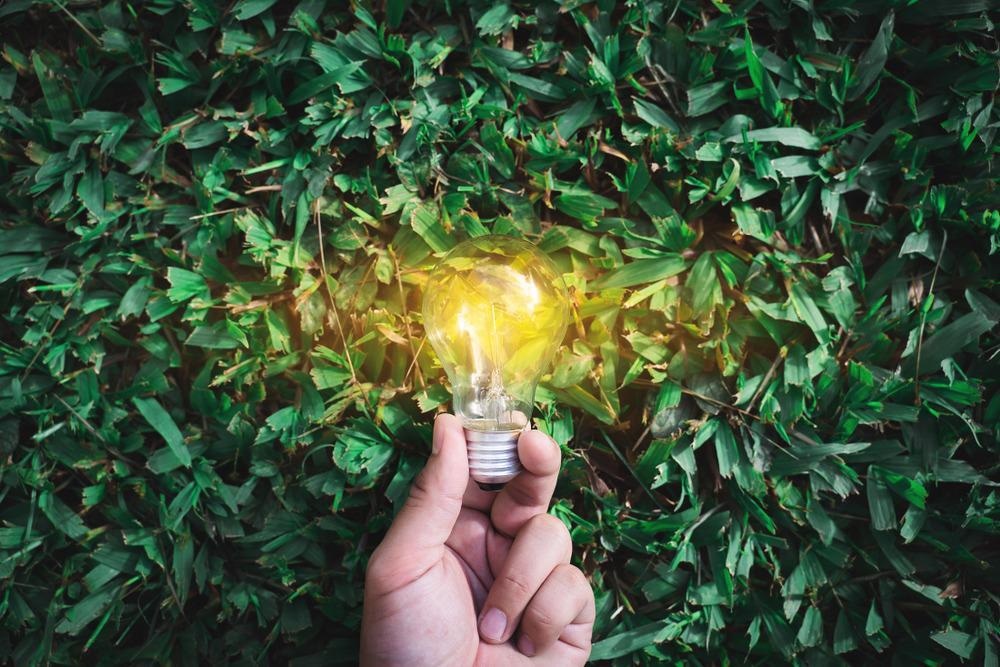
Image Credit: one photo/Shutterstock.com
Although various types of soft robots exist, soft continuum robots developed using the principle of vine growth have gained significant attention as they can offer certain unique benefits. These relate to independent movement within environments, flexible systems that can mitigate damage, as well as the potential to expand the surrounding workspace.
Due to the continuum nature of these robots, motion is limited to relatively simple path planning, which restricts the ability to utilize these robots in complex, dynamic environments.
Overcoming these challenges is a major focus in improving the movement controllability of soft robots.
Building on previous designs that model the growth system of vines, researchers have devised a control system for soft continuum robots that aids on-demand active steering abilities. In doing so, the team hopes that such robots can adapt to dynamic environments, evading potential objects and threats more quickly. Their research was published in the journal Research.
It was important to develop a control system as vines do not possess one, much like animals.
Methodology
The inspiration for a tip-extending and signal-controlling soft robot comes from the vine growth system. The eversion motion that arises from the tip and the asymmetric growth due to the electromagnet units in the movement system mimics the motion of natural vines to evade obstacles and track the target.
At the same time, due to the centralized management and decoupling control of the steering actuators found in the control system, the motion is complicated yet coordinated. Thus, as illustrated in Figure 1, this study proposes a bioinspired soft robot that integrates a coordinated control system with the growth adaptability of vine plants.
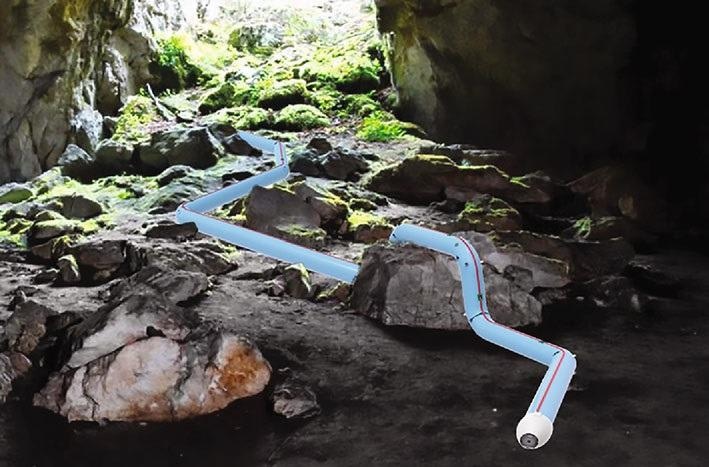
Figure 1. The conceptual design of the bioinspired soft robot. Image Credit: Li, et al., 2021
Figure 2(a) illustrates the design of the robot, including a backbone and four arrays of electromagnet units distributed evenly in the cross-section at 90°. As illustrated in Figure 2(b), the robot includes two distinct turning modes that enable steering in eight directions in space.
