Article Updated on 12 April 2021
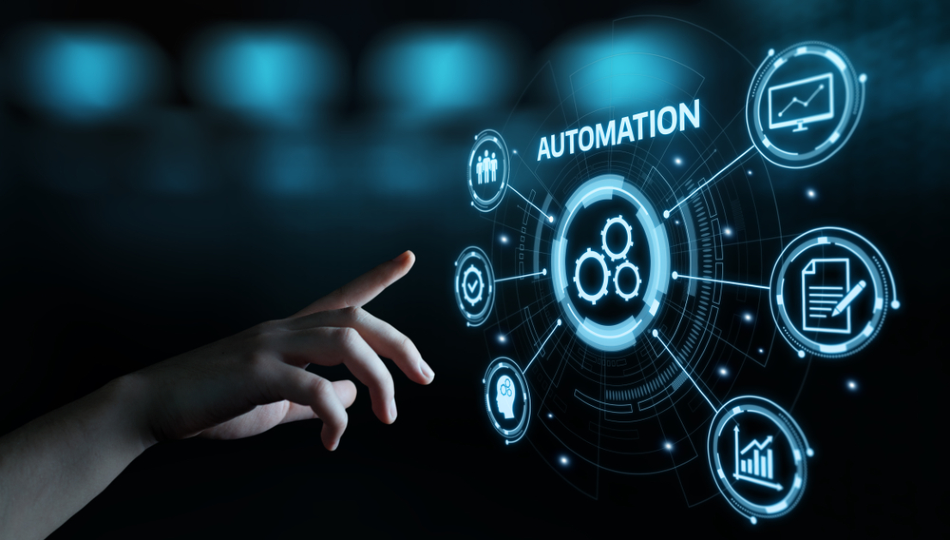
Image Credit: Alexander Supertramp/Shutterstock.com
Performing a task over and over again can be very monotonous, and finite elemental analysis is no exception. Automating the task can remove the monotony, but might it also introduce new problems into the process.
Finite Elemental Analysis
Finite elemental analysis, or FEA, is a type of computer program that utilizes the finite element method (FEM) to analyze materials or objects and find out how they are affected by applied stresses. It is a simulation of a physical phenomenon.
At the core of mechanical engineering and other disciplines, FEM is a numerical mathematical technique and a key principle used in the design of simulation software. The technique can determine points of weakness in a design before it is manufactured; it is used to reduce the number of physical prototypes and run virtual experiments to optimize components in the design phase, to develop better products faster.
Complex maths is employed to help us understand and quantify physical phenomena such as structural and fluid dynamics, wave propagation and thermal analysis. This is most often described using Partial Differential Equations (PDEs); these complicated equations need to be solved to compute relevant quantities of a structure - stresses and strains - to estimate a certain behavior of the investigated component under a given load.
But it’s more than just mathematical theory; by the 1950s FEA had developed enough to be used in real-world situations, with a focus on structural analysis. It is employed where multiple, highly variable equations are needed and was developed by engineers for engineers to address structural mechanical problems in civil engineering and aerospace.
FEA algorithms are integrated into simulation software, which is then integrated into computer-aided design (CAD) to make it easier for engineers to progress from design to running complex structural analysis.
How is it Done?
It requires a high level of expertise to obtain accurate and reliable from FEA. FEM is the most successful numerical means to analyze stresses and deformation in physical structures; its accuracy and reliability depend on the quality of the decisions made during the process and contextual information contained throughout.
The most time-consuming part of FEA is creating the analysis model. The first step is to generate a mesh; this mesh contains millions of small elements that make up the overall shape. It turns a three-dimensional object into a series of mathematical points that can be analyzed.
Calculations are then run for every single element or point on the mesh. These individual results are combined to make up the overall, final result for the structure. Engineers then know the value of certain points within the elements, but not every point; these are called nodal points and are often located at the boundary of the element.
The technique can provide information on stresses and strains, as well as the effects of vibration, fatigue and heat transfer.
Automation
Performing repetitive tasks is not desirable for a human workforce and it is tempting to automate all processes. But you have to be incredibly specific for it to work properly as every task or process is specific to the model you have and the industry you are in for example.
Engineering software can perform many tasks, but it is complex to use. Automation can help, but it only masks the complexity and reduces the decisions a user can make, many of which might be critical to the research. Automation might mean that the user does not know the desired level of accuracy to recommend.
However, automation can make FEA more efficient, and speed up the process by generating the final computer code. Complete automation provides algorithms for efficient and automatic computation of a system for given variables, finite element, and mesh. Researchers have demonstrated that by automatically generating and compiling efficient low-level computer code, you can parametrize a finite element code over the variational problem and finite element in addition to the mesh.
References and Further Reading
Disclaimer: The views expressed here are those of the author expressed in their private capacity and do not necessarily represent the views of AZoM.com Limited T/A AZoNetwork the owner and operator of this website. This disclaimer forms part of the Terms and conditions of use of this website.