An active continuous steering process that helps complete spatial path planning is illustrated in Figures 2(c)–2(f). The effect of the electromagnet’s size on its flexibility was reported as negligible with respect to the robot body. Figure 2(g) illustrates the working process of the control system.
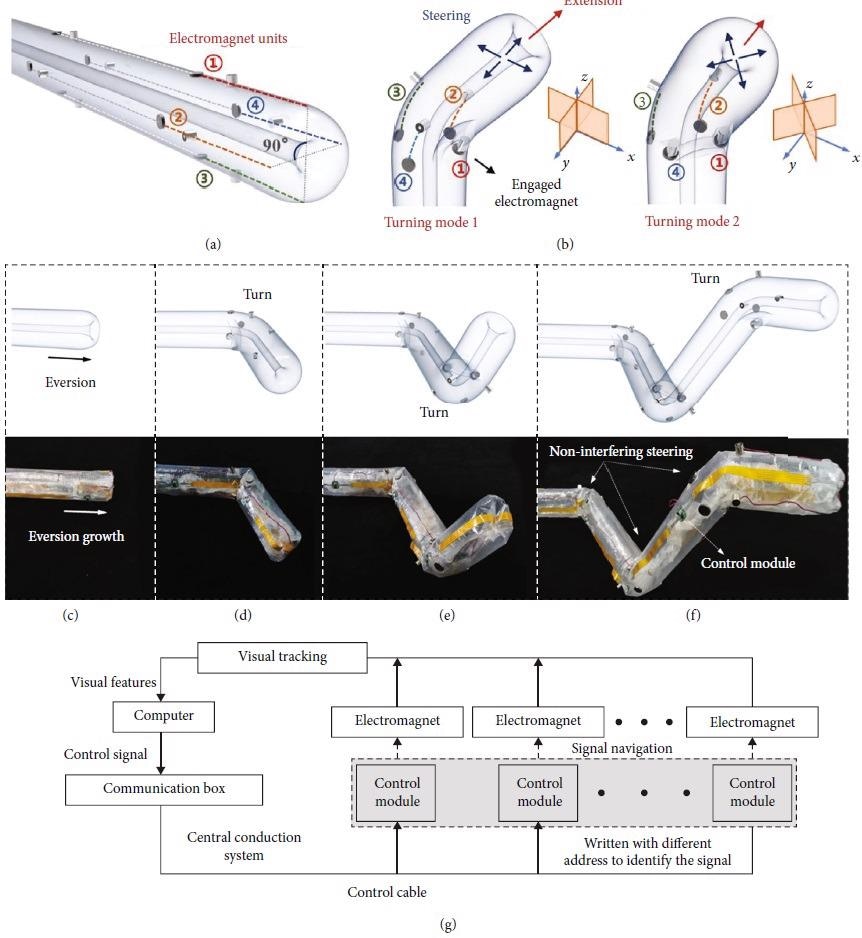
Figure 2. Principle of design and control for continuous steering. (a) Four series electromagnet units are uniformly distributed at 90° along the body of the soft robot. (b) The electromagnet units release the stored body to make the asymmetric lengthening, and the steering can be held by one electromagnet unit such as ① or two adjacent electromagnets such as ① and ④, corresponding to two different turning modes. (c) The robot is in a state of waiting for growth. (d) The electromagnets release the stored body through turning mode 1 and the robot steers to right. (e) Using turning mode 2, the robot steers upward. (f) The robot turns again to create three noninterfering steering at the spatial level. (g) Control block diagram of the robot. Image Credit: Li, et al., 2021
Results
The kinematic model of steering was verified by setting five different lengths of the robot body in the electromagnet unit, thus creating five respective angles. Measurement errors in the experiment were eliminated by using a protractor to quantify the steering angle of the turning body axis five times and estimating the average value.
The robot's motion under the target navigation system’s control allows the robot to complete complex path planning in a highly coordinated way. The transition process of the initials of “Soft Robot” from S to R is illustrated in Figure 4(a) for a single soft robot.
Figure 4(b) shows a dynamic finite element model created to study the crawling motion of the spatial steering robot on the stairs.
The main robot body's displacement change slowly reduces from the apex to the initial position, following the original motion of the continuous eversion growth induced by air pressure, as shown in Figure 4(b).
The spatial motion of the soft robot concerning avoiding obstacles, climbing stairs, and reaching the target on a different working plane is illustrated experimentally in Figure 4(c).
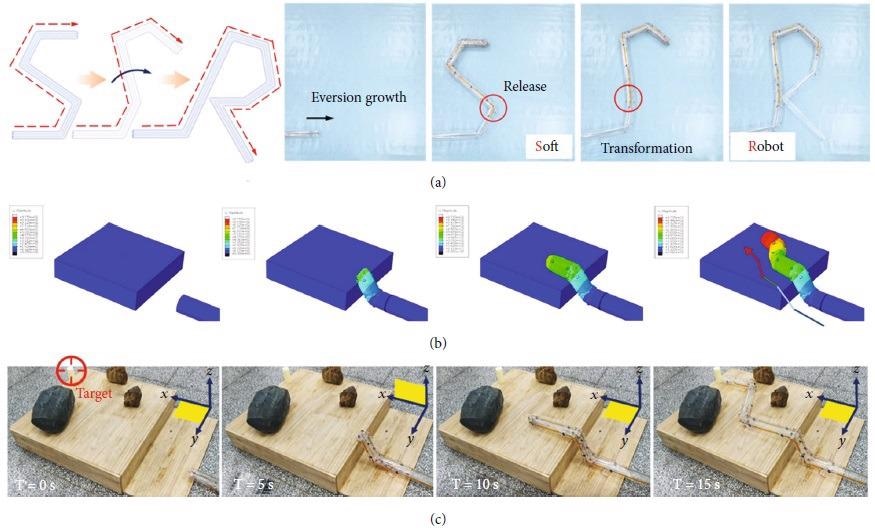
Figure 4. Simulation and demonstrations of models. (a) The deformation process of the initials “Soft Robot” from S to R. (b) The motion simulation of the soft robot to climb the steps to change the working plane. (c) Actual motion demonstration corresponding to simulation. The robot reaches the step and turns upward to climb on the step with multiple obstacles, after changing the work plane, the robot plans the path on the new plane to avoid all obstacles and finally reaches the target. Image Credit: Li, et al., 2021
The ability of the soft robot to serve as a carrier for detection and disinfection in dynamic, restricted environments is demonstrated in Figure 5.
Figure 5(a) illustrates the movement of the soft robot inside a pipeline to perform disinfection, where the robot’s length is greater than 5 m. Figure 5(b) shows how the robot executes detection in a multi-obstacle, restricted space.
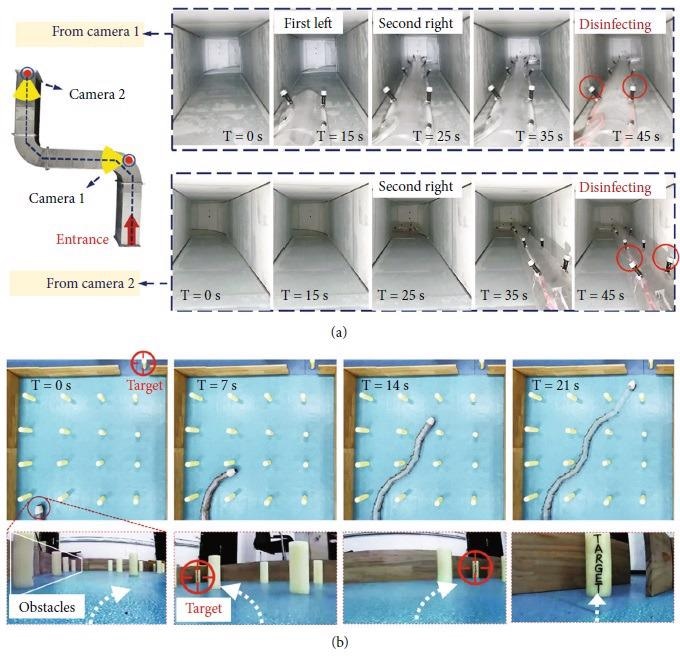
Figure 5. The pipeline disinfection by soft robot and the detection experiment in multi-obstacle environment. (a) The robot attached with two series of sterilizing nozzles enters the ventilation pipeline for disinfection. T = 15 seconds, the robot steers left at the first bend of the pipeline and steers right at the second at T = 25 seconds to comply with the tortuous path of the pipeline; T = 35 seconds, the robot runs through the pipeline, and then, the disinfecting valve is opened to disinfect at T = 45 seconds without missing any corner. (b) The soft robot navigates to the target by using a camera at the tip. T = 0 seconds, the left side of the view is full of obstacles, so the robot turns right to avoid; T = 7 seconds, the camera finds that the target is located to the left of the view, so it steers left; T = 14 seconds, the target is to the right and it steers right to approach to; while the target is in the center of the view, the robot completes the path selection and reaches the target at T = 21 seconds. Image Credit: Li, et al., 2021
Here, the soft robot reaches the given target using real-time path selection.
A camera fitted on the apex of the soft robot feeds the characteristics of the space back to the computer to enable visual sensing. The robot is powered by consecutive steering to continuously search for the target while turning beforehand to evade obstacles that come in the viewing range of the tip camera.
The apex of the robot is controllable and highly flexible, thus realizing detection without any contact with the environment. This ensures reliable adaptation to restricted environments that contain different obstacles, like overheated or sharp objects, with the potential to damage the body of the soft robot.
Conclusion
This study put forth an innovative bioinspired soft continuum robot, with several degrees of freedom in all three dimensions that integrates a coordinated control system with the growth adaptability of vine plants.
The robot features a multi-joint space steering design and achieves the simultaneous control of multiple joints with shorter response time and better reliability for the steering process.
The robot was demonstrated to offer high benefits in long-distance active consecutive steering with the help of electromagnet steering units. It also exhibited high controllability by completing highly complex path planning.
It could also carry operational tools, like a camera, on the apex in constrained spaces for disinfection of ventilation pipeline and multi-obstacle detection. These results not only contribute to the design of vine-inspired robots, but also lay the groundwork for potential applications in post-disaster rescue, equipment maintenance and environmental sensing.
In the future, the team hopes to improve controllability and growth even further.
Continue reading: Assembling the Foundations of Soft Robot Systems with Worm Blobs.
Journal Reference:
Li, P., Zhang, Y., Zhang, G., Zhou, D., Li, L. (2021) A Bioinspired Soft Robot Combining the Growth Adaptability of Vine Plants with a Coordinated Control System. Research. Available online: https://doi.org/10.34133/2021/9843859.
References and Further Reading
- Rus, D L & Tolley, M T (2015) Design, fabrication and control of soft robots. Nature, 521(7553), pp. 467–475. doi.org/10.1038/nature14543.
- Neppalli, S., et al. (2007) Octarm-a soft robotic manipulator. In: 2007 IEEE/RSJ International Conference on Intelligent Robots and Systems, pp. 2569–2569, San Diego, CA, USA. doi.org/10.1109/IROS.2007.4399146.
- Mehling, J. S., et al. (2006) A minimally invasive tendril robot for in-space inspection. In: The First IEEE/RAS-EMBS International Conference on Biomedical Robotics and Biomechatronics, 2006. BioRob 2006, pp. 690–695, Pisa, Italy. https://doi.org/10.1109/BIOROB.2006.1639170.
- Talas, S. K., et al. (2020) Design and development of a growing pneumatic soft robot. Soft Robotics, 7(4), pp. 521–533. doi.org/10.1089/soro.2019.0083.
- So, J., et al. (2021) Shape estimation of soft manipulator using stretchable sensor. Cyborg and Bionic Systems, 2021(9843894), pp. 1–10. doi.org/10.34133/2021/9843894.
- Jian, Y., et al. (2019) Antifreezing and stretchable organohydrogels as soft actuators. Research, 2019(2384347), pp. 1–11. doi.org/10.34133/2019/2384347.
- Walker, I D (2015) Biologically inspired vine-like and tendril-like robots. In: 2015 Science and Information Conference (SAI), pp. 714–720, London, UK. doi.org/10.1109/SAI.2015.7237221.
- Hawkes, E. W., et al. (2017) A soft robot that navigates its environment through growth. Science Robotics, 2(8), article eaan3028. doi.org/10.1126/scirobotics.aan3028.
- Hammond, Z. M., et al. (2017) Pneumatic reel actuator: design, modeling, and implementation. In: 2017 IEEE International Conference on Robotics and Automation (ICRA), pp. 626–633, Singapore. doi.org/10.1109/ICRA.2017.7989078.
- Agharese, N., et al. (2018) HapWRAP: soft growing wearable haptic device. In: 2018 IEEE International Conference on Robotics and Automation (ICRA), pp. 5466–5472, Brisbane, QLD, Australia. doi.org/10.1109/ICRA.2018.8460891.
- Blumenschein, L., et al. (2018) A tip-extending soft robot enables reconfigurable and deployable antennas. IEEE Robotics & Automation Letters, 3(2), pp. 949–956. doi.org/10.1109/LRA.2018.2793303.
- Coad, M. M., et al. (2020) Vine robots: design, teleoperation, and deployment for navigation and exploration. IEEE Robotics & Automation Magazine, 27(3), pp. 120–132. doi.org/10.1109/MRA.2019.2947538.
- Gravagne, I. A., et al. (2003) Large deflection dynamics and control for planar continuum robots. IEEE/ASME Transactions on Mechatronics, 8(2), pp. 299–307. doi.org/10.1109/TMECH.2003.812829.
- Webster, R J & Jones, B A (2010) Design and kinematic modeling of constant curvature continuum robots: a review. International Journal of Robotics Research, 29(13), pp. 1661–1683. doi.org/10.1177/0278364910368147.
- Greer, J. D., et al. (2017) Series pneumatic artificial muscles (sPAMs) and application to a soft continuum robot. In: 2017 IEEE International Conference on Robotics and Automation (ICRA), pp. 5503–5510, Singapore. doi.org/10.1109/ICRA.2017.7989648.
- Do, B. H., et al. (2020) Dynamically reconfigurable discrete distributed stiffness for inflated beam robots. In: 2020 IEEE International Conference on Robotics and Automation (ICRA), pp. 9050–9056, Paris, France. doi.org/10.1109/ICRA40945.2020.9197237.
- Tsukagoshi, H., et al. (2011) Smooth creeping actuator by tip growth movement aiming for search and rescue operation. In: 2011 IEEE International Conference on Robotics and Automation, pp. 1720–1725, Shanghai, China. doi.org/10.1109/ICRA.2011.5980564.
- Tsukagoshi, H., et al. (2011) Tip growing actuator with the hose-like structure aiming for inspection on narrow terrain. International Journal of Automation Technology, 5(4), pp. 516–522. doi.org/10.20965/ijat.2011.p0516.
- Jeong, S. G., et al. (2019) A tip mount for carrying payloads using soft growing robots. Available at: https://arxiv.org/abs/1912.08297.
- Gan, L. T., et al. (2020) 3D electromagnetic reconfiguration enabled by soft continuum robots. IEEE Robotics and Automation Letters, 5(2), pp. 1704–1711. doi.org/10.1109/LRA.2020.2969922.
- Ozkan-Aydin, Y., et al. (2019) Nutation aids heterogeneous substrate exploration in a robophysical root. In: 2019 2nd IEEE International Conference on Soft Robotics (RoboSoft), pp. 172–177, Seoul, Korea. doi.org/10.1109/ROBOSOFT.2019.8722717.
- Wang, S., et al. (2020) A dexterous tip-extending robot with variable-length shape-locking. In: 2020 IEEE International Conference on Robotics and Automation (ICRA), pp. 9035–9041, Paris, France. doi.org/10.1109/ICRA40945.2020.9197311.
- Hannan, M W & Walker, I D (2003) Kinematics and the implementation of an elephant’s trunk manipulator and other continuum style robots. Journal of Robotic Systems, 20(2), pp. 45–63. doi.org/10.002/rob.10070.
- Tian, Y., et al. (2017) Kinematic modeling of the constant curvature continuum line drive robot. In: 2016 IEEE International Conference on Robotics and Biomimetics (ROBIO), pp. 289–294, Qingdao, China. doi.org/10.1109/ROBIO.2016.7866337.
- Jones, B A & Walker, I D (2006) Kinematics for multisection continuum robots. IEEE Transactions on Robotics, 22(1), pp. 43–55. doi.org/10.1109/TRO.2005.861458.
- Jones, B A & Walker, I D (2007) Practical kinematics for real-time implementation of continuum robots. IEEE Transactions on Robotics, 22(6), pp. 1087–1099. doi.org/10.1109/TRO.2006.886268.
- Elsayed, Y., et al. (2014) Finite element analysis and design optimization of a pneumatically actuating silicone module for robotic surgery applications. Soft Robotics, 1(4), pp. 255–262. doi.org/10.1089/soro.2014.0016.